Hull Optimization Strategies in 2025: What’s Hot and What’s Cold?
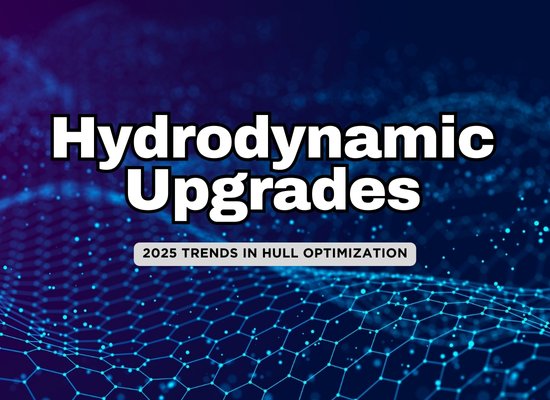
In 2025, shipowners face a critical challenge: balancing fuel efficiency, regulatory compliance, and operational costs while keeping vessels competitive. With rising fuel prices, stricter emissions rules, and advancements in maritime technology, hull optimization has never been more important.
But not every so-called "game-changing" upgrade delivers real results. Some proven technologies are gaining widespread adoption, slashing fuel costs and improving hydrodynamics. Others remain overhyped, experimental, or simply impractical for large commercial vessels.
So, what’s actually worth investing in? This guide breaks down the hottest hull optimization strategies in 2025—the ones delivering measurable efficiency—and exposes the cold, underwhelming ideas that still aren’t making waves.
Let’s dive in. 🚢🔥❄️
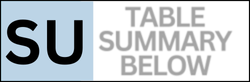
** We welcome your feedback, suggestions, corrections, and ideas for enhancements. Please email editor at shipuniverse.com **
ShipUniverse: Hydrodynamic Upgrades Voyage Savings Calculator
Select Upgrade: | |
Fuel Cost ($ per ton): | |
Voyage Distance (Nautical Miles): | |
Fuel Consumption (Tons per day): | |
Estimated Savings: - |
🔥 HOT (High Demand & Widespread Adoption)
1️⃣ Low-Friction & Anti-Fouling Hull Coatings 🔥
Enhancing Vessel Efficiency
In the maritime industry, low-friction and anti-fouling hull coatings are pivotal for enhancing vessel performance. These specialized coatings minimize drag by preventing marine organism accumulation on hull surfaces, leading to significant fuel savings and reduced greenhouse gas emissions. As of 2025, the global hull coatings market is projected to reach $12.9 billion, reflecting steady growth due to increasing environmental regulations and fuel efficiency demands.
Innovations Driving the Market
The industry is witnessing a shift towards environmentally friendly solutions. Companies are developing biocide-free, ultra-low friction coatings that not only enhance fuel efficiency but also comply with stricter environmental standards. Some modern coatings incorporate hydrogel technology, which significantly reduces hull-to-water friction. Other innovations include silicone-based and self-polishing coatings that improve long-term efficiency by maintaining a smoother hull surface.
Leading Industry Players
Several key players are at the forefront of this market:
- AkzoNobel N.V. – Offers a range of marine coatings designed for fuel efficiency and environmental compliance.
- PPG Industries Inc. – Provides advanced antifouling solutions, including biocide-free products that reduce CO₂ emissions.
- Jotun – Develops high-performance marine coatings with a focus on sustainability and durability.
- Hempel A/S – Invests in research to create innovative antifouling coatings that meet evolving environmental standards.
- Seacoat – Specializes in silane-siloxane-based coatings, offering non-toxic solutions that help reduce fuel consumption.
Return on Investment (ROI) Considerations
Investing in advanced hull coatings entails initial costs, but the long-term benefits often outweigh these expenses. Material costs for high-performance coatings typically range from $50 to $80 per square meter, with installation (including surface preparation and application) adding $100 to $150 per square meter.
