Underwater ROV Costs Explained: 15 Key Factors to Consider

The world of underwater remotely operated vehicles (ROVs) offers a wide range of options, with prices spanning from $5,000 to hundreds of thousands of dollars. This large cost variation can make it difficult to determine which features you truly need and which ones might be unnecessary for your specific application. Whether you’re inspecting ship hulls, managing underwater maintenance, or exploring the deep sea, understanding these key cost drivers will help you make the right decision.
This guide breaks down the top 15 factors that affect underwater ROV costs. You’ll learn how each feature impacts price, its pros and cons, and whether it’s essential for your needs.
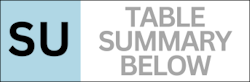
1. 🪢 Tethered vs. Untethered Systems
Tethered ROVs connect to the operator via a physical cable, providing a continuous power supply and a reliable data link. This makes them well-suited for extended operations and environments where signal interference is likely. Untethered systems, on the other hand, rely on advanced wireless communication or onboard autonomy, offering greater freedom of movement at the expense of operational range and complexity.
Pros:
- Tethered: Reliable data transfer, continuous power, and reduced downtime.
- Untethered: Greater mobility and the ability to access confined or complex environments without cable restrictions.
Cons:
- Tethered: Limited by cable length, susceptible to snags or tangles, and requires more setup.
- Untethered: Higher dependency on battery life and risk of losing communication in challenging underwater conditions.
Cost Driver:
- Cost Impact: 🔴 High
- Impact on Cost: Tethered systems are generally more cost-effective due to simpler technology, while untethered systems require sophisticated communication and power management, significantly raising their price.
- Cost Range/Estimate: Tethered: $5,000–$20,000; Untethered: $20,000–$100,000+.
2. 🤖 Autonomous Capabilities
Autonomous ROVs can perform tasks independently using advanced AI and navigation systems. They are ideal for large-scale or repetitive inspections where human intervention would be inefficient. Non-autonomous ROVs are operator-controlled in real time, making them better suited for precision tasks where direct oversight is necessary.
Pros:
- Autonomous: Reduces operator workload, improves efficiency, and allows for deployment in environments with limited communication access.
- Non-Autonomous: Easier to use for specific, real-time operations and significantly lower upfront costs.
Cons:
- Autonomous: High upfront investment and a steeper learning curve for operation and maintenance.
- Non-Autonomous: Requires constant operator engagement and is less effective for repetitive or large-scale tasks.
Cost Driver:
- Cost Impact: 🔴 High
- Impact on Cost: Advanced autonomy and AI systems dramatically increase costs due to the required software, sensors, and processing hardware.
- Cost Range/Estimate: Autonomous: $50,000–$200,000+; Non-Autonomous: $5,000–$50,000.
3. 📡 Sonar and Imaging Technology
Sonar and imaging systems are critical for underwater inspections, especially in low-visibility conditions. Sonar types vary from basic single-beam systems to high-resolution multi-beam setups capable of creating detailed 3D models. Advanced imaging cameras with low-light or thermal capabilities further enhance inspection accuracy.
Pros:
- Provides visibility and accuracy in turbid or deep waters.
- High-resolution imaging enables precise documentation and analysis.
Cons:
- Advanced sonar and imaging systems require specialized training.
- Adds significant cost, particularly for multi-beam or 3D sonar setups.
Cost Driver:
- Cost Impact: 🔴 High
- Impact on Cost: The complexity and resolution of sonar and imaging systems directly impact price. High-end sonar systems can cost as much as the ROV itself.
- Cost Range/Estimate: $2,000–$30,000+ depending on resolution and functionality.
4. 🌊 Depth Rating and Pressure Resistance
Depth rating determines how deep an ROV can safely operate without risking structural failure due to underwater pressure. Entry-level ROVs are often limited to shallow depths, while advanced models can reach several thousand meters. High-depth-rated ROVs are constructed using robust materials like titanium or specialized polymers, ensuring they can withstand immense pressures encountered in deep-sea environments. This factor is critical for tasks like deep-water exploration, pipeline inspections, or shipwreck studies.
