Revolutionizing Hull Cleaning: 20 Technologies That Could Save Millions
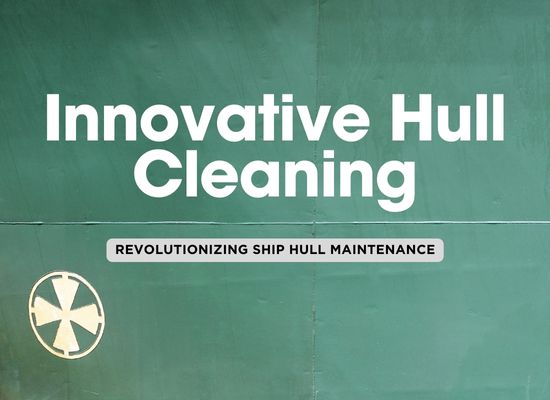
Maintaining a clean hull is crucial โ it enhances fuel efficiency, reduces maintenance costs, and helps avoid costly regulatory fines. Traditional methods like manual scrubbing and dry docking are being replaced by innovative cleaning technologies that minimize expenses by operating in transit, underwater, or autonomously. Let's get started with a rundown on the Top 20 innovate solutions in hull cleaning!
Disclaimer: Information provided is for general reference only. Costs, capabilities, and industry use may vary over time. Estimates are based on available data and may not reflect current market conditions. Please send any edits or suggestions to editor at shipuniverse.com
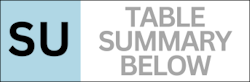
1. ๐ค Autonomous Hull Cleaning Robots
How It Works:
Autonomous hull cleaning robots attach to a shipโs hull and operate without human intervention. Using sensors, cameras, and AI-driven navigation, these robots move across the hull, cleaning biofouling with rotating brushes, suction pads, or water jets. They map out the surface to avoid obstacles, ensuring full coverage of the hull.
Estimated Cost:
High. Initial purchase costs range from $50,000 to $200,000, depending on the level of automation and cleaning technology. Maintenance costs are additional.
Industry Use:
Primarily used on large cargo ships, cruise ships, and tankers. These robots are ideal for ship operators looking to reduce downtime since cleaning can be done while ships are stationary or in port.
Potential:
- Fuel Efficiency: Clean hulls reduce drag, leading to fuel savings of 5-10%.
- No Dry Docking Required: Robots can clean the hull while the ship is in port or during short stops.
- Eco-Friendly: Eliminates the need for toxic anti-fouling paints or chemicals.
Drawbacks:
- High Upfront Cost: Requires significant investment in robotic technology.
- Ongoing Maintenance: Robot components like brushes and suction pads wear out over time.
- Limited Effectiveness in Harsh Biofouling Zones: May struggle in areas with extreme fouling.
2. ๐ก Ultrasonic Antifouling Systems
How It Works:
Ultrasonic systems prevent biofouling by emitting high-frequency sound waves that create micro-vibrations along the hullโs surface. These vibrations prevent biofilm and other marine organisms from attaching to the hull. The system typically consists of several transducers placed along key areas of the hull.
Estimated Cost:
Medium. Initial system costs range from $10,000 to $75,000, depending on vessel size and the number of transducers needed.
Industry Use:
Popular on yachts, smaller commercial vessels, and research ships. Larger ships are starting to adopt this technology as a preventative measure, especially in eco-regulated areas.
Potential:
- Prevention, Not Removal: Prevents biofouling before it happens, reducing the need for manual cleaning.
- Eco-Friendly: No chemicals, biocides, or physical coatings are required.
- Passive Cleaning: Operates continuously, requiring no crew intervention.
Drawbacks:
- Energy Use: System requires continuous power to emit sound waves.
- Limited Effectiveness on Heavy Fouling: Works best for light fouling but may struggle with barnacle growth.
- Coverage Gaps: May require multiple transducers to cover the entire hull, especially for large ships.
3. ๐งช Advanced Hull Coatings
How It Works:
Advanced hull coatings use slick, hydrophilic, or foul-release materials to prevent marine organisms from attaching. Materials like silicone or specialized polymers create ultra-smooth surfaces that reduce friction, making it difficult for biofouling to stick. Some coatings use "zwitterionic" technology to attract water molecules, forming a barrier that stops fouling organisms from attaching.
Estimated Cost:
Medium to High. Coating costs range from $10 to $40 per square meter, with total application costs for large vessels reaching $50,000 to $150,000. Dry dock time is required for application.
Industry Use:
Widely used on cruise ships, tankers, and container vessels. Companies looking to reduce drag and fuel consumption while also complying with zero-toxicity regulations are increasingly adopting these coatings.
