Mitigating Hull Stress in Ships: Innovative Solutions and Best Practices for Enhanced Structural Integrity
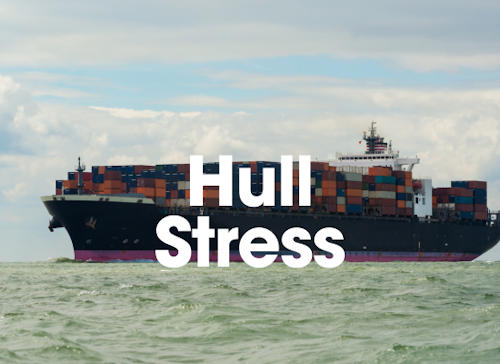
As shipping routes become more varied and environmental regulations stricter, the need for innovative solutions to monitor and manage hull stress has never been greater. This article explores the latest technologies and best practices that shipowners and operators can adopt to mitigate hull stress, thereby enhancing the longevity and safety of their vessels.
* Please send feedback/suggestions to editor @ shipuniverse.com
Understanding Hull Stress
Definition and Types
Dynamic Stress
Dynamic stress encompasses the forces that fluctuate as a ship navigates through varying environmental and operational conditions. These stresses arise due to the interaction between the vessel and its external surroundings:
- Waves: The impact of ocean waves hitting the hull generates bending, torsional, and shear stresses. These forces can vary significantly depending on wave height, frequency, and the direction relative to the ship's movement. For instance, large waves striking the bow can cause significant stress concentrations.
- Wind: Wind forces act on the ship's superstructure, creating additional pressure on the hull. High winds can lead to uneven loading, particularly when the vessel is in exposed positions, such as the open sea or coastal areas.
- Vessel Motion: The natural motion of the ship, including rolling (side-to-side motion), pitching (up-and-down movement of the bow), and heaving (vertical movement), generates fluctuating loads on the hull. These movements cause the hull to flex and twist, resulting in dynamic stress that varies with the sea state and vessel speed.
Static Stress
Static stress is caused by the constant forces due to the ship's own weight and the weight distribution of cargo and ballast. Unlike dynamic stress, static stress remains relatively constant but varies with operational loading conditions:
- Cargo Weight: The load from cargo exerts a downward force on the hull. Uneven distribution or heavy cargo can lead to significant stress concentrations, particularly in areas with structural constraints. Proper loading practices are essential to manage static stress effectively.
- Ballast: Ballast water used to stabilize the vessel impacts the hull stress distribution. Changes in ballast water levels can affect the overall buoyancy and stability, leading to variations in static stress. Proper ballast management is crucial for maintaining balanced stress levels across the hull.
- Vessel Structure: The inherent weight of the shipβs structural components, including the hull, superstructure, and internal fittings, contributes to static stress. This structural weight remains constant but affects the distribution of static stress throughout the vesselβs operational life.
Causes of Hull Stress
Environmental Factors
Environmental conditions play a pivotal role in the development and fluctuation of hull stress. These factors introduce external forces that can significantly impact the vesselβs structural integrity:
- Rough Seas: High seas and swells create substantial dynamic forces as waves interact with the hull. The energy from these waves causes the ship to bend and flex, leading to areas of high stress, particularly at the bow and stern where wave impact is most pronounced. Ships navigating in rough seas must be designed to withstand these repetitive stress cycles to avoid structural fatigue.
- Heavy Weather: Severe weather conditions, such as storms and hurricanes, intensify the forces acting on the ship. High winds and turbulent waters increase dynamic stress and can lead to structural deformation if the vessel is not adequately designed or prepared for such conditions. Operational decisions to navigate away from severe weather can mitigate some of these stresses.
- Ice Conditions: Vessels operating in ice-covered waters face additional challenges due to ice impact and pressure. Ice floes and bergs exert concentrated forces on the hull, potentially causing significant damage and stress. Ice-strengthened hull designs and operational practices like ice navigation training are essential to manage these stresses effectively.
Operational Factors
Operational practices significantly influence hull stress by affecting both the dynamic and static stress levels. These factors are within the control of the shipβs crew and management:
- Cargo Loading/Unloading: Improper loading procedures or uneven distribution of cargo can lead to imbalances, causing areas of high static stress. For instance, overloading a particular section of the ship can create localized stress points, increasing the risk of structural damage. Ensuring balanced and secure cargo stowage helps distribute stress evenly.
