Maritime Disruptions: Top 30 Risk Mitigation Strategies
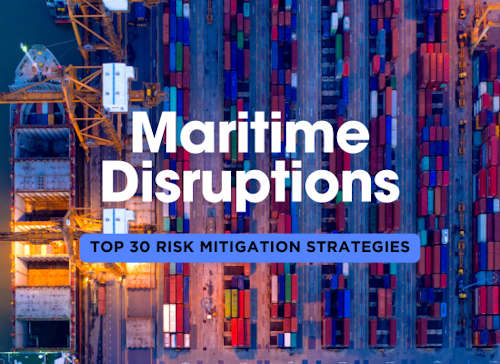
Maritime disruptionsβwhether caused by strikes, weather events, or logistical failuresβcan bring global supply chains to a halt, leaving ship and fleet owners scrambling to minimize losses. With the increasing complexity of global shipping, navigating these disruptions requires more than reactive measures; it calls for well-planned strategies that safeguard operations from unexpected delays and cost surges. This guide presents 30 key strategies to help you anticipate, prepare for, and respond effectively to maritime disruptions, ensuring your business remains resilient and competitive even in the most challenging times.
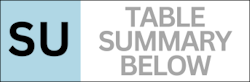
1. β Diversify Your Port Options
Problem: Relying on a single port can be a critical vulnerability, as strikes, congestion, or bad weather at that port could completely halt operations.
Solution: Use multiple ports across different regions to spread risk. Establish relationships with alternative ports to reroute shipments when needed. This ensures that, in the event of a disruption, you have options to keep cargo moving.
2. π¦ Build Up Safety Stock
Problem: Just-in-time delivery systems are particularly vulnerable during port disruptions, causing shortages and operational slowdowns when goods arenβt delivered on time.
Solution: Create a buffer by holding safety stock of essential goods. This allows your operations to continue even if there are delays in shipments, minimizing the impact of supply chain disruptions.
3. π Implement Real-Time Tracking
Problem: Without real-time tracking, you might miss critical updates on where your shipments are and how long delays might last, leading to a lack of information for decision-making.
Solution: Invest in GPS and IoT-enabled tracking systems for visibility into your cargo. This technology enables quick rerouting decisions, improves communication with stakeholders, and provides real-time updates on potential delays.
4. π Lock in Freight Rates Early
Problem: Freight rates can spike dramatically during a disruption, as available space on vessels becomes scarce, increasing costs.
Solution: Secure long-term contracts to lock in rates ahead of time. Negotiate flexible terms such as priority loading and rerouting capabilities to protect against price hikes and space shortages.
5. π€ Build Strong Relationships with 3PL Providers
Problem: During disruptions, finding flexible logistics solutions can be challenging, especially when all businesses are seeking the same alternatives.
Solution: Partner with reliable third-party logistics (3PL) providers who can offer alternative transport routes, scalable warehousing, and a wider network of shipping options to keep your cargo moving during disruptions.
6. πΌ Prepare for Demurrage Charges
Problem: Ships stuck in port due to strikes or congestion can quickly rack up demurrage charges, which are fees for exceeding the allotted time at the terminal. These costs can add up rapidly during prolonged delays.
Solution: Plan for potential demurrage costs in advance by incorporating them into your budget. Work with port authorities to expedite cargo movement and minimize time spent idling. Negotiating flexible terms in shipping contracts can also help reduce these charges.
7. π Utilize Multiple Transport Modes
Problem: When maritime routes are disrupted, relying solely on ocean freight can leave you vulnerable to significant delays.
Solution: Consider shifting cargo to alternative transport modes like air freight, rail, or trucking. While some alternatives may be more expensive upfront, they can save you from costly delays in critical shipments. Diversifying transportation options allows for more flexibility when sea routes are compromised.
8. π² Invest in Supply Chain Technology
Problem: A lack of visibility into supply chain operations can cause inefficiencies and delays in decision-making during a disruption.
