Ship Mooring Lines: Ultimate Guide
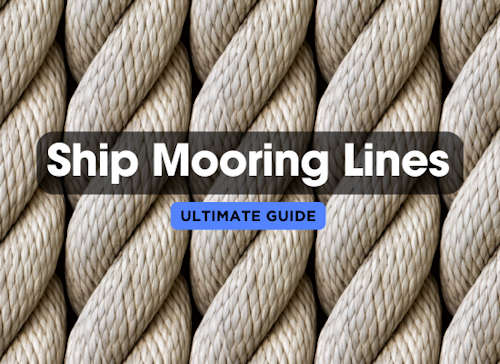
For shipowners and operators, choosing the right mooring lines is critical, as these lines not only affect the safety of the vessel but also have implications for operational costs and long-term maintenance. This guide provides an in-depth comparison of different mooring line materials, analyzing their strength, durability, cost, and other key factors to help you make informed decisions.
Quick Tips
Inspect Regularly: Conduct routine visual and tactile inspections to catch early signs of wear, such as fraying, stiffness, or discoloration.
Prioritize Safety: Replace mooring lines before they show significant wear to avoid unexpected failures during critical operations.
Rotate Usage: Rotate lines in use to distribute wear evenly across all mooring lines, extending their overall lifespan.
Monitor Load Impact: After incidents involving heavy loads (e.g., storms), inspect all lines for hidden damage that may not be immediately visible.
Document Everything: Keep detailed records of each line's purchase date, replacement history, and inspection notes to predict future needs.
Proper Storage: If possible store spare mooring lines in cool, dry, and shaded areas to protect them from UV exposure and moisture, ensuring they remain in good condition.
Crew Training: Ensure crew members are trained in proper handling, deployment, and storage techniques to minimize unnecessary wear and tear.
Plan Incremental Replacements: Replace mooring lines incrementally rather than all at once to manage costs and ensure a mix of new and older lines are always in service.
Check Compatibility: Ensure new mooring lines are compatible with existing winches, capstans, and mooring systems to prevent increased wear and ensure efficient operations.
Evaluate Line Appropriateness: Regularly assess whether the diameter and strength of your mooring lines are still appropriate for your ship's operational conditions.
Budget for Emergencies: Always have a budget for emergency line replacements to avoid downtime in case of sudden failures.
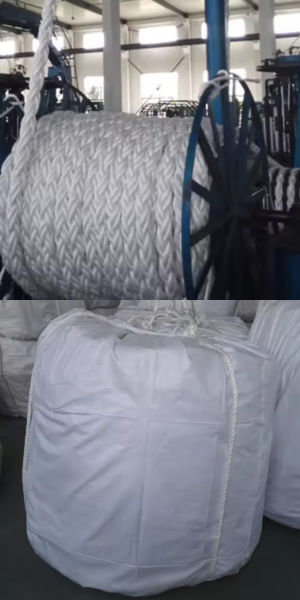
Factory Direct Pricing = Huge Savings
* High quality lines that are trusted by top fleets.
* Fully customizable according to your specs.
* Steel wire rope, PP, PES, Synthetic, in all sizes.
Mooring Line | 48mm | 56mm | 64mm | 72mm |
---|---|---|---|---|
8 Strand Polypropylene | $2.00 / kg | $2.10 / kg | $2.30 / kg | $2.40 / kg |
Ship Mooring Lines in-depth Comparison Tables
ShipUniverse: Comparison of Mooring Line Materials | ||||||
Material | Strength (Tensile Strength) | Stretch (%) | Lifespan (Years) | UV Resistance | Abrasion Resistance | Cost per Meter |
Nylon | High | 10-20% | 5-7 | Good | Good | $15 - $25 |
Polyester | High | 3-5% | 5-7 | Excellent | Excellent | $20 - $40 |
Polypropylene | Medium | 10-15% | 3-5 | Moderate | Moderate | $10 - $20 |
HMPE (Dyneema®) | Very High | <1% | 5-10 | Excellent | Excellent | $70 - $100 |
Aramid (Kevlar®) | Very High | <2% | 5-7 | Good | Excellent | $80 - $120 |
ShipUniverse: Strength and Load Capacity | |||
Material | Diameter (mm) | Breaking Load (kN) | Safe Working Load (kN) |
Nylon | 60mm | 580 - 640 kN | 145 - 160 kN |
Polyester | 60mm | 520 - 600 kN | 130 - 150 kN |
Polypropylene | 60mm | 400 - 480 kN | 100 - 120 kN |
HMPE (Dyneema®) | 60mm | 1,100 - 1,200 kN | 275 - 300 kN |
Aramid (Kevlar®) | 60mm | 950 - 1,050 kN | 237 - 262 kN |
ShipUniverse: Lifespan and Maintenance Frequency | ||||
Material | Average Lifespan (Years) | Recommended Inspection Frequency | Typical Signs of Wear | Replacement Guidelines |
Nylon | 5-7 | Monthly | Fraying, Loss of Elasticity, UV Degradation | Replace if significant fraying or elasticity loss is observed |
Polyester | 5-7 | Monthly | Abrasion, Surface Wear, Stiffness | Replace if severe abrasion or stiffness is detected |
Polypropylene | 3-5 | Monthly | Color Fading, Fraying, UV Degradation | Replace if color fading or significant fraying is present |
HMPE (Dyneema®) | 5-10 | Monthly | Internal Wear, Abrasion, Discoloration | Replace if internal wear or significant discoloration is observed |
