15 Cost-Effective Decarbonization Strategies for Ships
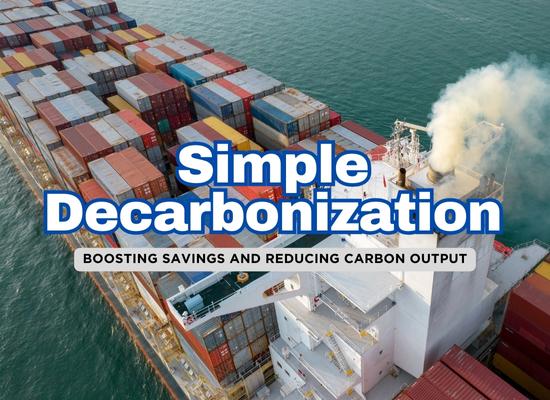
Decarbonization doesn’t always have to involve major investments or complex technology. Some strategies are simple, cost-effective, and can generate significant results. In this series, we'll break down the top 15 strategies, helping you understand the costs, savings, and real impact on your ship’s carbon footprint.
📝 View/Print Checklist
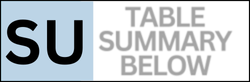
** We welcome your feedback, suggestions, corrections, and ideas for enhancements. Please email editor at shipuniverse.com **
ShipUniverse Quick Reference: Top 5 Affordable Decarbonization Techniques w/ Greatest Impact | |||
Strategy | Expense | Fuel Savings | Impact |
Energy Efficiency Training for Crew | $1,000 to $5,000 | 2% to 5% annually | Moderate to High |
Slow Steaming | Minimal operational cost | Up to 30% | Very High |
Energy-Efficient Lighting and Equipment | $5,000 to $30,000 | 1% to 2% of overall fuel consumption | Low to Moderate |
Hull Cleaning and Coating Optimization | $10,000 to $100,000 per maintenance cycle | 5% to 10% | High |
Route Planning and Weather Optimization | $10,000 to $50,000 annually | 5% to 10% | Moderate to High |
1️⃣ Energy Efficiency Training for Crew 🏋️
Crew energy efficiency training focuses on teaching operational practices that minimize fuel consumption and emissions. This includes:
- Engine Load Management: Avoiding overload or underload of engines to maintain efficiency
- Optimized Speed Adjustment: Matching speed with voyage conditions and fuel efficiency curves
- Fuel Efficiency Monitoring: Interpreting performance data in real-time to adjust for efficiency
- Voyage Planning: Incorporating route optimization and minimizing delays
Effective training programs can use digital simulations, on-board demonstrations, and continuous learning to keep the crew aware of efficiency targets.
Expense
- Cost Range: $1,000 to $5,000 per training session, depending on the size of the crew and training method
- Costs can be reduced if the training is developed internally with materials tailored to specific ship needs.
👉 Savings Note: Although upfront costs are low, maximizing impact may require periodic refreshers or access to real-time performance data.
Decarbonization Savings
Energy efficiency training alone can generate:
- Fuel Savings: 2% to 5% annually, depending on the crew’s adherence to best practices
- Carbon Emissions Reduction: Equivalent to 2 tons of fuel per day saved for large vessels burning 100 tons per day
Level of Impact
While this strategy won’t drastically reduce emissions on its own, it significantly enhances the impact of other measures, such as fuel-efficient technology. Trained crew members ensure that operational efficiency becomes a core part of daily ship activities.
2️⃣ Energy-Efficient Lighting and Equipment 💡
This strategy involves upgrading to energy-efficient lighting (such as LEDs) and other equipment, including pumps, HVAC systems, and onboard electronics. LEDs use far less energy than traditional incandescent or fluorescent lighting while providing longer-lasting performance. Similarly, energy-efficient machinery reduces the power needed for essential ship operations.
Common upgrades include:
- LED Lighting Installations in cabins, engine rooms, and passageways
- Energy-Efficient Motors and Pumps for systems like bilge and ballast water
- Smart Control Systems to optimize energy usage by adjusting power according to demand
Expense
- Cost Range: $5,000 to $30,000 per ship, depending on the extent of the upgrades
- LEDs have a higher upfront cost but last longer and require less maintenance. Upgrading motors and pumps may involve a higher investment but yields long-term savings.