Potential:
- Fuel Savings: By reducing drag, fuel consumption is cut by 5-10%.
- Long-Lasting: Coatings can last 5-10 years before reapplication is needed.
- Eco-Friendly: Unlike traditional anti-fouling paints, these coatings contain no harmful chemicals or biocides.
Drawbacks:
- Cost of Application: Ships must be dry-docked for the coating application, leading to downtime.
- Surface Preparation: Hulls must be completely clean before coating is applied, increasing initial labor costs.
- Limited to Light Fouling: Coatings prevent biofilm but may struggle with barnacle removal if already attached.
4. ๐ฟ Robotic Water Jet Crawlers
How It Works:
Robotic water jet crawlers attach to the shipโs hull using suction or magnetic tracks. As they move across the surface, they blast water at ultra-high pressure (20,000 - 40,000 psi) to remove fouling. The system can be controlled remotely, and some models offer autonomous navigation using sensors.
Estimated Cost:
Medium to High. Systems cost $30,000 to $100,000, plus costs for replacement nozzles and maintenance.
Industry Use:
Used on commercial cargo ships, tankers, and offshore support vessels. These crawlers are ideal for cleaning large hull areas that human divers or manual methods struggle to reach.
Potential:
- No Divers Required: Eliminates the need for diver-based hull cleaning.
- Removes Hard Fouling: The high-pressure jets can remove barnacles, mussels, and hard biofouling.
- Port-Side Use: Cleaning can be done at port, without dry docking.
Drawbacks:
- Coating Damage: High-pressure jets can strip anti-fouling coatings if used improperly.
- Water Usage: Uses large amounts of water, which may require treatment before discharge.
- Port Dependency: If used in port, permission from port authorities may be required.
5. ๐งฒ Magnetic Hull Cleaning Robots
How It Works:
Magnetic hull cleaning robots use powerful magnets to attach to the shipโs hull. As they move across the surface, they use rotating brushes, scrapers, or suction pads to dislodge fouling. These robots are either remotely operated or semi-autonomous, with sensors to detect and avoid obstacles.
Estimated Cost:
Medium to High. Systems range from $50,000 to $150,000, depending on automation, size, and brush system complexity.
Industry Use:
Used on container ships, tankers, and offshore platforms. Their magnetic grip allows them to clean vertical and curved areas of the hull that other systems can't reach.
Potential:
- Vertical Cleaning: Cleans vertical, curved, and even upside-down surfaces.
- No Divers Required: Eliminates diver intervention, reducing safety risks.
- Flexible Operation: Can be used at port or at sea.
Drawbacks:
- Weight and Deployment: Magnetic robots are heavy and require specialized handling.
- Speed of Cleaning: Slower than large-scale cleaning platforms, as they cover smaller areas.
- Brush Maintenance: Brushes and moving parts wear down over time and require regular replacement.
6. ๐คฟ Hull Cleaning ROVs (Remotely Operated Vehicles)
How It Works:
Remotely Operated Vehicles (ROVs) are underwater drones equipped with cameras, brushes, suction devices, and water jets. Operators control them from the surface to clean the hull in real-time. Some ROVs are semi-autonomous, meaning they can follow a pre-programmed cleaning path. They dislodge fouling with rotating brushes, suction, or high-pressure water jets.
Estimated Cost:
High. Full systems range from $50,000 to $500,000, depending on size, camera quality, and cleaning tools.
Industry Use:
ROVs are used by large shipping companies, offshore platforms, and naval fleets. Theyโre especially useful for deepwater hull inspections and cleaning where divers cannot operate safely.
Potential:
- Diver-Free Cleaning: Avoids the need for human divers, increasing safety.
- Inspections & Cleaning in One: Equipped with cameras, ROVs can perform visual inspections as well as cleaning.
- Reach Hard-to-Clean Areas: Can clean hard-to-reach spots that robotic crawlers and diver tools might miss.
Drawbacks:
- High Equipment Cost: Advanced ROVs with multi-function cleaning tools are expensive.
- Requires Skilled Operators: Operators must be trained in controlling ROVs, which increases labor costs.
- Slow Cleaning Speed: Cleaning large hulls takes longer compared to automated crawlers.
7. ๐งช Foul-Release Coatings
How It Works:
Foul-release coatings are slick, non-toxic coatings that make it difficult for fouling organisms to adhere. They don't kill biofouling organisms but prevent them from sticking to the hull. Silicone and other hydrophilic coatings create a slippery surface that causes barnacles, mussels, and algae to slide off as the ship moves through water.