The fuel savings achieved can be substantial. For example, a capesize bulk carrier consuming 42 tons of low-sulfur fuel oil daily could see annual fuel savings of up to $1.3 million by applying a premium low-friction coating. Considering these savings, the payback period for the investment in such coatings can be as short as three to twelve months, depending on factors like vessel size, operating speed, and fuel costs.
Key Takeaways
The adoption of low-friction and anti-fouling hull coatings is a hot trend in 2025, driven by the dual imperatives of operational efficiency and environmental responsibility. As maritime regulations tighten and the demand for sustainable solutions grows, these advanced coatings are becoming essential for modern fleets aiming to optimize performance and reduce ecological impact.
2️⃣ Air Lubrication Systems 🔥
Enhancing Vessel Efficiency
Air Lubrication Systems (ALS) are innovative technologies designed to reduce the frictional resistance between a ship's hull and seawater by introducing a layer of air bubbles beneath the hull. This reduction in drag leads to significant fuel savings and decreased greenhouse gas emissions. The concept, initially developed in the 1950s by the U.S. Navy for noise reduction, has evolved into a viable energy-saving solution for commercial shipping.
Technological Advancements
Modern ALS utilize microbubble technology, where tiny air bubbles are injected beneath the hull to create a thin air layer. This layer reduces the direct contact between the hull and water, thereby decreasing frictional resistance. Advancements have led to systems that require minimal structural modifications, making them suitable for retrofitting existing vessels.
Leading Industry Players
Several companies are at the forefront of developing and implementing air lubrication technologies:
- Mitsubishi Heavy Industries (MHI): Developed the Mitsubishi Air Lubrication System (MALS), one of the first commercial air lubrication systems, designed to reduce frictional resistance by creating a layer of air bubbles beneath the hull.
- Silverstream Technologies: Offers the Silverstream® System, which uses air lubrication to reduce drag and improve fuel efficiency.
- Wärtsilä: Provides air lubrication solutions that inject air into the turbulent boundary layer between the hull and seawater, effectively reducing frictional resistance.
- Alfa Laval: Introduced the OceanGlide system, a fluidic air lubrication solution that creates an even and controllable air layer across the vessel's flat bottom, reducing friction and improving fuel efficiency.
Return on Investment (ROI)
The installation of an air lubrication system involves significant initial costs, including equipment and installation expenses. However, the fuel savings achieved can offset these costs over time. Reported data indicates that vessels may achieve a net power saving of approximately 4-5% due to the implementation of an air lubrication system. The potential payback period for such an investment varies depending on factors such as vessel type, operating conditions, and fuel prices.
Key Takeaways
Air lubrication systems represent a promising technology for enhancing fuel efficiency and reducing emissions in the maritime industry. While the initial investment is considerable, the potential for fuel savings and environmental benefits makes them a compelling option for modern fleets. As the technology advances and becomes more widely adopted, air lubrication systems are expected to play a significant role in the future of sustainable shipping.
3️⃣ High-Efficiency Propeller Upgrades 🔥
Enhancing Propulsive Performance
High-efficiency propeller upgrades are pivotal in optimizing a vessel's propulsion system, leading to significant improvements in fuel efficiency and reductions in greenhouse gas emissions. By refining propeller design and incorporating advanced technologies, ship operators can achieve better thrust, reduced cavitation, and overall enhanced performance.
Technological Advancements
Modern propeller upgrades focus on several key areas:
- Optimized Blade Design: Utilizing computational fluid dynamics (CFD), manufacturers tailor blade shapes to specific vessel operating profiles, ensuring maximum efficiency. For instance, Wärtsilä's efficiency upgrade involves designing new propeller blades that can improve propulsive efficiency by up to 15%.
- Contra-Rotating Propellers: This system employs two propellers rotating in opposite directions on a single shaft line, effectively recovering rotational energy and enhancing propulsion efficiency.