Decarbonization Savings
- Energy Savings: Up to 10% of the ship’s auxiliary power consumption
- Fuel Reduction: For large ships, this can translate to a 1-2% overall fuel saving, depending on power usage patterns
- Carbon Emissions Reduction: Corresponds directly to lower fuel burn due to reduced power demand
Level of Impact
This strategy provides low to moderate impact on decarbonization but offers significant long-term cost savings. When combined with other energy-saving measures, it can create a compound effect on overall carbon reduction and operational efficiency.
3️⃣ Hull Cleaning and Coating Optimization 🛳️
Over time, hulls accumulate biofouling (marine growth like algae, barnacles, and slime), which increases drag and fuel consumption. Regular hull cleaning and applying advanced antifouling coatings help reduce drag, making the ship more fuel-efficient.
Hull optimization involves two main actions:
- Regular Hull Cleaning: Removing biofouling to reduce drag
- Advanced Coating Application: Using specialized coatings that prevent biofouling and maintain a smoother surface for longer periods
Expense
- Cost Range: $10,000 to $100,000 per maintenance cycle, depending on ship size and coating type
- Regular hull cleaning may cost less but needs more frequent application than advanced coatings, which last for several years.
Decarbonization Savings
- Fuel Savings: 5% to 10% on average, depending on the severity of biofouling
- Carbon Emissions Reduction: Significant due to reduced fuel consumption; for a large vessel burning 100 tons of fuel daily, a 10% improvement can reduce fuel use by 10 tons per day
Level of Impact
Hull cleaning and coating optimization provide a high impact on decarbonization due to the direct and substantial reduction in fuel consumption. This strategy is particularly effective when implemented consistently as part of regular maintenance.
4️⃣ Slow Steaming 🐢
Slow steaming is the practice of operating a ship at a reduced speed to lower fuel consumption. Since fuel consumption and emissions increase exponentially with speed, slowing down by just a few knots can lead to significant fuel and carbon savings.
This strategy became popular during periods of high fuel costs and has since been adopted as a decarbonization method. Ship operators may adjust schedules to account for slower transit times while optimizing cargo planning.
Expense
- Cost Range: Minimal upfront cost (mainly operational adjustments)
- Potential indirect costs include increased voyage time and scheduling changes, which may impact cargo contracts or port availability.
Decarbonization Savings
- Fuel Savings: Up to 20% to 30% for a reduction of 10% in speed
- Carbon Emissions Reduction: Directly proportional to fuel savings, making this one of the most impactful strategies
- For large vessels, reducing speed from 20 to 18 knots can lower fuel consumption by thousands of tons per year.
Level of Impact
Slow steaming provides a very high impact on decarbonization due to the exponential relationship between speed and fuel consumption. This strategy requires minimal investment but needs careful planning to manage operational schedules effectively.
5️⃣ Fuel Switching ⛽
Fuel switching involves changing from traditional heavy fuel oil (HFO) to lower-emission alternatives such as:
- Liquefied Natural Gas (LNG): Reduces CO₂, sulfur oxides (SOx), and nitrogen oxides (NOx) emissions
- Biofuels: Made from renewable sources like vegetable oils or algae, with a lower carbon footprint
- Methanol and Ammonia: Emerging fuels that emit significantly less or even zero CO₂
This strategy can be adopted for ships already equipped to handle alternative fuels or through engine modifications.
Expense
- Cost Range: $500,000 to $2 million+ for retrofitting or building ships with dual-fuel capabilities
- Operating costs depend on the availability and price of alternative fuels in key ports.
Decarbonization Savings
- Fuel Savings: Depends on fuel type, with biofuels offering up to 50% lower lifecycle emissions
- Carbon Emissions Reduction:
- LNG: Reduces CO₂ by 20% and SOx by nearly 100%
- Biofuels: Potential to reduce emissions by 40% to 70% depending on the source
- Methanol/Ammonia: Can achieve near-zero carbon emissions in the future with further development
Level of Impact
Fuel switching provides a high impact on decarbonization, especially for ships operating in emission control areas (ECAs) with strict sulfur and NOx limits. However, infrastructure challenges and fuel availability can limit widespread adoption.
6️⃣ Route Planning and Weather Optimization 🗺️
Route planning and weather optimization involve using advanced software and real-time weather data to determine the most fuel-efficient route for a voyage. Ships can avoid harsh weather, high-current areas, and other obstacles that increase fuel consumption. This strategy enhances both safety and efficiency.
