The Pros and Cons of Automated Mooring Systems
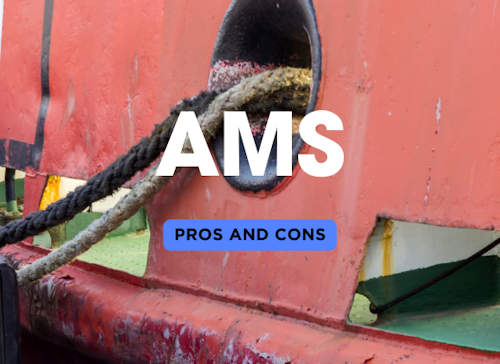
Automated Mooring Systems (AMS) have entered the maritime industry in hopes of replacing traditional mooring methods with high-tech, automated solutions. These systems use electric winches, sensors, and sometimes vacuum-based technology to secure ships to docks, reducing reliance on manual labor and improving efficiency. As ports and ships look to modernize and adopt greener, safer practices, AMS could become a key component in upgrading mooring operations. Let’s explore how AMS works both at the port and onboard the ship.
How AMS Works at a Port:
At ports, AMS replaces the need for manual mooring lines and heavy machinery with automated technology. Here’s how it works:
- Sensors and Control Systems: Once a vessel approaches the dock, sensors positioned on the port and the ship communicate with each other, guiding the ship into the correct mooring position.
- Electric Winches and Automated Arms: Some AMS setups use electric winches or automated arms to secure the vessel. These systems automatically adjust the tension to keep the ship in place, even during tidal changes.
- Vacuum-Based Systems (Optional): In certain ports, vacuum-based mooring systems like Cavotec’s MoorMaster are used. These systems create a vacuum to attach the ship to the dock, providing a quick and secure connection without the need for lines or manual adjustments.
- Centralized Control: The entire system is controlled via a centralized interface at the port, allowing operators to monitor the process and make adjustments as needed.
How AMS Works on a Ship:
Onboard the ship, AMS integrates with the ship's docking and mooring systems to simplify the process. Here’s how it functions:
- Automated Communication with Port: As the ship approaches the dock, onboard systems communicate with the port's AMS. This ensures the ship aligns correctly for docking.
- Automated Mooring Winches: Some ships are equipped with electric winches that adjust automatically based on real-time feedback from the port. The crew does not need to manually handle the lines or make adjustments during docking.
- Dynamic Positioning Systems: In more advanced setups, the ship's dynamic positioning system helps guide the vessel into position using GPS and sensor data. This ensures precision during docking, even in harsh weather conditions.
- Safety and Monitoring: Onboard sensors and cameras monitor the mooring process to ensure that everything is secure. The ship’s crew can monitor the entire operation from a control room, reducing the need for physical involvement on deck.
ShipUniverse: Pros and Cons of Automated Mooring Systems (AMS) at Ports | |
---|---|
Pros | Cons |
Increased Safety By automating the mooring process, AMS reduces the need for manual handling of heavy lines, significantly lowering the risk of injury to port workers and crew. |
High Initial Installation Costs AMS technology requires substantial investment upfront, including equipment, software, and potential infrastructure upgrades, making it costly for smaller ports. |
Faster Docking and Undocking Automated systems can secure a ship in minutes, speeding up port operations, reducing docking time, and minimizing vessel idle time, which saves money. |
Maintenance and Operational Costs AMS requires ongoing maintenance by specialized technicians, and any failure in the system could lead to costly delays and repairs. |
Reduces Manual Labor Requirements With AMS, ports need fewer dockworkers for mooring operations, lowering labor costs and reducing the need for dangerous manual tasks. |
Compatibility Issues Many older ports or smaller facilities may lack the necessary infrastructure to adopt AMS. Retrofitting can be expensive or impractical. |
Improves Operational Efficiency AMS systems optimize the docking process, making the entire port operation smoother, reducing human error, and increasing overall throughput. |
Vulnerability to Technological Failures Since AMS relies heavily on automation, any system failure—whether software, power outages, or mechanical issues—could disrupt operations, causing delays. |
Environmental Benefits Electric-powered AMS reduces emissions by eliminating the need for tugs and traditional mooring winches, helping ports meet sustainability goals and reduce their carbon footprint. |
Training and Skill Requirements Port staff need extensive training to operate AMS effectively, which requires time and resources. The complexity of these systems can make troubleshooting more difficult for untrained staff. |
Reduces Port Congestion By speeding up docking and undocking times, AMS allows more vessels to use the port in a given time frame, reducing congestion and improving scheduling. |
Limited Retrofitting Capabilities Older ports may struggle to retrofit AMS into their existing infrastructure, and the costs of such upgrades can be prohibitive for some ports. |
No Ship Modifications Needed: How Vacuum-Based Automated Mooring Systems Work
One of the major benefits of certain Automated Mooring Systems (AMS), particularly vacuum-based systems, is that they require no modifications or additional equipment on the ship itself. These systems operate entirely from the port side, using vacuum pads to securely attach to the hull of the ship.