- Wake-Equalizing Ducts: Devices like the Becker Mewis Duct are installed ahead of the propeller to streamline water flow, reducing turbulence and improving efficiency.
Leading Industry Players
Several companies are at the forefront of propeller innovation:
- Wärtsilä: Offers comprehensive propeller solutions, including the Wärtsilä Efficiency Upgrade, which involves designing optimized propeller blades to enhance performance.
- Kongsberg Maritime: Developed the Promas system, integrating the propeller and rudder into a single unit to optimize hydrodynamic efficiency.
- MAN Energy Solutions: Provides a range of high-efficiency propellers and aft-ship solutions designed to enhance propulsion performance.
- Sharrow Marine: Introduced the Sharrow Propeller™, a patented looped propeller design that offers improved efficiency and reduced noise.
Return on Investment (ROI)
Investing in high-efficiency propeller upgrades entails initial costs, including design, manufacturing, and installation. However, the potential fuel savings and operational benefits often justify the investment. For example, Wärtsilä reports that their optimized propeller designs can lead to propulsive efficiency improvements of up to 15%, with a typical payback period of 2 to 3 years.
Key Takeaways
Upgrading to high-efficiency propellers is a "hot" trend in 2025, driven by the maritime industry's focus on sustainability and cost-effectiveness. Advanced propeller designs and technologies not only enhance fuel efficiency but also contribute to reduced emissions, aligning with global environmental regulations. As the industry continues to innovate, adopting these propeller upgrades becomes increasingly advantageous for modern fleets aiming to optimize performance and operational costs.
4️⃣ Energy-Saving Devices (ESDs) 🔥
Enhancing Propulsion Efficiency
Energy-Saving Devices (ESDs) are innovative technologies designed to improve a ship's propulsion efficiency by reducing hydrodynamic resistance and optimizing water flow around the hull and propeller. By enhancing the interaction between the vessel and water, ESDs contribute to significant fuel savings and reduced greenhouse gas emissions, aligning with the maritime industry's sustainability goals.
Technological Advancements
Several ESDs have been developed to address different aspects of propulsion efficiency:
- Pre-Swirl Devices: These are installed ahead of the propeller to condition the inflow of water, reducing rotational losses and improving thrust. The Becker Mewis Duct®, for example, is a pre-swirl stator that creates a pre-swirl in the inflow, leading to fuel savings of up to 10% for tankers and bulk carriers.
- Post-Swirl Devices: Located aft of the propeller, these devices recover rotational energy from the propeller slipstream. The Propeller Boss Cap Fin (PBCF) is one such device that reduces the hub vortex, enhancing propeller efficiency and achieving fuel savings of approximately 4-5%.
- Hull Modifications: Adjustments to the hull form, such as the installation of the Silent Bulb by Damen Marine Components, streamline water flow and minimize turbulence, contributing to overall energy efficiency.
Leading Industry Players
Several companies are at the forefront of developing and implementing ESDs:
- Becker Marine Systems: Offers the Becker Mewis Duct® and Becker Twisted Fin®, both designed to enhance propulsion efficiency and reduce emissions.
- Wärtsilä: Provides a range of energy-saving technologies, including the GATE RUDDER™, an innovative device that improves maneuverability and reduces fuel consumption.
- Damen Marine Components: Develops products like the Silent Bulb, which reduces propeller flow losses and enhances efficiency.
- VICUSdt: Specializes in designing customized ESDs tailored to specific vessel requirements, optimizing propulsion performance.
Return on Investment (ROI)
The initial investment in ESDs varies depending on the type of device and the complexity of installation. However, the fuel savings achieved can lead to a favorable payback period. For instance, installing a Becker Mewis Duct® can result in fuel consumption reductions of up to 10%, with a typical ROI period ranging from one to two years, depending on the vessel's operational profile and fuel costs.