Estimated Cost:
Medium to High. Coating costs range from $15 to $40 per square meter, with full application on large vessels costing $50,000 to $150,000.
Industry Use:
Used on cargo ships, tankers, and cruise liners. Companies seeking to reduce their use of biocidal anti-fouling paints are adopting these coatings as a sustainable alternative.
Potential:
- Fuel Savings: Reduced drag can result in 5-8% fuel savings.
- Eco-Friendly: No toxic chemicals or heavy metals are released into the water.
- Long-Lasting: Coatings typically last 5-10 years before reapplication is required.
Drawbacks:
- Requires Clean Hull: The hull must be thoroughly cleaned before application, adding prep costs.
- Application Downtime: Application must happen in a dry dock, which causes operational delays.
- Limited to Light Fouling: While effective at releasing biofilm, larger fouling like barnacles may require additional cleaning.
8. ๐ฟ Enzyme-Based Cleaning Systems
How It Works:
Enzyme-based cleaning systems use natural, biologically-engineered enzymes to break down the biofilm that allows biofouling organisms to attach to a hull. Enzyme solutions are sprayed onto the hull or injected into the surrounding water, where the enzymes degrade the sticky biofilm that marine organisms need to attach.
Estimated Cost:
Medium. Costs range from $5,000 to $25,000 per treatment, depending on vessel size and enzyme concentration.
Industry Use:
Primarily used in eco-sensitive environments and by companies aiming to reduce their reliance on chemical-based cleaning. These systems are common on smaller vessels and luxury yachts, but some larger ships are testing this method.
Potential:
- Eco-Friendly: Uses natural enzymes that break down biofilm without harming marine life.
- Non-Damaging: Does not harm coatings or anti-fouling paints.
- Reduced Diver Use: Enzymes do the work, reducing the need for human divers.
Drawbacks:
- Time-Consuming: Enzymes take time to degrade the biofilm, unlike fast-action brushes or jets.
- Reapplication Required: Multiple treatments may be required for complete cleaning.
- Environmental Sensitivity: Effectiveness may be reduced in very cold water or turbulent sea conditions.
9. ๐ฆ Biofilm-Resistant Coatings
How It Works:
Biofilm-resistant coatings prevent the formation of biofilm, the sticky layer of organic matter that marine organisms need to attach to the hull. These coatings use advanced polymers, zwitterionic materials, or hydrophilic substances that attract water molecules, forming a protective layer that biofilm canโt penetrate. Without biofilm, larger organisms like barnacles and mussels canโt attach.
Estimated Cost:
Medium to High. Coatings cost between $10 and $40 per square meter, with application costs for large ships totaling $50,000 to $150,000.
Industry Use:
Used on container ships, tankers, and cruise liners. Biofilm-resistant coatings are common for eco-friendly operators aiming to reduce chemical usage and improve hull performance.
Potential:
- Prevents Fouling at the Source: Stops biofilm formation, blocking the initial stage of fouling.
- Fuel Efficiency: Reducing biofilm reduces drag, improving fuel efficiency.
- Environmental Compliance: Non-toxic solution that helps companies meet zero-toxicity goals.
Drawbacks:
- Coating Cost: The ship must be in dry dock for the coating to be applied, increasing operational downtime.
- Surface Prep Required: The hull must be fully clean before the coating is applied, increasing labor costs.
- Limited to Preventative Use: Does not remove existing biofouling.
10. ๐ก UV-C Light Disinfection Systems
How It Works:
UV-C disinfection systems use ultraviolet (UV) light to kill biofouling organisms on the hull. UV-C light damages the DNA of fouling organisms, stopping them from reproducing or attaching. The system works by emitting UV-C light from underwater lamps that are attached to key points on the hull.
Estimated Cost:
High. Systems cost between $50,000 and $150,000, depending on ship size, number of UV lamps, and energy usage.
Industry Use:
Primarily used on luxury yachts, research vessels, and eco-friendly ship operators. UV-C technology is widely used in aquaculture and wastewater treatment, and its application in maritime hull cleaning is relatively new but promising.
Potential:
- Eco-Friendly: Uses light instead of chemicals or coatings, making it safe for marine life.
- No Physical Contact: No brushes or scrapers are needed, preserving anti-fouling coatings.
- 24/7 Operation: Operates continuously, offering protection even while the ship is at sea.
Drawbacks:
- Limited Large-Scale Use: While tested on smaller vessels, it is not yet widely adopted on large ships.
- High Energy Cost: The UV lamps must operate continuously, consuming power from the shipโs energy system.