Solution: Invest in supply chain management software and technologies that offer real-time tracking, automated reporting, and analytics. These tools provide insights into cargo movement and help you identify potential delays early, allowing you to act swiftly and optimize operations during disruptions.
9. π Maintain Transparent Communication with Clients
Problem: A lack of clear communication during disruptions can lead to frustration and lost business. Clients may become dissatisfied if theyβre uninformed about delays and potential delivery issues.
Solution: Keep clients informed about disruptions in real time. Provide regular updates through emails, automated notifications, or direct phone calls to explain the situation and what steps are being taken to minimize delays. Transparent communication helps manage client expectations and maintain trust during challenging times.
10. π’ Secure Additional Warehousing Space
Problem: During port disruptions, warehousing near affected areas becomes scarce, which can lead to skyrocketing storage costs and limited availability.
Solution: Secure additional warehousing space in advance, particularly in regions unaffected by the disruption. Locking in storage options before a strike or congestion occurs will give you the flexibility to manage delayed shipments and avoid last-minute cost hikes.
11. π Optimize Fuel Efficiency
Problem: Disruptions often lead to longer or rerouted voyages, increasing fuel consumption and costs.
Solution: Implement fuel-saving practices like slow steaming (reducing ship speed to save fuel) and optimize routing to avoid costly delays. Investing in fuel-efficient technologies or using cleaner fuel alternatives can also help manage costs during extended voyages caused by disruptions.
12. π‘οΈ Review Insurance Coverage
Problem: Maritime disruptions can result in cargo damage, delays, or even complete shipment losses, leading to unexpected financial burdens.
Solution: Review your insurance policies to ensure adequate coverage for potential losses due to disruptions, such as strikes, port closures, or weather events. Consider adding specific coverage for delays, disruptions, or demurrage to protect your business from unforeseen costs.
13. π Adjust Shipment Schedules Early
Problem: Once a disruption begins, adjusting shipment schedules can be difficult due to already congested logistics networks.
Solution: Be proactive by adjusting your shipping schedules as soon as you anticipate a potential disruption, such as labor strikes or severe weather events. Moving shipments up or rerouting cargo early can help you avoid the rush and keep your supply chain on track.
14. π§βπ€βπ§ Foster Relationships with Key Stakeholders
Problem: Disruptions can strain relationships with clients, suppliers, and partners, leading to potential long-term business damage.
Solution: Foster strong, transparent relationships with stakeholders by maintaining open lines of communication during disruptions. Offer regular updates and outline the steps youβre taking to manage delays and ensure delivery. This builds trust and keeps relationships intact during challenging times.
15. π Use Data Analytics to Forecast Disruptions
Problem: Not being prepared for disruptions due to a lack of predictive insights can cause businesses to be reactive rather than proactive, leading to higher costs and operational inefficiencies.
Solution: Use data analytics and predictive tools to forecast potential disruptions in your supply chain. These tools can help you anticipate issues based on historical data, current trends, or global events, allowing you to adjust your plans in advance and minimize negative impacts.
16. π§° Leverage Local Suppliers
Problem: Global disruptions can make it difficult to get goods from distant suppliers, delaying operations and increasing costs.
Solution: Build relationships with local suppliers to provide critical goods when international supply chains are disrupted. This reduces dependency on global shipping and can provide quicker, more reliable access to essential products, helping to maintain operations during longer disruptions.
17. π οΈ Invest in Fleet Maintenance
Problem: During disruptions, ships can be stuck in port or face longer voyages, increasing the wear and tear on your fleet. Neglecting maintenance during these times can lead to higher repair costs and longer downtime.
Solution: Prioritize routine maintenance during downtimes caused by disruptions. Use this time to perform essential repairs and upgrades to ensure your fleet is ready to operate efficiently once the disruption clears. This can reduce the likelihood of mechanical failures during critical periods.
18. π¨ Prepare Emergency Response Plans
Problem: Disruptions can quickly spiral into emergencies, leaving companies unprepared to manage escalating issues like significant delays, lost cargo, or safety concerns.