Key components include:
- Weather Routing: Avoiding storms and high waves that increase drag and fuel use
- Optimized Currents: Utilizing favorable ocean currents to reduce engine load
- Traffic Avoidance: Minimizing delays and detours by navigating congested areas more effectively
Expense
- Cost Range: $10,000 to $50,000 annually for software licenses and satellite data services
- Relatively low setup costs with quick payback periods due to operational savings.
Decarbonization Savings
- Fuel Savings: Up to 5% to 10% per voyage depending on route and weather conditions
- Carbon Emissions Reduction: Corresponds to fuel savings, with potential reductions of several tons of CO₂ per day for large ships
Level of Impact
This strategy provides a moderate to high impact on decarbonization by reducing unnecessary fuel consumption on long voyages. It also improves the predictability of schedules, which can enhance overall operational efficiency and reduce costs.
7️⃣ Air Lubrication Systems 🌊
Air lubrication systems reduce friction between the ship's hull and the water by creating a layer of air bubbles underneath the vessel. This air cushion decreases hydrodynamic resistance, allowing the ship to move more efficiently and consume less fuel.
Key system types include:
- Air Release Panels: Installed along the hull to distribute air
- Compressor Systems: Generate and control airflow based on operating conditions
- Controlled Bubble Layers: Maintained under the hull to minimize drag
Expense
- Cost Range: $1 million to $5 million for installation, depending on ship size and system complexity
- High initial investment, with long-term savings that can justify the expense over the ship's lifetime.
Decarbonization Savings
- Fuel Savings: 5% to 10% on average, with potential for more depending on vessel design
- Carbon Emissions Reduction: Proportional to reduced fuel use, potentially saving thousands of tons of CO₂ annually on large ships
Level of Impact
Air lubrication systems offer a high impact on decarbonization by providing consistent fuel efficiency improvements. While the upfront costs are significant, the system can yield substantial savings and emissions reductions over time, especially on high-usage routes.
8️⃣ Regular Engine Maintenance and Tuning 🛠️
Regular engine maintenance and tuning ensure that a ship's engines run at peak efficiency, reducing fuel consumption and emissions. It involves routine checks, adjustments, and repairs to engine systems such as air filters, fuel injectors, and combustion components.
Key maintenance actions include:
- Engine Tuning: Adjusting settings for optimal fuel combustion efficiency.
- Fuel Injector Cleaning: Ensuring that fuel injectors are working at full efficiency.
- Air Filter Maintenance: Keeping air filters clean for optimal air-to-fuel ratios.
- Monitoring and Adjustments: Real-time data collection to ensure systems are running efficiently.
Expense
Cost Range: $10,000 to $50,000 for regular engine servicing, depending on ship and engine type.
Routine checks can be done as part of regular maintenance, and costs vary depending on the engine condition.
Decarbonization Savings
Fuel Savings: 3% to 7% annually due to improved combustion and less fuel waste.
Carbon Emissions Reduction: Proportional to fuel savings, leading to a decrease in CO₂ emissions.
Level of Impact
Regular engine maintenance has a moderate impact on decarbonization, but it’s a simple and effective strategy that can provide consistent long-term fuel savings and emissions reductions when properly maintained.
9️⃣ Engine and System Efficiency Upgrades ⚙️
Engine and system efficiency upgrades focus on enhancing the performance of main engines, auxiliary engines, and mechanical systems to reduce fuel consumption and emissions. These upgrades can include retrofitting existing engines with advanced components or implementing new technologies that optimize energy usage.
Examples include:
- Engine Tuning and Modifications: Adjusting engines for better fuel combustion efficiency
- Variable Frequency Drives (VFDs): Regulating the speed of electric motors to reduce energy waste
- Energy Recovery Systems: Reusing waste heat from engines to power other ship systems
Expense
- Cost Range: $200,000 to $2 million, depending on the scope of upgrades and ship type
- Costs vary with retrofitting complexity, but long-term fuel savings often provide a favorable return on investment.
Decarbonization Savings
- Fuel Savings: 5% to 15% depending on the efficiency improvements made
- Carbon Emissions Reduction: Substantial, as reduced fuel consumption directly translates to lower CO₂ emissions. Savings can reach thousands of tons annually on large ships.
Level of Impact
This strategy offers a high impact on decarbonization by improving fuel efficiency across critical systems. It can be particularly effective for older vessels needing modernization to remain compliant with stricter emissions regulations.