How It Works:
When a vessel approaches the dock, the vacuum-based AMS activates from the shore. The system uses powerful vacuum pads to create a secure connection between the dock and the ship’s hull. These vacuum pads pull the ship toward the dock, holding it firmly in place without the need for traditional mooring lines or ship-based winches. The entire process is controlled from the port, eliminating the need for any onboard crew involvement.
Key Benefits:
- No Ship Modifications: Ships of any age or design can use vacuum-based AMS without the need for retrofits or special equipment onboard. This makes it highly versatile and easy to implement for all kinds of vessels.
- Enhanced Safety: The system eliminates the need for crew members to manually handle heavy mooring lines, reducing the risk of injuries during docking.
- Faster Docking: With the vacuum system in place, ships can be secured within minutes, speeding up the mooring process and reducing port congestion.
Drawbacks of Vacuum-Based Automated Mooring Systems
While vacuum-based Automated Mooring Systems (AMS) offer many advantages, such as faster docking and no ship modifications, they also come with some drawbacks. These limitations can impact the feasibility of adopting such systems at certain ports or for specific operational needs.
1. High Initial Installation Costs
- Why It’s a Drawback: The infrastructure required to set up vacuum-based systems like Cavotec’s MoorMaster is expensive. Ports need to install specialized vacuum pads, control systems, and sensors, which can require significant investment, especially in older ports that lack modern infrastructure.
- Impact: The high upfront costs can be a barrier for smaller or less frequented ports where the return on investment may take longer to realize.
2. Sensitivity to Hull Conditions
- Why It’s a Drawback: The vacuum pads must create a secure seal on the ship’s hull to work effectively. Ships with irregular or damaged hulls, or those with significant marine fouling, may struggle to form a proper seal, reducing the system's effectiveness.
- Impact: This can lead to delays or even the inability to moor certain vessels, especially older ships or those that haven’t undergone regular maintenance.
3. Dependence on External Power
- Why It’s a Drawback: Vacuum-based AMS relies on continuous electrical power to maintain the vacuum seal. Any power outage or electrical failure at the port could disrupt the mooring system, potentially causing the ship to drift or become unsecured.
- Impact: Ports need to have reliable power backups in place, such as generators, to ensure continuous operation of the mooring system.
4. Limited to Certain Docking Configurations
- Why It’s a Drawback: Vacuum-based systems are best suited for straight-line docking situations where the pads can easily reach the hull. For ports with more complex dock layouts or where vessels must be moored at an angle, the system may not function as effectively.
- Impact: Ports with non-standard docking configurations may face challenges using vacuum-based systems, limiting their application.
5. Maintenance Costs
- Why It’s a Drawback: Regular maintenance of the vacuum system is essential to ensure its functionality. Over time, wear and tear on the vacuum pads and sensors can lead to higher operational costs and downtime for repairs.
- Impact: Ports need to allocate resources for ongoing maintenance, which can add to the overall cost of using the system.