- Lamp Degradation: UV-C lamps degrade over time and must be replaced periodically.
11. โก Electrolytic Hull Cleaning Systems
How It Works:
Electrolytic hull cleaning systems use a low-voltage electrical current applied to the hullโs surface. This current alters the electrochemical properties of the hull, making it less attractive to biofouling organisms. It disrupts the electrochemical process that allows barnacles, algae, and other marine life to attach to the hull. This system can be combined with cathodic protection to prevent corrosion as well.
Estimated Cost:
Medium to High. Installation costs range from $30,000 to $100,000, depending on ship size and the complexity of the system. Retrofitting older ships is more expensive than adding it to new builds.
Industry Use:
Used on large vessels such as tankers, offshore support vessels, and naval ships. It is often installed on newly constructed ships to avoid retrofit costs.
Potential:
- Dual Purpose: Prevents biofouling and corrosion simultaneously.
- Continuous Protection: Works 24/7 while the ship is at sea.
- Eco-Friendly: No toxic chemicals, biocides, or coatings are required.
Drawbacks:
- Energy Use: Requires constant electricity from the shipโs power system.
- Limited Retrofits: Older ships may require extensive electrical rewiring to support the system.
- Potential Interference: May interfere with certain hull coatings if not properly calibrated.
12. ๐ซง Microbubble Lubrication Systems
How It Works:
Microbubble systems release tiny bubbles of air under the shipโs hull, creating a cushion of air that reduces friction between the hull and water. This system is primarily designed to reduce drag and save fuel, but it also has secondary benefits for fouling prevention. The constant flow of air makes it difficult for fouling organisms to attach to the hull.
Estimated Cost:
Very High. Full systems range from $500,000 to $2,000,000, depending on ship size and the complexity of the air distribution system. Retrofitting is significantly more expensive than installations on new builds.
Industry Use:
Primarily installed on LNG tankers, cruise ships, and bulk carriers. It is often found on large vessels where fuel savings and operational efficiency are most critical.
Potential:
- Fuel Savings: Reduces water drag, leading to a 5-10% reduction in fuel consumption.
- Fouling Prevention: Constant airflow prevents fouling organisms from attaching.
- Environmentally Friendly: No chemicals, no physical cleaning, and reduced emissions from fuel savings.
Drawbacks:
- High Cost: Systems are expensive to install and maintain.
- Energy Usage: Air compressors must run continuously, consuming energy.
- Complex Retrofits: Retrofitting existing ships requires hull modifications, which can be costly.
13. ๐ฌ๏ธ Active Air Lubrication Systems
How It Works:
Active air lubrication systems are similar to microbubble systems but use larger bubbles or even a continuous layer of air across the hull. Compressed air is blown through multiple nozzles along the shipโs bottom, creating a thin air layer that reduces drag. The system requires active control of airflow to ensure consistent coverage.
Estimated Cost:
Very High. Full systems range from $1,000,000 to $3,000,000, depending on the shipโs size and number of air release points. Retrofitting is even more expensive.
Industry Use:
Primarily used on large cargo vessels, tankers, and cruise liners. It's being adopted by companies focused on fuel efficiency and emissions reduction.
Potential:
- Fuel Savings: Significantly reduces drag, saving 5-15% on fuel costs.
- Reduced Fouling: Constant air prevents fouling organisms from settling on the hull.
- Environmental Impact: Lower emissions from reduced fuel consumption.
Drawbacks:
- High Installation Cost: Installation is expensive, especially as a retrofit.
- Energy Use: Requires energy to operate the compressors continuously.
- System Maintenance: Air generators, nozzles, and pipelines require periodic maintenance.
14. โ๏ธ Plasma Cleaning Technology
How It Works:
Plasma cleaning technology uses ionized gases (plasma) to disrupt and destroy organic biofouling at the cellular level. Unlike water jets, brushes, or lasers, plasma cleaning doesn't require physical contact with the hull. Plasma energy disintegrates marine life and biofilm, leaving the hull clean.
Estimated Cost:
Very High. Plasma cleaning systems are still in the pilot stage, but initial estimates place costs around $200,000 to $500,000 for a fully functional system.
Industry Use:
Currently being tested on military ships, research vessels, and high-value commercial vessels. Adoption is still limited due to the high cost and relatively slow cleaning speed.
Potential:
- Contact-Free Cleaning: No risk of damaging anti-fouling coatings.
- Chemical-Free: No toxic biocides or cleaning agents required.
- Precision Cleaning: Capable of cleaning small, targeted areas with precision.
Drawbacks:
- Cost: Plasma systems are expensive to purchase and maintain.