Pros:
- Enables operations in deep and high-pressure environments, expanding use cases.
- High-quality construction ensures longevity and reliability even in extreme conditions.
Cons:
- Deep-rated ROVs are heavier and bulkier due to reinforced construction.
- Costs escalate significantly with increased depth capability.
Cost Driver:
- Cost Impact: 🔴 High
- Impact on Cost: Advanced materials, rigorous testing, and engineering drive up costs for ROVs rated for extreme depths.
- Cost Range/Estimate: $10,000–$200,000+, depending on depth capability (e.g., 300 meters vs. 6,000 meters).
5. ⚙️ Payload and Tooling Options
Payload capacity refers to the weight an ROV can carry, including additional tools like manipulator arms, sonar systems, or sample collectors. Tooling options, such as cutters or cleaning brushes, are often essential for specialized tasks, making the ROV more versatile. A higher payload capacity allows operators to customize the ROV for specific missions, such as underwater construction, repair, or biological sampling.
Pros:
- Expands the ROV’s functionality for a wide range of applications.
- Customizable payloads allow for mission-specific configurations.
Cons:
- Increased payload capacity requires more powerful thrusters, leading to greater energy demands.
- Adds complexity and maintenance requirements, especially with moving parts like arms or cutting tools.
Cost Driver:
- Cost Impact: 🟠 Mid
- Impact on Cost: Larger payload capacities and advanced tooling increase costs significantly but enhance operational capability.
- Cost Range/Estimate: $5,000–$50,000+ depending on the tools and payload weight.
6. 🎥 Camera Quality and Features
Cameras are the eyes of the ROV, capturing images and videos for inspections and data collection. Basic ROVs often feature HD cameras, while advanced systems include 4K resolution, low-light capability, thermal imaging, and even 360-degree coverage for a full field of view. Features like adjustable focus, zoom, and pan-tilt-zoom (PTZ) capabilities further improve functionality. These advancements are crucial for ship hull inspections, underwater archaeology, and detailed pipeline assessments.
Pros:
- High-resolution cameras enhance inspection accuracy and provide clearer data.
- 360-degree capabilities improve situational awareness, making navigation and inspection easier.
- Low-light and thermal imaging extend usability in challenging conditions.
Cons:
- High-end cameras significantly increase upfront costs.
- Advanced features may require additional processing power and operator expertise.
Cost Driver:
- Cost Impact: 🟠 Mid
- Impact on Cost: Advanced camera systems with 4K, low-light, or 360-degree capability add substantial cost, especially for professional-grade imaging solutions.
- Cost Range/Estimate: $1,000–$20,000+ depending on resolution, features, and functionality.
7. 🔋 Battery Life, Power Supply, and Range
Battery life and power supply determine how long an ROV can operate on a single charge, which is especially important for ship inspections that may require extended operations. Tethered ROVs often bypass battery limitations with a continuous power source, while untethered systems rely heavily on onboard batteries. Advanced models may feature swappable or fast-charging batteries to minimize downtime. Range, in terms of distance from the operator, is another critical factor, particularly for untethered systems.
Pros:
- Longer battery life supports more comprehensive inspections without interruptions.
- Swappable batteries or tethered power ensure extended operations for large vessels.
- Advanced power systems improve reliability during detailed inspections.
Cons:
- High-capacity batteries can add weight and increase costs.
- Limited range in untethered systems can restrict their use for larger or hard-to-reach ships.
Cost Driver:
- Cost Impact: 🔴 High
- Impact on Cost: High-capacity batteries and advanced charging systems increase costs significantly, particularly in untethered models.
- Cost Range/Estimate: $2,000–$20,000+ depending on battery type and capacity.
8. 🧭 Navigation and Control Systems
Navigation and control systems help operators maneuver ROVs with precision, making them essential for detailed ship inspections. Basic models offer manual controls with visual feedback, while advanced ROVs feature GPS, gyroscopes, and autonomous navigation for complex tasks. Thruster configuration also impacts control, especially in challenging conditions like strong currents or confined spaces under a ship’s hull.