ShipUniverse: Pros and Cons of Automated Mooring Systems (AMS) on Ships | |
---|---|
Pros | Cons |
Increased Crew Safety AMS reduces the need for crew members to manually handle heavy mooring lines, lowering the risk of accidents and injuries on deck. |
High Installation Costs The initial cost of installing AMS onboard ships can be substantial, particularly for retrofitting older vessels with the necessary technology. |
Faster Mooring Operations Automated mooring systems speed up the docking process, reducing the time needed to secure the ship and allowing for quicker turnarounds in port. |
Maintenance Requirements AMS systems require specialized maintenance, and any malfunction may result in delays. The cost of repairs can be higher due to the need for skilled technicians. |
Reduces Crew Workload By automating the mooring process, AMS reduces the physical workload on crew members, freeing them up for other tasks and lowering fatigue levels. |
Training Requirements Ships' crews must be trained to operate the AMS correctly, which can take time and resources. Misuse or lack of knowledge can result in system failures. |
Increases Operational Efficiency AMS ensures precise and efficient mooring, reducing human error, and allowing for smoother operations both during docking and departure. |
Vulnerability to System Failures Automated systems, while advanced, are susceptible to power outages, software glitches, or mechanical failures, which can cause delays in operations. |
Improves Accuracy in Challenging Conditions AMS systems, especially those integrated with dynamic positioning, improve docking accuracy in difficult weather conditions such as high winds or strong currents. |
Compatibility with Ports Not all ports are equipped to support AMS, so ships may still require manual mooring methods in some locations, limiting the system's overall usefulness. |
Environmental Benefits By reducing reliance on tugs and other fuel-powered machinery, AMS helps reduce fuel consumption and emissions during docking procedures. |
Retrofit Challenges for Older Ships Retrofitting older ships with AMS can be technically challenging and expensive, requiring significant alterations to onboard systems and deck layouts. |
Traditional vs Automated Mooring
As the maritime industry continues to evolve, the debate between automated and traditional mooring systems is becoming more prominent. Traditional mooring, which relies on manual labor and physical handling of ropes and winches, has been the standard for centuries. However, the introduction of Automated Mooring Systems (AMS) has brought new opportunities for improving safety, efficiency, and sustainability at ports. Below is a detailed comparison of the two approaches, highlighting key aspects such as speed, safety, cost, labor requirements, and environmental impact.
ShipUniverse: Comparison of Automated vs. Traditional Mooring | ||
---|---|---|
Aspect | Automated Mooring | Traditional Mooring |
Speed | Automated systems can secure a ship within minutes, significantly reducing docking and undocking times. This leads to quicker turnaround times at ports, allowing for more efficient scheduling. | Traditional mooring is labor-intensive and can take up to 30 minutes or more, depending on the size of the ship and weather conditions. This results in longer docking times and potential delays. |
Safety | AMS greatly reduces the need for manual handling of heavy lines, significantly lowering the risk of injury to dockworkers and crew. The automation also reduces human error, improving overall safety. | Traditional mooring requires workers to handle ropes and winches, often in hazardous conditions. This manual process increases the risk of injuries from falling lines, slips, or handling equipment in bad weather. |
Cost | While AMS comes with high initial installation costs, it offers long-term savings through reduced labor costs and faster operations. Ongoing maintenance costs can vary based on the system. | Traditional mooring has lower initial costs but requires continuous labor expenses. Additionally, the longer mooring times can result in higher port fees due to extended docking durations. |
Labor Requirements | Automated mooring systems require minimal human intervention. Once installed, the system is operated by a few port staff, reducing the need for large crews and labor costs. | Traditional mooring requires a team of dockworkers and onboard crew to handle lines and operate winches, resulting in higher labor costs and potential for worker shortages. |
Environmental Impact | AMS typically uses electric-powered systems, which reduce the need for tugs and other fuel-based machinery, leading to lower emissions and contributing to greener port operations. | Traditional mooring often relies on tugs or diesel-powered winches, increasing fuel consumption and emissions, contributing to a higher environmental footprint. |
Energy Comparison
As ports and shipping companies move toward more sustainable operations, the energy consumption and environmental impact of mooring systems have become critical factors in decision-making. Traditional methods like manual rope mooring are labor-intensive but require little energy, while modern systems such as electric and vacuum-based mooring offer speed and efficiency but come with different energy requirements. This table compares the energy usage and environmental footprint of various mooring systems, helping you understand the trade-offs between traditional and automated solutions.