- Slow Cleaning Speed: Plasma cleaning takes longer than brushes or high-pressure jets.
- Early-Stage Tech: Limited to pilot programs and controlled demonstrations.
15. ๐ Hydrodynamic Cleaning Systems
How It Works:
Hydrodynamic cleaning systems use water flow forces and specially designed appendages, fins, or plates on the hull to create turbulence. This turbulence naturally scrubs the hull as the ship moves through the water. Some systems use small, integrated cleaning devices that activate during the voyage, cleaning the hull in real time.
Estimated Cost:
Medium to High. Costs range from $20,000 to $75,000 depending on system type, ship size, and hull design.
Industry Use:
Used on ships that regularly travel long distances at higher speeds, such as cargo ships, ferries, and container ships. Systems are installed on new builds or during retrofits.
Potential:
- Self-Cleaning Hulls: Cleans while the ship is moving, reducing the need for port-side cleanings.
- Continuous Cleaning: Unlike traditional cleaning, it works every time the ship moves.
- Fuel Savings: Reduces drag, improving fuel efficiency.
Drawbacks:
- Limited to Ships in Motion: Only works when the ship is actively sailing.
- Maintenance: Fins, deflectors, and other hydrodynamic components require maintenance.
- Reduced Effectiveness at Low Speeds: Works best at higher sailing speeds.
16. ๐ก Sonic Wave Biofouling Prevention Systems
How It Works:
Sonic wave biofouling prevention systems emit low-frequency sound waves that disrupt the attachment of marine organisms like barnacles, algae, and mussels. These sound waves create vibrations along the hullโs surface, making it difficult for organisms to settle and form biofouling. Multiple transducers are placed along the hull, and the system runs continuously, providing non-stop protection.
Estimated Cost:
Medium. Initial installation costs range from $20,000 to $50,000, depending on ship size and the number of transducers required.
Industry Use:
Primarily used on smaller ships, fishing boats, and research vessels, but larger vessels are slowly adopting the technology to prevent fouling in areas where anti-fouling coatings are limited by environmental regulations.
Potential:
- Continuous Protection: Prevents biofouling 24/7, reducing the need for manual cleaning.
- Eco-Friendly: No biocides, chemicals, or toxic coatings are required.
- Reduced Maintenance: Prevents fouling before it starts, eliminating frequent cleaning needs.
Drawbacks:
- Limited to Light Fouling: More effective on biofilm and algae but less effective for hard barnacle growth.
- Energy Use: Requires continuous power, which may strain smaller ships' power supplies.
- Coverage Gaps: May require multiple transducers for full hull coverage, especially on large vessels.
17. โ๏ธ Multi-Purpose Cleaning Platforms
How It Works:
Multi-purpose cleaning platforms are port-side stations that combine multiple cleaning methods into one system. These platforms feature rotating brushes, high-pressure water jets, and suction systems in a single unit. Ships dock alongside the platform, and the system cleans large sections of the hull in one pass. These systems eliminate the need for divers or shipboard cleaning devices.
Estimated Cost:
High. Full systems cost $100,000 to $500,000, depending on platform capacity, water jet strength, and brush features.
Industry Use:
Used in shipyards, major ports, and dedicated cleaning facilities. Large shipping companies with multiple fleet operations use this technology to avoid costly diver-based cleanings.
Potential:
- Fast, Efficient Cleaning: Cleans large portions of the hull in a single pass.
- No Divers Required: Eliminates diver intervention, reducing labor costs and risk.
- Comprehensive Cleaning: Cleans biofilm, barnacles, and hard fouling at once.
Drawbacks:
- Limited to Port Locations: Ships must visit the port or shipyard with a cleaning platform.
- High Cost: Installation and maintenance costs are high for multi-purpose cleaning platforms.
- Operational Downtime: Ships must remain stationary during the cleaning process.
18. โก Cathodic Protection Systems
How It Works:
Cathodic protection systems use electrical currents to prevent corrosion and reduce fouling. This is achieved using two methods: sacrificial anodes (where the anodes corrode instead of the hull) and impressed current systems (where an electric current is applied directly to the hull to create an electrochemical shield). The system disrupts the ability of fouling organisms to bond with the hull's surface.
Estimated Cost:
Medium to High. Full system costs range from $30,000 to $100,000, depending on the shipโs size and system complexity.
Industry Use:
Commonly used on offshore support vessels, tankers, oil rigs, and large container ships. These systems are especially useful in areas where marine growth and corrosion occur simultaneously.
Potential:
- Corrosion Protection: Extends the lifespan of the shipโs metal hull.