- Ballast Management: Inadequate ballast management can disrupt the vesselβs stability and stress distribution. Uneven ballast can lead to excessive hull stress, especially in rough seas where the distribution of weight affects the vesselβs movement and stress levels. Effective ballast management ensures that the ship remains balanced and minimizes unnecessary static stress.
- Navigation: Navigating through challenging environments, such as narrow channels, shallow waters, or areas with strong currents, introduces dynamic stresses due to sudden maneuvers and changes in vessel speed. Precise and cautious navigation, aided by advanced navigational systems, helps reduce the dynamic stress on the hull, preventing long-term damage.
Innovative Solutions for Monitoring Hull Stress
Sensor Technologies
Strain Gauges
Strain gauges are a fundamental technology for real-time hull stress monitoring. These sensors are strategically attached to the hull at critical stress points and measure the strain (deformation) experienced by the ship's structure under various conditions.
- Functionality: Strain gauges detect minute changes in the hullβs shape caused by dynamic and static forces. They work by converting mechanical deformation into an electrical signal that can be analyzed to assess the level of stress and strain.
- Real-Time Monitoring: The data from strain gauges provides real-time insights into the stress distribution across the hull. This immediate feedback allows operators to take corrective actions promptly, such as adjusting speed, altering course, or redistributing cargo to mitigate excessive stress.
- Installation Example: A container ship operating on transoceanic routes equipped strain gauges at the keel and other critical points to continuously monitor bending and torsional stress during heavy weather conditions. This setup enabled the crew to make informed decisions to maintain structural integrity during rough sea states.
Fiber Optic Sensors
Fiber optic sensors represent an advanced method for precise hull stress measurement, offering several advantages over traditional strain gauges, including higher sensitivity and the ability to monitor large areas with fewer sensors.
- Functionality: These sensors use optical fibers embedded in the hull structure. As the hull undergoes stress, the optical fibers experience changes in light transmission, which are interpreted to determine the level and location of stress.
- Precision and Coverage: Fiber optic sensors provide highly accurate measurements and can cover extensive areas of the hull with a single fiber, making them ideal for detecting complex stress patterns and early signs of structural fatigue.
- Case Study Example: A large oil tanker used fiber optic sensors embedded along its length to monitor stress during transits through high-risk ice-covered waters. The sensors provided detailed information on stress variations, enabling the crew to adjust the ballast and navigation strategies to minimize the risk of ice-induced damage.
Data Analytics
Predictive Analytics
Predictive analytics, driven by AI and machine learning, plays a crucial role in anticipating hull stress-related issues before they become critical. By analyzing historical and real-time data, these systems can predict potential stress points and maintenance needs.
- AI and Machine Learning: These technologies analyze patterns from past voyages and current conditions to forecast stress levels. They can model different scenarios, such as varying sea states or cargo loads, to predict how these factors will impact hull stress.
- Proactive Maintenance: Predictive analytics enables proactive maintenance scheduling by identifying trends that indicate developing stress issues. This approach helps prevent structural failures and extends the operational life of the vessel by addressing stress-related problems before they escalate.
- Example Use Case: A bulk carrier used AI-based predictive analytics to analyze data from strain gauges and weather forecasts, predicting areas of high stress during upcoming storms. This allowed the crew to preemptively reinforce affected areas and adjust the vesselβs route to mitigate the predicted stress.
Real-Time Monitoring
Integrating data from sensors into a comprehensive real-time monitoring system provides continuous insights into hull stress, allowing for immediate adjustments to operational practices and navigational strategies.
- Integrated Systems: Real-time monitoring systems combine inputs from various sensors, including strain gauges and fiber optics, into a centralized dashboard. This integration allows for a holistic view of the vessel's structural health at any given moment.
- Operational Decisions: The real-time data helps in making informed operational decisions, such as altering speed, changing course, or modifying ballast levels, to respond to current stress conditions and maintain structural integrity.
- Implementation Example: A modern cruise ship implemented a real-time hull monitoring system that integrates data from sensors distributed across the hull. This system provided live stress metrics to the bridge, allowing the captain to make immediate adjustments during high-sea voyages to ensure passenger safety and vessel stability.