Pros:
- Precise navigation allows for thorough and accurate inspections, even in tight spaces.
- Advanced systems with autonomous features reduce operator workload.
- Thrusters designed for high maneuverability are ideal for inspecting under-hull areas.
Cons:
- Advanced navigation systems increase costs and may require specialized training.
- Highly automated systems can reduce operator control in unpredictable environments.
Cost Driver:
- Cost Impact: 🟠 Mid
- Impact on Cost: GPS, gyroscopes, and autonomous navigation features add to the cost but are valuable for efficient and accurate inspections.
- Cost Range/Estimate: $1,000–$15,000+ depending on system complexity.
9. 🛠️ Build Quality, Materials, and Durability
The construction quality and materials of an ROV directly affect its ability to handle the rigors of ship inspections, which often involve abrasive surfaces, tight spaces, and exposure to marine environments. High-quality materials like titanium and reinforced polymers ensure the ROV can withstand harsh conditions, while rugged designs reduce the risk of damage during operations.
Pros:
- Durable materials minimize wear and tear, extending the ROV’s lifespan.
- High-quality construction allows operation in tough inspection environments, including under large ships.
- Better resistance to impacts and corrosion reduces maintenance needs.
Cons:
- Premium materials increase weight, potentially impacting maneuverability.
- Higher upfront costs for rugged designs.
Cost Driver:
- Cost Impact: 🔴 High
- Impact on Cost: Using high-end materials like titanium or reinforced polymers significantly increases costs but ensures reliability in challenging environments.
- Cost Range/Estimate: $5,000–$50,000+ depending on material type and durability.
10. 💾 Software, Data Processing, and Integration
The software capabilities of an ROV are critical for ship inspections, as they enable real-time data processing, reporting, and integration with other systems. Basic models may include simple navigation and video streaming software, while advanced ROVs offer 3D mapping, defect detection algorithms, and integration with inspection management systems. Features like remote control via mobile apps or cloud data sharing are also becoming common.
Pros:
- Advanced software streamlines inspections with tools like automated defect identification.
- Integration with management systems improves documentation and workflow efficiency.
- Real-time processing provides instant feedback for quicker decision-making.
Cons:
- High-end software requires a steep learning curve for operators.
- Updates, licensing, and support can add ongoing costs.
Cost Driver:
- Cost Impact: 🟠 Mid
- Impact on Cost: Advanced software and AI features significantly increase the upfront cost, but they reduce long-term inspection time and labor costs.
- Cost Range/Estimate: $2,000–$30,000+ depending on functionality.
11. 🛡️ Maintenance, Support, and Warranty Costs
Maintenance and support costs are often overlooked but are crucial for long-term reliability, especially for ROVs used in demanding ship inspection scenarios. Maintenance includes routine checks, component replacements, and software updates. Extended warranties and dedicated support packages can further enhance operational reliability but come at an additional cost.
Pros:
- Reduces downtime through preventative maintenance.
- Extended warranties and support packages offer peace of mind.
- Access to manufacturer support ensures quick issue resolution.
Cons:
- Adds ongoing costs, especially for high-end models with complex systems.
- Dependence on manufacturer support can lead to delays if parts are not readily available.
Cost Driver:
- Cost Impact: 🟠 Mid
- Impact on Cost: Maintenance contracts, warranties, and replacement parts can increase the total cost of ownership, especially for premium ROVs.
- Cost Range/Estimate: $1,000–$10,000+ annually, depending on the complexity of the ROV.
12. ✅ Certifications, Compliance, and Safety Standards
Certifications and compliance with industry standards ensure that an ROV meets safety, reliability, and performance benchmarks. For ship inspections, compliance with classification societies like ABS, DNV, or Lloyd’s Register is often required. Certified ROVs come with assurances of quality but also tend to cost more due to rigorous testing and documentation.