- Continuous Protection: Operates 24/7, ensuring year-round fouling prevention.
- Eco-Friendly: No chemicals or coatings are used.
Drawbacks:
- Limited Fouling Prevention: More effective at preventing corrosion than biofouling.
- Ongoing Maintenance: Requires periodic inspection and replacement of sacrificial anodes.
- Power Use: Impressed current systems require continuous power to function.
19. ๐ ๏ธ Onboard Cleaning Systems with Self-Cleaning Hulls
How It Works:
Onboard self-cleaning systems use built-in cleaning mechanisms on the shipโs hull to clean biofouling as the ship moves. These systems can include micro-scrubbers, small jets of water, or air bubble devices that create turbulence. As water moves over the hull, the cleaning system disrupts the attachment of fouling organisms, allowing the hull to stay clean in real-time.
Estimated Cost:
Very High. Full systems cost $100,000 to $500,000, especially when integrated during new ship construction. Retrofits are significantly more expensive.
Industry Use:
Primarily used on research vessels, specialized military ships, and large commercial vessels that prioritize long-term hull cleanliness and operational efficiency.
Potential:
- Always On: Self-cleaning system works as the ship moves.
- No Dry Docking Needed: Eliminates the need for traditional hull cleaning during routine maintenance.
- Eco-Friendly: No brushes, chemicals, or diver involvement required.
Drawbacks:
- Costly Retrofits: Retrofitting an older ship with a self-cleaning system is costly.
- Energy Usage: Continuous operation increases the shipโs energy consumption.
- High Initial Cost: Cheaper to install during ship construction than retrofit.
20. Laser Ablation Cleaning Systems
How It Works:
Laser ablation cleaning systems use high-powered laser beams to vaporize biofouling organisms directly from the hull. The laser targets fouling at a microscopic level, disintegrating barnacles, algae, and biofilm without harming the underlying hull coating. Unlike physical brushes or water jets, lasers rely on precise energy pulses to remove fouling without direct contact.
Estimated Cost:
High. Full systems range from $100,000 to $500,000, depending on laser intensity, system size, and onboard integration.
Industry Use:
Currently used in military vessels, research ships, and advanced commercial vessels. The system is being tested for broader commercial shipping applications but is still in the early stages of adoption.
Potential:
- No Coating Damage: Unlike high-pressure water jets or brushes, lasers do not damage anti-fouling coatings.
- Chemical-Free: No need for chemicals, water, or consumables, making it an eco-friendly solution.
- Precise Cleaning: Lasers can target small, hard-to-reach areas of the hull with pinpoint accuracy.
Drawbacks:
- High Initial Cost: Purchase and installation costs are significant, especially for large vessels.
- Slow Cleaning Time: Laser cleaning is slower than water jets or large-scale brush systems.
- Still in Early Adoption: While effective, it is still being tested for large commercial fleets.
The world of hull cleaning is transforming with the rise of self-cleaning hulls, sonic wave prevention systems, and multi-purpose cleaning platforms. From autonomous robots to diver-friendly tools, ship operators have an arsenal of options to fight fouling, reduce drag, and improve fleet efficiency. The shift away from traditional methods like toxic coatings and diver scrubbing is part of a larger industry movement toward automation, sustainability, and operational efficiency.
These technologies provide multiple benefits, including:
- Fuel Savings: Many of these solutions reduce drag, improving fuel efficiency by up to 15%.
- Environmental Compliance: Eco-friendly methods like sonic waves, onboard self-cleaning systems, and advanced coatings help shipowners meet strict environmental regulations.
- Reduced Downtime: Technologies like onboard self-cleaning systems and port-side multi-purpose platforms ensure cleaning can happen without taking the ship out of service.
As regulations tighten and fuel prices rise, shipowners must consider how to keep their fleets as efficient, clean, and compliant as possible. These 20 technologies offer innovative, real-world solutions that save time, money, and the planet.