Aramid (Kevlar®) | 5-7 | Monthly | Abrasion, Heat Damage, UV Degradation | Replace if heat damage or abrasion is severe |
ShipUniverse: Environmental Resistance | ||||
Material | UV Resistance | Saltwater Resistance | Chemical Resistance | Temperature Resistance |
Nylon | Good | Good | Moderate | Good |
Polyester | Excellent | Excellent | Good | Excellent |
Polypropylene | Moderate | Moderate | Poor | Moderate |
HMPE (Dyneema®) | Excellent | Excellent | Excellent | Good |
Aramid (Kevlar®) | Good | Good | Good | Excellent |
ShipUniverse: Cost Analysis of Mooring Lines | ||||
Material | Initial Cost per Meter | Total Cost for 2,200 Meters (10 Lines, 220m Each) | Annual Maintenance Cost | Total Cost Over 5 Years |
Nylon | $15 - $25 | $33,000 - $55,000 | $2,000 - $3,500 | $43,000 - $72,500 |
Polyester | $20 - $40 | $44,000 - $88,000 | $2,500 - $4,500 | $56,500 - $110,500 |
Polypropylene | $10 - $20 | $22,000 - $44,000 | $1,500 - $2,500 | $29,500 - $56,500 |
HMPE (Dyneema®) | $70 - $100 | $154,000 - $220,000 | $5,000 - $7,500 | $179,000 - $257,500 |
Aramid (Kevlar®) | $80 - $120 | $176,000 - $264,000 | $5,500 - $8,000 | $203,500 - $304,000 |
ShipUniverse: Elasticity and Energy Absorption | ||||
Material | Stretch Percentage Under Load | Energy Absorption Capacity | Impact on Mooring Stability | Best Use Cases |
Nylon | 10-20% | High | Good for absorbing shock loads | Rough seas, high dynamic loads |
Polyester | 3-5% | Moderate | Stable under consistent loads | Port mooring, calm waters |
Polypropylene | 10-15% | Moderate | Less stable under heavy loads | Temporary mooring, low-stress applications |
HMPE (Dyneema®) | <1% | Very Low | Excellent stability, minimal stretch | High-load situations, extreme conditions |
Aramid (Kevlar®) | <2% | Low | Good stability, low stretch | Specialized applications, heavy loads |
ShipUniverse: Handling and Operational Ease | ||||
Material | Weight per Meter (kg) | Ease of Handling (Subjective Scale) | Compatibility with Winches and Capstans | Crew Safety Considerations |
Nylon | 1.2 - 1.5 | Moderate | Good | Watch for snapback due to elasticity |
Polyester | 1.3 - 1.6 | Easy | Excellent | Safe, minimal snapback |
Polypropylene | 0.9 - 1.2 | Very Easy | Good | Monitor for UV degradation |
HMPE (Dyneema®) | 0.7 - 0.9 | Easy | Excellent | Minimal risk, low stretch |
Aramid (Kevlar®) | 1.0 - 1.3 | Moderate | Good | Careful handling to avoid abrasion |
ShipUniverse: Comparative Analysis of New vs. Used Ropes | ||||
Material | Condition | Cost Savings | Expected Lifespan Reduction | Risks and Considerations |
Nylon | New | N/A | N/A | Optimal strength and elasticity |
Nylon | Used | 30-50% | 2-3 years | Potential hidden damage, reduced elasticity |
Polyester | New | N/A | N/A | Full durability and resistance |
Polyester | Used | 25-40% | 2-4 years | Risk of surface wear, reduced lifespan |
HMPE (Dyneema®) | New | N/A | N/A | Maximum strength and minimal stretch |
HMPE (Dyneema®) | Used | 40-60% | 3-5 years | Internal wear may not be visible, reduced strength |
ShipUniverse: Global Availability and Sourcing | ||||
Material | Major Suppliers | Average Delivery Time | Regional Price Variations | Import/Export Regulations |
Nylon | USA, Europe, Asia | 2-4 weeks | Moderate | Customs duties in some regions |
Polyester | Europe, Asia | 3-5 weeks | Low | Minimal restrictions, widely available |
Polypropylene | Asia, South America | 2-3 weeks | Low | Generally no restrictions |
HMPE (Dyneema®) | Europe, USA | 4-6 weeks | High | Export controls in some regions |
Aramid (Kevlar®) | USA, Europe | 4-6 weeks | High | May require special licenses |
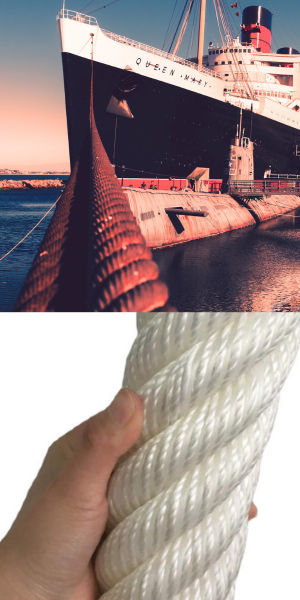
Factory Direct Pricing = Huge Savings
* High quality lines that are trusted by top fleets.
* Fully customizable according to your specs.
* Steel wire rope, PP, PES, Synthetic, in all sizes.
Mooring Line | 48mm | 56mm | 64mm | 72mm |
---|---|---|---|---|
8 Strand Polypropylene | $2.00 / kg | $2.10 / kg | $2.30 / kg | $2.40 / kg |
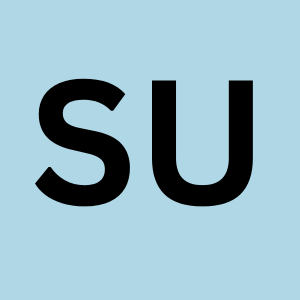
Do you have a Maritime Product or Service that may be of interest to Shipowners? Tell us about it here!
Do you have feedback or insights? Please reach out to editor @ shipuniverse.com