Pros:
- Ensures compliance with industry regulations, critical for commercial operations.
- Increases confidence in the ROV’s reliability and safety.
- Often a prerequisite for working with large shipping companies or port authorities.
Cons:
- Certified models typically have a higher upfront cost due to testing and certification processes.
- Non-certified models may be sufficient for smaller, less regulated inspections, making the additional cost unnecessary in some cases.
Cost Driver:
- Cost Impact: 🔴 High
- Impact on Cost: Certification processes and compliance testing add significant cost but are essential for professional-grade ROVs used in regulated industries.
- Cost Range/Estimate: $2,000–$15,000+ depending on the certifications required.
13. 🛠️ Sensor Add-Ons and Customization Options
Sensor add-ons such as water quality analyzers, leak detectors, or ultrasonic thickness gauges enhance an ROV’s functionality, making it more versatile for ship inspections. Customization options, including additional lighting or specialized manipulators, allow operators to tailor the ROV to specific inspection needs, such as detecting hull cracks or assessing corrosion.
Pros:
- Expands the range of applications, making the ROV suitable for specialized tasks.
- Customization ensures optimal performance for specific ship inspection requirements.
Cons:
- Each add-on increases complexity and maintenance needs.
- Can significantly increase initial investment.
Cost Driver:
- Cost Impact: 🟠 Mid
- Impact on Cost: Sensor add-ons and custom features increase costs but add significant value for complex inspections.
- Cost Range/Estimate: $1,000–$20,000+ depending on the type and number of sensors or add-ons.
14. 🎓 Operational Training and User Expertise
Ship inspections often require operators to have a strong understanding of ROV controls and capabilities. Entry-level ROVs are relatively easy to use, while advanced systems demand significant training, especially for features like autonomous navigation, advanced cameras, or sonar imaging. Training packages or certifications from manufacturers can increase upfront costs but are essential for safe and effective operations.
Pros:
- Ensures safe operation and maximizes the ROV’s potential for inspections.
- Reduces the risk of errors or damage during complex tasks.
Cons:
- High-end ROVs require specialized training, which adds time and cost.
- Lack of expertise can limit the effectiveness of even the most advanced ROVs.
Cost Driver:
- Cost Impact: 🟢 Low
- Impact on Cost: While training adds to upfront costs, it is relatively minor compared to hardware or software expenses.
- Cost Range/Estimate: $500–$5,000+ depending on the level of training and certification required.
15. 💸 Resale Value and Lifecycle Costs
The resale value of an ROV depends on its brand, build quality, and the demand for its features. Lifecycle costs, including depreciation, maintenance, and upgrades, are critical considerations for those using ROVs in long-term operations like ship inspections. High-quality models with durable components tend to hold their value better and cost less in the long run.
Pros:
- High resale value can offset initial investment costs.
- Durable, well-maintained ROVs have lower lifecycle costs.
Cons:
- Budget models depreciate quickly and may lack long-term reliability.
- Resale value may vary significantly depending on market trends and technological advancements.
Cost Driver:
- Cost Impact: 🟠 Mid
- Impact on Cost: High-quality materials and features increase initial costs but can lead to better resale value and lower long-term expenses.
- Cost Range/Estimate: Depreciation varies but expect a 20–50% drop in value after 3–5 years for most models.
Investing in an underwater ROV for ship inspections involves balancing cost with functionality. While the price range can vary from $5,000 to hundreds of thousands of dollars, understanding the key factors driving these costs is essential to making an informed decision.
Whether you need advanced sonar for hull inspections, a tethered system for extended operations, or autonomous capabilities for hands-free navigation, each feature comes with trade-offs. By evaluating your specific needs and budget, you can prioritize the features that matter most and avoid overspending on unnecessary add-ons.
ROVs have revolutionized ship inspections by reducing risk and increasing efficiency. With the right balance of features and costs, they can be a powerful asset for maintaining and managing maritime vessels.