Table Summary
html Copy codeShipUniverse: 20 Hull Cleaning Technologies That Could Save Millions | ||||
Technology | How It Works | Estimated Cost | Industry Use | Potential & Drawbacks |
Autonomous Hull Cleaning Robots | AI-controlled robots attach to hulls, using brushes, jets, or suction to clean biofouling while avoiding obstacles. | $50,000 - $200,000 | Large cargo ships, cruise liners, tankers | Potential: Cleans during port calls, reduces downtime, saves 5-10% on fuel. Drawbacks: High cost, frequent maintenance for brushes/sensors. |
Ultrasonic Antifouling Systems | High-frequency sound waves create micro-vibrations on the hull, preventing biofouling organisms from attaching. | $10,000 - $75,000 | Yachts, fishing vessels, small cargo ships | Potential: Prevents fouling 24/7, no toxic coatings. Drawbacks: Limited on large vessels, only prevents foulingโnot removal. |
Advanced Hull Coatings | Specialized coatings create a slick, non-stick surface using polymers or hydrophilic materials that resist biofouling. | $10 - $40/sq meter | Tankers, cruise ships, research vessels | Potential: 5-10% fuel savings, long-lasting protection. Drawbacks: Dry-dock application required, costly reapplication. |
Robotic Water Jet Crawlers | High-pressure water jets blast biofouling off the hull while magnetic or suction tracks move the robot. | $30,000 - $100,000 | Bulk carriers, tankers, offshore vessels | Potential: No diver required, removes hard fouling. Drawbacks: High water usage, risk of damaging hull coatings. |
Magnetic Hull Cleaning Robots | Magnetically attach to the hull and use rotating brushes to clean vertical and curved areas. | $50,000 - $150,000 | Tankers, container ships, offshore support vessels | Potential: Cleans vertical hulls, no divers needed. Drawbacks: Heavy, slow cleaning speed, brushes wear out quickly. |
Hull Cleaning ROVs (Remotely Operated Vehicles) | Underwater drones equipped with brushes or jets to clean hulls remotely from shore or ship. | $100,000 - $500,000 | Offshore platforms, military ships, large fleets | Potential: No divers required, combined cleaning and inspection. Drawbacks: High cost, slow cleaning process, operator required. |
Foul-Release Coatings | Non-stick coatings that cause fouling organisms to โslip offโ when the ship moves through water. | $15 - $40/sq meter | Container ships, cruise ships, tankers | Potential: Self-cleaning with motion, eco-friendly. Drawbacks: Expensive, ineffective for heavy fouling. |
Enzyme-Based Cleaning Systems | Biologically active enzymes degrade biofilm and prevent biofouling organisms from attaching. | $5,000 - $25,000 per treatment | Research ships, luxury yachts, eco-sensitive vessels | Potential: No toxic chemicals, gentle cleaning. Drawbacks: Slow process, reapplication required. |
Biofilm-Resistant Coatings | Specialized coatings prevent the formation of biofilm, stopping fouling organisms before they attach. | $10 - $40/sq meter | Tankers, research ships, environmentally conscious fleets | Potential: Stops fouling at source, 5-10% fuel savings. Drawbacks: Requires pre-cleaning, limited hard fouling prevention. |
UV-C Light Disinfection Systems | UV light is used to kill marine organisms on the hull by destroying their DNA, preventing attachment. | $50,000 - $150,000 | Research ships, eco-focused operators | Potential: No chemicals, eco-friendly, constant protection. Drawbacks: High energy use, bulb replacement required. |
Electrolytic Hull Cleaning Systems | Low-voltage electrical current disrupts biofouling attachment and prevents corrosion. | $30,000 - $100,000 | Tankers, offshore support vessels, naval ships | Potential: Continuous fouling prevention and corrosion protection. Drawbacks: High energy usage, limited on older ships. |
Microbubble Lubrication Systems | Releases air bubbles under the hull to reduce drag and prevent fouling from attaching. | $500,000 - $2,000,000 | LNG tankers, cruise ships, bulk carriers | Potential: 5-10% fuel savings, less fouling. Drawbacks: High cost, compressor maintenance, retrofit issues. |
Active Air Lubrication Systems | Compressed air is blown along the hull to create an air layer that reduces drag and fouling. | $1,000,000 - $3,000,000 | Large cargo ships, tankers, cruise liners | Potential: Huge fuel savings, less fouling. Drawbacks: Expensive to retrofit, requires constant power for air compressors. |
Plasma Cleaning Technology | Ionized gas (plasma) disrupts and breaks down biofouling on a molecular level, similar to laser ablation but without physical contact. | $200,000 - $500,000 | Military vessels, research ships, experimental commercial vessels | Potential: No coatings needed, precise cleaning, no water required. Drawbacks: High cost, slow cleaning, still in testing phase. |