Key Takeaways
In 2025, the adoption of Energy-Saving Devices is a prominent trend in the maritime industry, driven by the dual imperatives of cost efficiency and environmental responsibility. ESDs offer shipowners practical solutions to enhance propulsion efficiency, reduce fuel consumption, and comply with increasingly stringent emission regulations. As technology advances and more vessels undergo retrofitting, ESDs are poised to become standard components in modern ship design and operation.
5️⃣ Rudder Optimization 🔥
Enhancing Maneuverability and Fuel Efficiency
Rudder optimization plays a crucial role in improving a vessel's maneuverability and fuel efficiency. By refining rudder design and integrating advanced technologies, ships can achieve better course stability, reduced hydrodynamic resistance, and lower fuel consumption.
Technological Advancements
Recent innovations in rudder technology focus on optimizing the interaction between the propeller and rudder to enhance propulsion efficiency:
- Integrated Propeller-Rudder Systems: Collaborations between propulsion and rudder specialists have led to designs like the Energopac, which integrates the propeller and rudder to optimize water flow, resulting in improved efficiency and maneuverability.
- CFD-Optimized Rudders: Utilizing Computational Fluid Dynamics (CFD), designers can create rudder profiles tailored to specific vessel characteristics, reducing resistance and enhancing performance.
- Advanced Rudder Profiles: Innovations such as twisted leading-edge rudders and rudders with propulsion bulbs are designed to minimize cavitation and improve thrust efficiency.
Leading Industry Players
Several companies are at the forefront of rudder optimization:
- Becker Marine Systems: Renowned for their innovative rudder solutions, including the Becker Flap Rudder and Becker Twist Rudder, which enhance propulsion efficiency and maneuverability.
- Damen Marine Components: Offers a range of rudders and steering systems designed to improve vessel performance across various maritime sectors.
- Wärtsilä: Provides integrated propulsion and rudder solutions, such as the EnergoPac, aimed at optimizing propulsion and improving vessel maneuverability.
Return on Investment (ROI)
Investing in rudder optimization can lead to significant fuel savings. Studies indicate that optimizing rudder configuration can achieve fuel savings ranging from 2% to 8%, depending on the vessel type and operational profile.
The payback period for such investments varies but is often within a few years, making it a cost-effective strategy for enhancing vessel performance.
Key Takeaways
In 2025, rudder optimization stands out as a "hot" strategy for shipowners aiming to boost fuel efficiency and reduce operational costs. Advanced rudder designs and integrated propulsion systems not only enhance maneuverability but also contribute to significant fuel savings, aligning with the maritime industry's sustainability goals. As technology continues to advance, investing in rudder optimization offers a compelling return on investment for modern fleets.
🌡️ WARM (Growing Interest, but Not Yet Industry Standard)
6️⃣ Bulbous Bow Retrofits 🌡️
Enhancing Fuel Efficiency Through Bow Optimization
Bulbous bows are protruding bulb-like structures at a ship's bow, positioned just below the waterline. They modify the flow of water around the hull, reducing wave resistance and enhancing fuel efficiency. Retrofitting an existing vessel with a redesigned bulbous bow can lead to significant performance improvements, especially when operational profiles have changed since the ship's original design.
Technological Advancements
Modern computational fluid dynamics (CFD) simulations enable precise optimization of bulbous bow designs tailored to a vessel's current operating conditions. For instance, a study on a container vessel demonstrated that optimizing the bulbous bow for actual operational profiles resulted in a fuel consumption reduction of over 14%, primarily by decreasing resistance at lower speeds.
Similarly, FORCE Technology conducted retrofitting studies where new bulbous bows were designed based on ships' operational profiles, achieving resistance savings of up to 17.5%.
Leading Industry Players
Several companies specialize in bulbous bow retrofitting:
- FORCE Technology: Offers comprehensive studies and design services for optimizing bulbous bows based on a ship's operational profile, leading to significant fuel savings.
- Foreship: Provides feasibility studies and retrofit designs for bulbous bows, utilizing modern CFD simulations to achieve fuel savings of up to 13%.