Table Summary
ShipUniverse: Underwater ROV Cost Factors Summary | ||||
Feature | Cost Rating | Description | Pros | Cons |
Tethered vs. Untethered Systems | High | Tethered systems rely on cables for power and data, offering reliability but limited range. Untethered systems are wireless or autonomous, providing greater mobility at a higher cost. | Reliable data transfer with tethered systems; untethered offers more freedom for complex environments. | Tethers can snag and limit range; untethered systems are costlier and battery-dependent. |
Autonomous Capabilities | High | Autonomous ROVs perform tasks independently using AI, while non-autonomous models require operator control. | Efficient for repetitive tasks; reduces operator workload. | Higher cost and learning curve for autonomous systems. |
Sonar and Imaging Technology | High | Sonar and cameras enable navigation and inspection in low-visibility environments. Advanced systems offer detailed 3D mapping. | High-resolution imaging improves accuracy; sonar works in murky water. | Costly and may require operator training for advanced features. |
Depth Rating and Pressure Resistance | High | Determines maximum operational depth, with higher ratings requiring advanced materials. | Enables deep-sea operations; ensures reliability in high-pressure environments. | Increased cost and weight for high-depth models. |
Payload and Tooling Options | Mid | Includes tools like manipulator arms or sensors, enhancing the ROV’s versatility. | Customizable for specific tasks like cleaning or sample collection. | Adds weight and complexity; higher energy demands. |
Camera Quality and Features | Mid | Basic models offer HD cameras; advanced options include 4K, thermal imaging, and 360-degree views. | Improves inspection detail; 360-degree cameras enhance situational awareness. | High-end systems add cost and processing requirements. |
Battery Life, Power Supply, and Range | High | Battery life determines operational time, while range is crucial for untethered systems. | Swappable batteries allow extended operations; tethered systems bypass battery limits. | High-capacity batteries increase cost and weight; untethered systems are range-limited. |
Navigation and Control Systems | Mid | Systems range from manual controls to advanced GPS and autonomous navigation. | Precise navigation supports detailed inspections; autonomous features reduce operator burden. | Advanced systems are costly and may limit manual control. |
Build Quality, Materials, and Durability | High | Premium materials ensure durability in harsh underwater conditions. | Reduces wear and tear; prolongs operational life. | Premium materials increase weight and upfront cost. |
Software, Data Processing, and Integration | Mid | Enables real-time data processing, 3D mapping, and integration with other systems. | Improves efficiency; advanced software enhances analysis. | Steep learning curve and high upfront costs for advanced software. |
Maintenance, Support, and Warranty Costs | Mid | Covers routine maintenance, warranties, and manufacturer support. | Ensures reliability and minimizes downtime. | Adds recurring costs; may depend on manufacturer availability. |
Certifications, Compliance, and Safety Standards | High | Ensures adherence to industry standards, required for commercial operations. | Enhances reliability; often required by major clients. | Certification processes increase cost. |
Sensor Add-Ons and Customization Options | Mid | Additional sensors enhance capabilities, such as detecting hull cracks or corrosion. | Expands functionality; supports specialized tasks. | Add-ons increase weight, complexity, and cost. |
Operational Training and User Expertise | Low | Training ensures safe and effective operation, especially for advanced systems. | Improves operator confidence and minimizes errors. | Adds upfront cost and time for training programs. |
Resale Value and Lifecycle Costs | Mid | High-quality models retain value; lifecycle costs include maintenance and depreciation. | Durable models lower long-term expenses; good resale value offsets initial costs. | Lower-quality models depreciate quickly; market demand affects resale. |
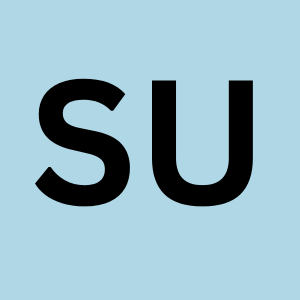
Do you have a Maritime Product or Service that may be of interest to Shipowners? Tell us about it here!
Do you have feedback or insights? Please reach out to editor @ shipuniverse.com