ShipUniverse: Energy Usage Comparison of Mooring Systems | |||
---|---|---|---|
System Type | Energy Consumption | Environmental Impact | Comparison to Traditional Mooring (Ropes) |
Electric Mooring Systems (e.g., winches powered by electricity) |
Electric mooring systems consume **moderate energy** based on vessel size and winch power. Energy usage is lower than diesel winches but higher than manual mooring with ropes. | These systems produce **no direct emissions** and are more environmentally friendly, especially when powered by renewable sources. They also generate less noise than diesel systems. | **Rope mooring requires no energy consumption** from machinery, but heavy manual labor is required. While it's energy-efficient in terms of power use, it's labor-intensive and slow. |
Vacuum-Based Mooring Systems (e.g., Cavotec's MoorMaster) |
Vacuum-based systems use **moderate energy** to maintain vacuum pressure. Overall energy use is lower compared to mechanical mooring systems but higher than traditional ropes. | These systems produce **no emissions** and eliminate the need for tugs, reducing fuel use and noise. Their carbon footprint is minimal, contributing to greener port operations. | Compared to rope mooring, vacuum systems are **much faster and safer**, although they consume more energy for the vacuum process. However, rope mooring doesn't require power, making it technically more energy-efficient but less efficient overall in speed and labor. |
Diesel-Powered Mooring Winches | Diesel-powered winches are **energy-intensive**, consuming large amounts of fuel, especially when securing larger vessels. They operate continuously during mooring, using significant amounts of diesel fuel. | These systems emit **greenhouse gases**, particulate pollution, and significant noise, contributing negatively to the environment. They also raise operational costs due to fuel use and emissions regulations. | Traditional rope mooring doesn’t require fuel, making it more energy-efficient on paper. However, rope mooring requires **tugboats** for larger vessels, which burns additional fuel, resulting in a higher overall environmental impact in complex scenarios. |
Manual Rope Mooring (Traditional Method) |
Rope mooring requires **no mechanical energy**, relying entirely on human labor. Energy use is effectively zero for the mooring process, but it requires significant manual effort and time. | While **no emissions** are produced from rope handling itself, **tugboats** used to assist large vessels can generate considerable emissions. Rope mooring is more sustainable for smaller vessels where tugs aren't needed. | Rope mooring is more energy-efficient but far **slower and labor-intensive** compared to automated systems. For large vessels, the need for tugs can raise the environmental footprint significantly. It's a lower-tech, lower-cost method, but at the expense of speed and safety. |
As the maritime industry continues to evolve, Automated Mooring Systems (AMS) are becoming an increasingly attractive option for ports and ship operators. While traditional rope mooring methods remain energy-efficient and cost-effective for smaller vessels, they are labor-intensive and slow. On the other hand, modern AMS technologies, such as electric and vacuum-based systems, offer significant improvements in speed, safety, and environmental impact, making them ideal for busy ports and large vessels.
The higher upfront costs and maintenance requirements associated with AMS can be offset by long-term benefits such as reduced labor needs, faster turnaround times, and lower emissions, particularly when electric or renewable energy sources are used. For ports seeking to improve efficiency and safety while contributing to greener operations, automated systems represent the future of mooring.
However, it’s essential to consider the specific needs of each port and vessel when choosing between traditional and automated mooring systems. While AMS technology provides clear advantages in many areas, the trade-offs in cost, energy consumption, and infrastructure should be carefully weighed before making the transition. In the end, adopting AMS can position ports and shipping companies to meet the growing demands of safety, efficiency, and sustainability in the global maritime industry.
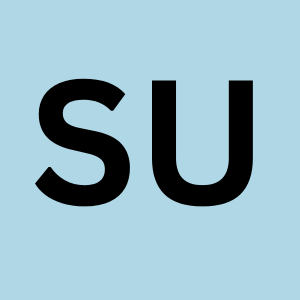
Do you have a Maritime Product or Service that may be of interest to Shipowners? Tell us about it here!
Do you have feedback or insights? Please reach out to editor @ shipuniverse.com