- DNV: Utilizes a formal optimization approach featuring fully parametric models for bulbous bow design, aiming to enhance vessel efficiency through tailored retrofitting solutions.
- VICUSdt: Specializes in multi-objective bulbous bow optimization using CFD, achieving energy savings above 10% compared to original configurations.
Return on Investment (ROI)
The cost of retrofitting a bulbous bow varies depending on vessel size and complexity. Estimates suggest that the fixed cost for a new bulbous bow, including optimization, engineering, and approval, is approximately $100,000, with additional material costs ranging from $250,000 to $700,000.
Fuel savings from such retrofits can be substantial. For example, a study reported that redesigning a container ship's bulbous bow for slow steaming resulted in annual fuel savings of about 5%, allowing the retrofit to pay for itself in less than a year.
Key Takeaways
In 2025, bulbous bow retrofits are considered a "warm" strategy for enhancing vessel efficiency. While not universally applicable, they offer significant benefits for ships operating under conditions different from their original design specifications. Advancements in CFD and design optimization have made it feasible to tailor bulbous bows to current operational needs, leading to notable fuel savings and reduced emissions. Shipowners should assess their vessels' operational profiles to determine the potential ROI of such retrofits.
7️⃣ Hull Form Optimization 🌡️
Enhancing Hydrodynamic Performance
Hull form optimization involves refining a vessel's shape to minimize resistance and improve hydrodynamic efficiency. By analyzing and adjusting the hull's geometry, ship designers can reduce fuel consumption, enhance speed, and improve overall performance. This process is crucial for both new builds and retrofitting existing vessels to meet modern efficiency standards.
Technological Advancements
Advancements in computational tools have significantly impacted hull form optimization:
- Computational Fluid Dynamics (CFD): Utilizing CFD simulations allows for detailed analysis of fluid flow around the hull, enabling designers to identify and mitigate areas of high resistance. This approach facilitates the evaluation of multiple design iterations efficiently.
- Parametric Design Modifications: Techniques such as adjusting the prismatic coefficient, waterline length, and bulbous bow geometry enable targeted refinements to the hull form, leading to reductions in wave-making resistance and improved seakeeping.
- Surrogate Modeling and Machine Learning: Incorporating deep learning models and surrogate-based optimization accelerates the design process by predicting hydrodynamic performance outcomes, allowing for rapid exploration of design spaces.
Leading Industry Players
Several companies are at the forefront of hull form optimization:
- FRIENDSHIP SYSTEMS AG: Developers of CAESES®, a software solution enabling naval architects to create parametric ship models for CFD-based hull optimization. Their expertise includes modeling hull forms, appendages, propellers, and energy-saving devices.
- VARD: A ship design company specializing in custom vessel designs. Their hydrodynamics team utilizes advanced tools and computational resources to develop optimized hull forms, achieving up to 30% less resistance compared to designs from a decade ago.
- Cloud Towing Tank: Offers CFD-based hull form optimization services, automating simulations to minimize resistance and propulsion power. They employ parametric modeling to explore various hull geometries, enhancing performance and efficiency.
- FORCE Technology: Provides hull line optimization services using CFD tools like StarCCM+. Their approach includes both manual iterative optimization and parametric optimization utilizing CAESES®, aiming to reduce resistance and improve inflow conditions to the propeller.
- Ulstein Design & Solutions AS: Part of the Ulstein Group, this company develops ship designs incorporating innovative hull concepts such as the X-BOW® and X-STERN®, which enhance seakeeping and reduce fuel consumption.
Return on Investment (ROI)
Investing in hull form optimization can yield substantial fuel savings. The cost of a comprehensive CFD analysis varies depending on the project's complexity and the tools used. Optimized hull designs can achieve fuel consumption reductions between 4% and 8%, leading to a favorable payback period. The initial investment in optimization services is often offset by the long-term savings in operational costs.