Solution: Develop comprehensive emergency response plans that address various types of maritime disruptions. This includes ensuring that your crew is trained for emergency scenarios, having a reliable communication plan in place, and knowing how to quickly access backup resources like additional vessels, rerouting options, or insurance assistance.
19. π‘ Strengthen IT Infrastructure
Problem: Outdated IT systems can struggle to handle the complexities of rerouting, tracking, and real-time decision-making during disruptions.
Solution: Upgrade your IT infrastructure to support advanced tracking, real-time communication, and data analytics. This helps to streamline decision-making during disruptions and ensures that your operations are responsive and agile in adjusting to the rapidly changing environment.
20. π Establish Flexible Contracts with Suppliers
Problem: Rigid contracts can prevent you from adjusting orders, delivery times, or terms in the face of disruptions, leading to costly penalties or missed opportunities.
Solution: Negotiate flexible contracts with your suppliers that allow for adjustments during unforeseen disruptions. This flexibility ensures you can change delivery schedules, order volumes, or shipment methods without incurring significant penalties, providing more leeway during unexpected disruptions.
21. π Diversify Global Sourcing
Problem: Relying too heavily on suppliers from one region leaves your supply chain vulnerable to regional disruptions such as strikes, political unrest, or natural disasters.
Solution: Diversify your sourcing by working with suppliers from different regions. This reduces the risk of supply chain bottlenecks when one area faces disruption, ensuring that your business has backup options in place for critical materials.
22. π Review Legal and Regulatory Requirements
Problem: Disruptions, especially those crossing international borders, can lead to legal complications if you are not up to date on regulations in different regions. These can delay shipments or even lead to penalties.
Solution: Regularly review and stay up-to-date on international shipping regulations, labor laws, and trade restrictions in all regions you operate. This ensures that you are prepared for potential legal challenges or changes during a disruption and can pivot your logistics strategy accordingly.
23. π Conduct Regular Risk Assessments
Problem: Without regular assessments, businesses may not fully understand their vulnerabilities to disruptions, leading to unanticipated risks and higher costs.
Solution: Conduct regular risk assessments of your supply chain to identify potential weak spots or overdependencies. Use this information to create contingency plans and allocate resources where they are needed most, ensuring you are better prepared for future disruptions.
24. π‘ Explore Alternative Shipping Routes
Problem: Traditional shipping routes may become congested or blocked during a disruption, leading to severe delays in cargo movement.
Solution: Explore and establish alternative shipping routes in advance. These could include smaller or less-used ports, different transport corridors, or even inland connections. Being able to quickly pivot to alternative routes can help maintain delivery schedules and reduce overall disruption impact.
25. πΌ Establish a Dedicated Disruption Management Team
Problem: Without a dedicated team focused on managing disruptions, companies may struggle to coordinate an effective response, leading to disorganization and slow reaction times.
Solution: Establish a dedicated team or assign key personnel to focus solely on managing maritime disruptions. This team should monitor real-time data, communicate with stakeholders, and make decisions quickly to reduce downtime and ensure that responses are well-coordinated across all parts of the business.
Successfully navigating maritime disruptions is about being proactive, adaptable, and informed. By implementing the strategies outlined in this guideβranging from diversifying your supply chain to leveraging cutting-edge technologyβyou can reduce downtime, manage costs, and maintain strong relationships with stakeholders during difficult periods. Disruptions may be inevitable, but with the right approach, you can ensure that your operations remain steady and your business continues to thrive, no matter what obstacles arise.