Hydrodynamic Cleaning Systems | Utilizes turbulence generated by specially designed hull shapes or appendages to clean biofouling as the ship moves through water. | $20,000 - $75,000 | Bulk carriers, ferries, container ships | Potential: Self-cleaning during movement, continuous operation. Drawbacks: Limited effectiveness at slow speeds, requires ship design changes for retrofits. |
Sonic Wave Biofouling Prevention Systems | Uses low-frequency sound waves to create micro-vibrations along the hull, preventing biofouling from attaching. | $20,000 - $50,000 | Fishing vessels, small cargo ships, research vessels | Potential: 24/7 protection, eco-friendly, no biocides. Drawbacks: Limited to light fouling prevention, multiple transducers required for large vessels. |
Multi-Purpose Cleaning Platforms | Port-side platforms with water jets, brushes, and suction systems that clean large sections of the hull in one pass. | $100,000 - $500,000 | Port facilities, shipyards, commercial fleet operators | Potential: Comprehensive cleaning, fast cleaning time, no divers required. Drawbacks: High setup cost, requires ships to visit a specific port, downtime during cleaning. |
Cathodic Protection Systems | Electrochemical system that prevents corrosion and limits fouling attachment by using sacrificial anodes or impressed electrical current. | $30,000 - $100,000 | Tankers, offshore support vessels, naval ships | Potential: Corrosion and fouling prevention, 24/7 protection. Drawbacks: Limited fouling prevention, requires ongoing maintenance and power usage. |
Plasma Cleaning Technology | Ionized gas (plasma) breaks down biofouling on a molecular level. Unlike brushes or jets, plasma removes organisms without physical contact, protecting underlying hull coatings. | $200,000 - $500,000 | Military vessels, research ships, early-stage trials on commercial vessels | Potential: Precise, chemical-free cleaning, no water needed. Drawbacks: High cost, relatively slow process, limited commercial adoption. |
Hydrodynamic Cleaning Systems | Uses engineered hull shapes, fins, or plates to create turbulence as the ship moves. This turbulence helps dislodge fouling naturally, reducing drag and maintaining a cleaner hull. | $20,000 - $75,000 | Bulk carriers, ferries, container ships (particularly new-build designs) | Potential: Continuous cleaning during normal operation, reduced downtime. Drawbacks: Less effective at low speeds, may require hull design modifications. |
Sonic Wave Biofouling Prevention Systems | Low-frequency sound waves create gentle vibrations along the hull, preventing the initial attachment of biofouling organisms like algae and barnacles. | $20,000 - $50,000 | Fishing vessels, small cargo ships, yachts, some research vessels | Potential: 24/7 passive protection, no chemicals, low maintenance. Drawbacks: Less effective against heavy fouling, multiple transducers may be needed for large hulls. |
Multi-Purpose Cleaning Platforms | Port-side platforms equipped with brushes, high-pressure jets, and suction systems that clean large hull sections quickly. Ships align with the platform in port for a one-stop cleaning solution. | $100,000 - $500,000 | Major ports, shipyards, large fleet operators seeking rapid turnaround | Potential: Comprehensive cleaning in a single pass, no divers needed, efficient port-side operation. Drawbacks: High setup cost, limited to port availability, requires docking time. |
Cathodic Protection Systems | Applies a small electrical current or uses sacrificial anodes to prevent corrosion. This altered electrochemical environment also makes it harder for biofouling organisms to attach. | $30,000 - $100,000 | Tankers, offshore support vessels, naval and commercial ships in corrosive waters | Potential: Corrosion prevention plus some fouling reduction, continuous protection. Drawbacks: Limited direct fouling prevention, requires maintenance and power supply. |
Onboard Cleaning Systems with Self-Cleaning Hulls | Built-in scrubbers, jets, or bubble emitters integrated into the hull design. As the ship sails, these systems continuously remove fouling before it becomes established. | $100,000 - $500,000 | New-build cargo ships, research vessels, eco-focused operators | Potential: No downtime for cleaning, reduced fuel costs, eco-friendly. Drawbacks: High installation cost, best suited for new builds, constant energy use. |
Laser Ablation Cleaning Systems | High-powered lasers precisely vaporize biofouling organisms without damaging hull coatings. Operates without water or chemicals, relying solely on concentrated laser energy. | $100,000 - $500,000 | Military vessels, research ships, pilot use in commercial fleets | Potential: No coating damage, eco-friendly, precise targeting of fouled areas. Drawbacks: High upfront cost, slower cleaning speed, technology still emerging for large-scale use. |
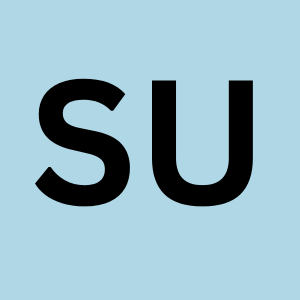
Do you have a Maritime Product or Service that may be of interest to Shipowners? Tell us about it here!
Do you have feedback or insights? Please reach out to editor @ shipuniverse.com