Best Practices for Managing Hull Stress
Design Considerations
Structural Reinforcement
When designing or retrofitting ships, incorporating structural reinforcement techniques is crucial for managing hull stress effectively. These techniques involve using materials and construction methods that enhance the hullβs ability to withstand dynamic and static forces.
- Advanced Materials: Utilizing high-strength steel, composite materials, or alloys that provide greater resistance to stress and fatigue. These materials can absorb and distribute stress more efficiently, reducing the likelihood of structural failures.
- Design Innovations: Incorporating design features such as reinforced frames, double hulls, or stress-distributing geometries. These designs help distribute stress more evenly across the hull, minimizing stress concentrations and extending the vesselβs operational life.
- Case Example: A new build oil tanker incorporated high-strength steel in its construction, along with a double-hull design. These enhancements provided increased resistance to dynamic stresses encountered during heavy sea states and improved overall structural integrity.
Retrofits
Upgrading existing vessels with modern reinforcement technologies can significantly mitigate hull stress, extending their service life and improving safety.
- Hull Strengthening: Retrofitting older ships with additional plating, reinforcing beams, or installing stress-relief panels. These modifications help distribute stress and reduce the impact of dynamic forces.
- Technological Upgrades: Adding modern monitoring systems, such as strain gauges or fiber optic sensors, to older vessels to provide real-time data on hull stress. This allows for better management of existing stresses and timely maintenance interventions.
- Case Example: An aging bulk carrier was retrofitted with reinforced beams and advanced stress sensors. These upgrades allowed the ship to continue operating safely under demanding conditions by providing enhanced structural support and monitoring capabilities.
Operational Strategies
Load Management
Effective load management practices are essential for minimizing static stress and ensuring the even distribution of forces on the hull.
- Balanced Loading: Ensuring that cargo is distributed evenly across the vessel to avoid creating areas of high stress. Using load management software to plan and verify cargo placement can help achieve optimal balance.
- Ballast Adjustment: Properly managing ballast water levels to maintain stability and minimize stress concentrations. Adjusting ballast based on sea conditions and cargo load can help mitigate both dynamic and static stresses.
- Example Strategy: A container ship used load management software to simulate various loading scenarios and determine the optimal cargo distribution, ensuring even weight distribution and reducing static stress on the hull.
Speed and Route Optimization
Adjusting the vesselβs speed and selecting optimal routes based on environmental conditions can reduce dynamic stress and enhance operational safety.
- Speed Control: Modifying speed to minimize the impact of waves and reduce dynamic forces. Lowering speed in rough seas or during heavy weather can significantly decrease hull stress.
- Route Planning: Choosing routes that avoid high-risk areas such as regions with severe weather, strong currents, or ice-covered waters. Using advanced navigational systems and weather forecasting to plan safer and more efficient routes.
- Example Strategy: A cruise ship employed AI-based route optimization software to avoid rough seas, adjusting its speed and course based on real-time weather data, thus minimizing hull stress and ensuring passenger comfort.
Maintenance and Inspections
Regular Inspections
Conducting routine inspections is critical for early detection of stress-related damage and ensuring the ongoing integrity of the hull.
- Inspection Frequency: Establishing a regular schedule for inspecting the hull, focusing on areas known to experience high stress. Using visual inspections, ultrasound, or other non-destructive testing methods.
- Documentation: Keeping detailed records of inspection findings, including any signs of stress damage such as cracks, corrosion, or deformation. This documentation helps in tracking the progression of issues and planning maintenance activities.
- Case Example: A tanker company implemented a bi-annual hull inspection protocol, using drones for visual inspections of hard-to-reach areas. This approach allowed for comprehensive assessments without the need for dry-docking, reducing costs and downtime.
Preventive Maintenance
Implementing preventive maintenance strategies based on stress monitoring data can help address potential issues before they escalate.
- Maintenance Planning: Using real-time and historical stress data to predict maintenance needs and schedule interventions accordingly. This proactive approach helps prevent unexpected failures and extends the vesselβs operational life.
- Repairs and Reinforcements: Conducting timely repairs on areas showing signs of stress damage, such as cracks or corrosion. Reinforcing these areas with additional materials or structural modifications to prevent further deterioration.