🔟 Ballast Water Optimization ⚓
Ballast water optimization involves adjusting how ballast water is managed to improve fuel efficiency and reduce drag. By minimizing excess ballast or redistributing it for optimal trim (the ship’s angle in the water), ships can reduce resistance, fuel consumption, and carbon emissions.
Key techniques include:
- Trim Optimization: Balancing ballast to ensure the ship operates at its most fuel-efficient trim angle
- Dynamic Ballast Management: Adjusting ballast based on voyage conditions and cargo load to reduce unnecessary weight
- Real-Time Monitoring Systems: Using sensors and software to optimize ballast levels and trim during a voyage
Expense
- Cost Range: $20,000 to $250,000 for software, sensors, and upgrades to ballast control systems
- Operational costs are minimal if optimization is part of regular ship management.
Decarbonization Savings
- Fuel Savings: 1% to 5% depending on how much optimization reduces drag
- Carbon Emissions Reduction: Proportional to fuel savings, reducing CO₂ emissions by several hundred tons annually on large vessels
Level of Impact
Ballast water optimization provides a moderate impact on decarbonization. While the direct savings may be smaller than other strategies, it supports overall fuel efficiency and is easy to implement alongside other decarbonization measures.
1️⃣1️⃣ Waste Heat Recovery and Utilization 🔥
Waste heat recovery systems capture heat generated by the ship’s main engines and use it to power auxiliary systems, reducing the need for additional fuel. This heat can be used for:
- Electricity Generation: Running a steam turbine to produce electrical power
- Heating Systems: Providing heat for onboard systems, such as fuel pre-heating or accommodation heating
- Freshwater Generation: Using heat for desalination through evaporators
By repurposing this heat, ships can improve overall energy efficiency.
Expense
- Cost Range: $500,000 to $3 million, depending on ship size and system complexity
- High initial investment, but long-term operational cost savings can provide a good return on investment.
Decarbonization Savings
- Fuel Savings: 5% to 15%, depending on the amount of waste heat utilized
- Carbon Emissions Reduction: Significant, as reduced fuel consumption directly decreases CO₂ emissions, potentially saving thousands of tons annually on large ships
Level of Impact
Waste heat recovery offers a high impact on decarbonization by improving overall energy efficiency and reducing reliance on auxiliary fuel consumption. This strategy is particularly beneficial for ships with high energy demand and long operational periods.
1️⃣2️⃣ Onshore Power Supply (Cold Ironing) ⚡
Onshore power supply, also known as cold ironing, allows ships to shut down their engines while docked by connecting to the local electrical grid. This eliminates the need to run auxiliary engines, which typically burn fuel to generate electricity while in port.
Key components include:
- High-Voltage Shore Connection (HVSC): Infrastructure to deliver grid power to the ship
- Ship Modifications: Upgrades to ship systems to accept shore power
- Port Facilities: Ports must provide compatible electrical supply to visiting ships
Expense
- Cost Range: $500,000 to $2 million per ship for retrofitting and equipment
- Costs also depend on the availability of shore power infrastructure at major ports. Some ports may offer subsidies or incentives to offset costs.
Decarbonization Savings
- Fuel Savings: 100% elimination of auxiliary engine fuel use while docked
- Carbon Emissions Reduction: Direct and substantial in port areas, where CO₂, sulfur oxides (SOx), and nitrogen oxides (NOx) emissions are reduced to nearly zero during berthing
Level of Impact
Cold ironing has a high impact on localized emissions and decarbonization, particularly in ports with strict environmental regulations. This strategy is crucial for reducing pollution in populated coastal areas and achieving compliance with emission control area (ECA) requirements.
1️⃣3️⃣ Digital Twin Technology and Performance Monitoring 🖥️
Digital twin technology creates a real-time virtual model of a ship, allowing operators to simulate and monitor performance under various conditions. Performance monitoring involves continuous data collection on engine efficiency, fuel consumption, trim, and other key factors, enabling proactive adjustments to improve efficiency and reduce emissions.
Key features include:
- Real-Time Data Integration: Sensors across the ship provide continuous data on critical systems
- Predictive Analytics: Simulations to predict how changes (e.g., speed, trim) will impact fuel efficiency
- Condition-Based Maintenance: Monitoring wear and performance to optimize maintenance schedules
Expense
- Cost Range: $100,000 to $1 million+ for hardware, software, and integration depending on ship size and complexity
- Ongoing costs for software licensing and data services apply but may be offset by operational savings.