Table Summary
ShipUniverse: 30 Key Strategies to Navigate Maritime Disruptions | |
---|---|
Strategy | Description |
Diversify Your Port Options | Spread risk by using multiple ports across different regions to avoid relying on a single port that may be affected by strikes or other disruptions. |
Build Up Safety Stock | Maintain extra inventory of critical goods to ensure operations continue even if shipments are delayed. |
Implement Real-Time Tracking | Use GPS and IoT-enabled tracking systems to monitor cargo and make proactive decisions during delays. |
Lock in Freight Rates Early | Secure long-term contracts with freight providers to protect against rate spikes during disruptions. |
Build Strong Relationships with 3PL Providers | Work with third-party logistics providers who offer flexible transport and warehousing solutions during disruptions. |
Prepare for Demurrage Charges | Budget for potential demurrage fees and work to expedite cargo movement to avoid unnecessary costs. |
Utilize Multiple Transport Modes | Consider alternative transport options like air, rail, or trucking to minimize delays when maritime routes are disrupted. |
Invest in Supply Chain Technology | Implement digital tools to improve real-time visibility and decision-making during disruptions. |
Maintain Transparent Communication with Clients | Keep clients informed about delays with regular updates and proactive communication. |
Secure Additional Warehousing Space | Pre-book storage space at alternative locations to manage delayed shipments and avoid last-minute cost hikes. |
Optimize Fuel Efficiency | Use fuel-saving practices like slow steaming and optimize routes to reduce costs during longer voyages. |
Review Insurance Coverage | Ensure your insurance policies cover potential losses due to disruptions such as strikes or weather events. |
Adjust Shipment Schedules Early | Move shipments up or reroute cargo as soon as you anticipate a disruption to avoid congestion. |
Foster Relationships with Key Stakeholders | Maintain strong, open relationships with clients, suppliers, and partners to manage expectations during disruptions. |
Use Data Analytics to Forecast Disruptions | Leverage predictive tools to anticipate potential disruptions and adjust operations accordingly. |
Leverage Local Suppliers | Work with local suppliers to minimize dependence on international shipping during global disruptions. |
Invest in Fleet Maintenance | Use downtime during disruptions to perform necessary maintenance on your fleet and equipment. |
Prepare Emergency Response Plans | Develop a response plan to handle emergencies caused by severe disruptions, including crew training and access to backup resources. |
Strengthen IT Infrastructure | Upgrade your IT systems to support advanced tracking, communication, and real-time decision-making during disruptions. |
Establish Flexible Contracts with Suppliers | Negotiate flexible terms with suppliers to allow for adjustments during unforeseen disruptions. |
Diversify Global Sourcing | Source materials from multiple regions to avoid over-dependence on one area for critical supplies. |
Review Legal and Regulatory Requirements | Stay up to date on shipping regulations and labor laws to avoid complications during disruptions. |
Conduct Regular Risk Assessments | Evaluate your supply chain regularly to identify vulnerabilities and develop mitigation plans. |
Explore Alternative Shipping Routes | Establish backup shipping routes to reduce the impact of congestion and delays on traditional routes. |
Establish a Dedicated Disruption Management Team | Create a team focused on monitoring disruptions and implementing quick responses to minimize downtime. |
Plan for Temporary Labor Solutions | Develop relationships with temporary labor agencies to keep operations moving during strikes or labor shortages. |
Negotiate Force Majeure Clauses in Contracts | Ensure contracts include a force majeure clause to protect both parties from liability during major disruptions. |
Create a Maintenance and Repair Backup Plan | Establish a backup```html plan that includes mobile repair services or access to spare parts to reduce downtime during disruptions. |
Maintain Buffer Capacity in Your Fleet | Keep extra capacity in your fleet to allow for flexibility when adjusting shipping schedules or rerouting during disruptions. |
Invest in Training for Remote Operations | Train staff to manage operations remotely with cloud-based systems, ensuring smooth operations during disruptions when personnel canβt be onsite. |
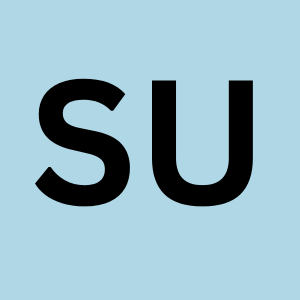
Do you have a Maritime Product or Service that may be of interest to Shipowners? Tell us about it here!
Do you have feedback or insights? Please reach out to editor @ shipuniverse.com