- Case Example: A bulk carrier used predictive maintenance software to analyze stress data and schedule hull inspections and repairs. This strategy minimized unexpected failures and reduced overall maintenance costs by focusing on high-risk areas.
Regulatory and Compliance Considerations
International Standards
Compliance with international standards and regulations is essential for managing hull stress effectively and ensuring the safety and operational readiness of commercial ships.
- IMO Regulations: Adhering to the International Maritime Organization (IMO) regulations related to hull integrity, including guidelines for hull design, construction, and maintenance.
- Classification Society Guidelines: Following guidelines from classification societies such as Lloydβs Register, ABS, or DNV GL, which provide standards for hull stress management and certification.
- Example Compliance: A shipping company updated its fleet maintenance protocols to meet the latest IMO regulations on hull inspection and reinforcement, ensuring that all vessels were compliant and certified for safe operation.
Certification and Documentation
Obtaining certification for hull stress management practices and maintaining thorough documentation are key to regulatory compliance and operational transparency.
- Hull Stress Certificates: Acquiring certification from classification societies that verify compliance with stress management standards. These certificates provide assurance to stakeholders that the vessel meets necessary safety criteria.
- Record-Keeping: Maintaining detailed records of stress monitoring data, maintenance activities, and inspections. These records support compliance with regulations and facilitate audits and inspections.
- Example Practice: A container shipping line implemented a digital documentation system that recorded all hull stress monitoring data and maintenance activities. This system streamlined regulatory compliance and provided easy access to historical data for audits.
Future Trends in Hull Stress Management
Advancements in Materials
The development and use of advanced materials offer new opportunities for enhancing hull strength and stress resistance.
- Composite Materials: The adoption of composites such as carbon fiber and advanced polymers for hull construction, which provide high strength-to-weight ratios and resistance to corrosion and fatigue.
- Smart Materials: Innovations in smart materials that can adapt to stress conditions, such as self-healing composites that repair micro-cracks and reduce the accumulation of stress damage.
- Future Example: A research project developing composite hull sections for a new class of cargo ships aimed at reducing weight and increasing resistance to dynamic and static stress, enhancing overall vessel performance.
Innovations in Monitoring Technologies
Emerging technologies in hull stress monitoring continue to evolve, providing more precise and comprehensive data.
- Integrated Systems: The development of integrated monitoring systems that combine various sensor technologies (strain gauges, fiber optics, etc.) to provide a complete picture of hull stress in real-time.
- Autonomous Inspections: Use of drones and autonomous underwater vehicles (AUVs) for conducting hull inspections, reducing the need for human involvement and enhancing the accuracy of inspections.
- Future Example: A future deployment of AUVs for conducting detailed underwater hull inspections on oil tankers, providing real-time data on stress-related damage and reducing the need for dry-docking.
Predictive Maintenance Models
AI and machine learning are transforming predictive maintenance, enabling more accurate forecasting and proactive stress management.
- AI Integration: Advanced AI models that analyze stress data to predict maintenance needs, optimizing maintenance schedules and reducing unexpected failures.
- Real-Time Adjustments: Systems that can make real-time adjustments to vessel operations based on stress predictions, such as altering speed or ballast levels to manage dynamic stress.
- Future Example: A shipping company using an AI-driven predictive maintenance platform to monitor stress levels and schedule maintenance for its fleet, reducing downtime and improving overall vessel reliability.
The continued development and adoption of advanced solutions for hull stress management underscore the importance of proactive measures in maintaining structural health. Embracing these innovations not only enhances operational performance but also aligns with the growing emphasis on safety and sustainability in maritime operations.