Decarbonization Savings
- Fuel Savings: 5% to 15% through optimized operations and proactive decision-making
- Carbon Emissions Reduction: Directly tied to reduced fuel consumption, potentially saving thousands of tons of CO₂ annually for larger vessels
Level of Impact
Digital twin technology provides a high impact on decarbonization by offering full visibility into ship performance. By enabling real-time adjustments and simulations, it ensures that other efficiency strategies are executed optimally, leading to substantial long-term gains in fuel savings and emission reductions.
1️⃣4️⃣ Energy-Efficient Propulsion Upgrades 🚢
Energy-efficient propulsion upgrades enhance the ship’s propulsion system to reduce fuel consumption and emissions. These upgrades can involve improving the ship’s propellers, rudders, or engines to optimize hydrodynamic efficiency.
Common upgrades include:
- Optimized Propeller Design: Installing high-efficiency propellers or retrofitting existing ones with propeller boss cap fins
- Advanced Rudder Systems: Reducing turbulence and improving water flow with energy-saving rudder designs
- Hybrid Propulsion Systems: Integrating electric or dual-fuel engines to reduce fuel consumption
Expense
- Cost Range: $500,000 to $5 million depending on the upgrade and ship size
- Some upgrades, such as propeller retrofits, may have a lower upfront cost than complete engine overhauls.
Decarbonization Savings
- Fuel Savings: 5% to 20%, depending on the type and extent of upgrades
- Carbon Emissions Reduction: Significant reductions, as improved propulsion efficiency directly lowers fuel consumption. Savings can be as high as several thousand tons of CO₂ annually on large ships.
Level of Impact
This strategy provides a high impact on decarbonization by addressing one of the most critical fuel consumption areas—propulsion. While the upfront costs can be substantial, the long-term savings and emissions reductions make it a worthwhile investment, especially for older vessels.
1️⃣5️⃣ Renewable Energy Integration 🌞🌬️
Renewable energy integration involves using wind and solar technologies to reduce fuel consumption and emissions. These systems provide supplementary energy to either assist propulsion or power onboard systems, decreasing the load on the ship’s engines.
Key renewable technologies include:
- Rotor Sails: Vertical, spinning cylindrical sails that harness wind to generate additional thrust
- Rigid Sails: Large, foldable sails designed to capture wind power efficiently
- Solar Panels: Installed on large deck areas to provide power for auxiliary systems such as lighting, pumps, and HVAC
Expense
- Cost Range: $500,000 to $2 million depending on the system and ship type
- Rotor sails tend to have a higher upfront cost, while solar panels are more affordable for auxiliary power use.
Decarbonization Savings
- Fuel Savings: 5% to 10% depending on wind and solar usage
- Carbon Emissions Reduction: Proportional to fuel savings, potentially reducing several thousand tons of CO₂ annually for large vessels
Level of Impact
Renewable energy integration has a moderate to high impact on decarbonization by directly reducing engine workload. It is particularly effective when used alongside other strategies, such as slow steaming and route optimization, to maximize overall fuel efficiency.