Aspect | Summary | Technologies/Practices | Real-World Example |
---|---|---|---|
Dynamic Stress | Stresses from external forces such as waves and wind acting on the ship during motion. |
- **Strain Gauges**: Measure deformation in real-time. - **Wave Prediction Systems**: Forecast wave impacts. |
Container ship crossing the Pacific monitors wave-induced stress using strain gauges. |
Static Stress | Stresses from internal forces such as cargo weight and ballast distribution. |
- **Load Management Software**: Ensures balanced cargo loading. - **Ballast Management Systems**: Optimize ballast distribution. |
Bulk carrier uses load management software to distribute cargo evenly, reducing stress concentrations. |
Environmental Factors | Factors like rough seas, heavy weather, and ice conditions that increase hull stress. |
- **Weather Forecasting**: Provides real-time updates. - **Ice Detection Sensors**: Monitor ice conditions around the ship. |
Oil tanker in Arctic uses ice detection sensors to navigate safely and reduce hull stress. |
Operational Factors | Operations such as cargo handling and navigation that affect hull stress. |
- **Route Optimization Software**: Avoids hazardous areas. - **Efficient Cargo Handling Practices**: Ensure even weight distribution. |
Container ship uses route optimization software to avoid rough seas, minimizing dynamic stress. |
Strain Gauges | Devices that measure the amount of strain (deformation) in the hull. |
- **Installation at Critical Points**: Placed at high-stress areas. - **Data Integration**: Linked to real-time monitoring systems. |
Large cargo ship installs strain gauges at keel and midship to monitor stress during voyages. |
Fiber Optic Sensors | Advanced sensors that provide precise measurements of hull stress through changes in light transmission. |
- **Extensive Coverage**: Monitors large hull areas. - **High Precision**: Offers detailed stress data. |
Ice-strengthened vessel uses fiber optics to measure stress from ice impact, improving hull safety. |
Predictive Analytics | Uses AI to forecast potential stress-related issues and schedule maintenance. |
- **AI Models**: Analyze past and real-time data. - **Maintenance Forecasting**: Predicts maintenance needs. |
Bulk carrier applies AI to predict stress during heavy weather, planning maintenance accordingly. |
Real-Time Monitoring | Combines data from various sensors to provide immediate feedback on hull stress. |
- **Integrated Dashboard**: Displays live stress data. - **Automated Alerts**: Warns of critical stress levels. |
Cruise ship uses a real-time monitoring system to adjust speed and course based on live stress data. |
Design Reinforcements | Structural enhancements to manage hull stress, including the use of advanced materials. |
- **High-Strength Steel**: Provides greater durability. - **Composite Materials**: Reduce weight and increase resistance. |
New oil tanker uses high-strength steel and composites in hull construction to handle stress better. |
Load Management | Ensuring proper cargo and ballast distribution to minimize stress concentrations. |
- **Cargo Planning Software**: Optimizes load distribution. - **Ballast Control Systems**: Adjust ballast for balance. |
Freight carrier uses advanced software for optimal cargo placement, reducing static stress on hull. |
Regular Inspections | Routine checks to detect early signs of stress damage and maintain hull integrity. |
- **Drones for Visual Inspections**: Assess hard-to-reach areas. - **Non-Destructive Testing**: Identifies stress without damaging hull. |
Tanker company performs bi-annual drone inspections to detect and address stress cracks early. |
Preventive Maintenance | Scheduled maintenance based on stress monitoring data to prevent major issues. |
- **Data-Driven Scheduling**: Uses real-time data to plan. - **Proactive Repairs**: Addresses stress issues before they escalate. |
Bulk carrier uses predictive data to perform maintenance, reducing unscheduled repairs and downtime. |
Regulatory Compliance | Adherence to international standards and guidelines for hull integrity and stress management. |
- **Compliance Software**: Tracks regulatory requirements. - **Certification**: Obtains necessary hull stress management certificates. |
Container line maintains digital compliance records, ensuring adherence to IMO regulations. |
Future Trends | Developments in materials, monitoring technologies, and predictive maintenance for better hull stress management. |
- **Composite Materials**: Lighter and stronger hull construction. - **Autonomous Systems**: Drones and AUVs for inspections. - **AI Maintenance Models**: Enhanced prediction and planning. |
Future cargo ship designs include smart materials that self-heal minor stress cracks. |
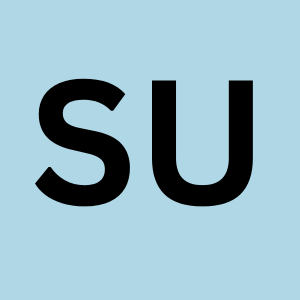
Do you have a Maritime Product or Service that may be of interest to Shipowners? Tell us about it here!
Do you have feedback or insights? Please reach out to editor @ shipuniverse.com