Table Summary
ShipUniverse: Simple Decarbonization Strategies for Ships | |||
Strategy | What It Is | Expense | Impact and Savings |
Energy Efficiency Training for Crew | Training crew to manage fuel use efficiently through engine load optimization, speed adjustment, and real-time monitoring. | $1,000 to $5,000 per training session. Internal development can lower costs. | Fuel savings of 2% to 5% annually; reduces up to 2 tons of fuel per day for large vessels. Enhances other decarbonization efforts. |
Energy-Efficient Lighting and Equipment | Upgrading to LED lighting and energy-efficient machinery for onboard systems. | $5,000 to $30,000 depending on the scope of upgrades. | Up to 10% energy savings for auxiliary systems; potential 1% to 2% reduction in overall fuel consumption. |
Hull Cleaning and Coating Optimization | Reducing biofouling and drag by cleaning the hull regularly and applying advanced coatings. | $10,000 to $100,000 per maintenance cycle, depending on ship size and coating. | Fuel savings of 5% to 10%; significant carbon reductions by improving hydrodynamic efficiency. |
Slow Steaming | Operating the ship at reduced speed to lower fuel consumption and emissions. | Minimal upfront cost; mainly operational adjustments and schedule management. | Fuel savings of up to 20% to 30%; highly impactful on reducing emissions. |
Fuel Switching | Switching from heavy fuel oil (HFO) to lower-emission alternatives like LNG, biofuels, or methanol. | $500,000 to $2 million+ for retrofitting or dual-fuel systems. | Emission reductions of up to 70% depending on fuel type. Significant impact, though limited by fuel availability. |
Route Planning and Weather Optimization | Using advanced software and real-time weather data to find the most fuel-efficient route, avoiding harsh weather, high currents, and obstacles. | $10,000 to $50,000 annually for software licenses and satellite data services. | Fuel savings of 5% to 10% per voyage; reduces CO₂ emissions significantly by optimizing routes and avoiding delays. |
Air Lubrication Systems | Creating an air cushion under the hull to reduce drag, making the ship more fuel-efficient by generating a layer of air bubbles. | $1 million to $5 million for installation, depending on ship size and system complexity. | Fuel savings of 5% to 10%; potentially reduces thousands of tons of CO₂ emissions annually on large ships. |
Regular Engine Maintenance and Tuning | Routine checks, adjustments, and repairs to optimize engine performance, reducing fuel consumption and emissions. | $10,000 to $50,000 for regular servicing, depending on ship type and engine condition. | Moderate impact on decarbonization with long-term savings and emissions reductions. Fuel savings of 3% to 7% annually through improved combustion efficiency. |
Engine and System Efficiency Upgrades | Improving fuel efficiency by upgrading main and auxiliary engines, and implementing systems like variable frequency drives (VFDs) and energy recovery systems. | $200,000 to $2 million, depending on ship type and the scope of upgrades. | Fuel savings of 5% to 15%; substantial carbon emissions reduction, potentially saving thousands of tons of CO₂ annually. |
Ballast Water Optimization | Optimizing ballast water management by adjusting ballast levels and trim for improved fuel efficiency and reduced drag. | $20,000 to $250,000 for software, sensors, and system upgrades. | Fuel savings of 1% to 5%; significant reduction in CO₂ emissions, especially for large vessels. |
Waste Heat Recovery and Utilization | Capturing waste heat from the engine and using it to power auxiliary systems like electricity generation, heating, or freshwater production. | $500,000 to $3 million, depending on ship size and system complexity. | Fuel savings of 5% to 15%; significant CO₂ emissions reduction by improving overall energy efficiency. Ideal for ships with high energy demand. |
Onshore Power Supply (Cold Ironing) | Allows ships to shut down engines while docked by connecting to the local electrical grid, eliminating the need to run auxiliary engines. | $500,000 to $2 million per ship for retrofitting and equipment. | 100% elimination of auxiliary engine fuel use while docked; significant CO₂, SOx, and NOx reductions in ports with strict environmental regulations. |
Digital Twin Technology and Performance Monitoring | Creating a virtual model of the ship to monitor and optimize performance in real-time, including fuel consumption, engine efficiency, and trim adjustments. | $100,000 to $1 million+ for hardware, software, and integration. | Fuel savings of 5% to 15%; significant emissions reductions by ensuring that efficiency strategies are executed optimally. |
Energy-Efficient Propulsion Upgrades | Upgrading propulsion systems such as propellers, rudders, and engines to reduce fuel consumption and improve efficiency. | $500,000 to $5 million depending on the ship and the type of upgrade. | Fuel savings of 5% to 20%; substantial reduction in CO₂ emissions, especially for older vessels requiring modernization. |
Renewable Energy Integration | Using wind (e.g., rotor sails) and solar technologies to assist propulsion or power auxiliary systems, reducing engine load and fuel consumption. | $500,000 to $2 million depending on the system and ship type. Rotor sails are typically more expensive than solar panels. | Fuel savings of 5% to 10%; significant reduction in CO₂ emissions by decreasing engine workload. Most effective with other decarbonization strategies. |
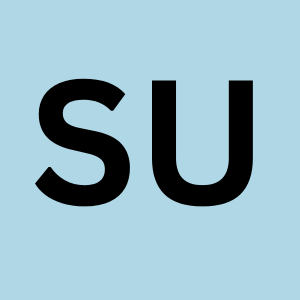
Do you have a Maritime Product or Service that may be of interest to Shipowners? Tell us about it here!
Do you have feedback or insights? Please reach out to editor @ shipuniverse.com