Key Takeaways
In 2025, hull form optimization remains a "warm" strategy for enhancing vessel efficiency. The integration of advanced computational methods and design techniques enables shipowners to achieve significant performance improvements. As environmental regulations tighten and fuel costs rise, optimizing hull forms offers a practical approach to meeting these challenges while ensuring operational profitability.
8️⃣ Next-Gen Bow Shapes 🌡️
Revolutionizing Maritime Design
In the quest for enhanced maritime efficiency and performance, next-generation bow shapes have emerged as pivotal innovations. These advanced designs, including wave-piercing bows and inverted bows like the Ulstein X-BOW®, are redefining how vessels navigate diverse sea conditions.
Technological Advancements
- Wave-Piercing Bows: Characterized by a slender, fine-pointed bow, wave-piercing designs allow ships to cut through waves rather than riding over them. This approach reduces vertical motion and slamming, leading to a smoother ride and improved fuel efficiency.
- Inverted Bows (Ulstein X-BOW®): The Ulstein X-BOW® features a backward-sloping, inverted bow design that enhances hydrodynamic efficiency. By distributing wave impact forces more evenly, it reduces pitch motion and fuel consumption, offering a more stable and comfortable voyage.
Leading Industry Players
- Ulstein Group: Pioneers of the X-BOW® design, Ulstein has integrated this innovative bow shape into over 100 vessels worldwide, spanning offshore support ships to expedition cruise liners.
- Baltic Workboats: Specializing in wave-piercing designs, Baltic Workboats offers vessels with bows that enhance fuel efficiency and seakeeping abilities, particularly beneficial for pilot boats and patrol crafts.
Return on Investment (ROI)
Adopting next-gen bow designs involves initial investment in advanced engineering and construction. However, the long-term benefits include significant fuel savings and reduced maintenance costs due to decreased structural stress. For instance, vessels equipped with the X-BOW® have reported smoother transits and lower operational expenses, leading to a favorable ROI over time.
Key Takeaways
In 2025, next-generation bow shapes represent a "warm" trend in maritime innovation. While not yet universally adopted, their proven advantages in fuel efficiency, vessel stability, and passenger comfort position them as compelling options for new builds and retrofits. As the industry continues to prioritize sustainability and performance, these advanced bow designs are poised to become more prevalent in modern fleets.
9️⃣ Wind-Assisted Propulsion 🌡️
Harnessing Wind Power for Sustainable Shipping
Wind-assisted propulsion is experiencing a resurgence in the maritime industry as shipowners seek sustainable solutions to reduce fuel consumption and greenhouse gas emissions. By integrating modern wind propulsion technologies, vessels can harness renewable wind energy, leading to significant operational cost savings and environmental benefits.
Leading Industry Players
- WindWings: Developed by BAR Technologies and first implemented by Cargill, WindWings are large, solid sails retrofitted onto cargo vessels. In 2024, the Pyxis Ocean, equipped with two WindWings, reported a 14% reduction in fuel consumption during a six-month trial.
- Norsepower: Specializes in modern Flettner rotors—vertically mounted, spinning cylinders that utilize the Magnus effect to generate thrust. Their rotor sails have been installed on various vessels, including tankers and ferries, achieving fuel savings of up to 20%.
- bound4blue: Offers the eSAIL® system, an automated rigid sail solution. Recent agreements with companies like Eastern Pacific Shipping and Louis Dreyfus Company aim to install these systems, with expected fuel savings between 10-15% and a potential payback period of less than five years.
- Mitsui O.S.K. Lines (MOL): Developed the Wind Challenger project, featuring a hard sail system designed to harness wind energy for propulsion. The first installation was completed in February 2022, marking a significant step toward integrating wind-assisted technologies in large commercial vessels.
- Airseas: A subsidiary of Airbus, Airseas has developed the Seawing, a large, automated kite system designed to tow ships and reduce fuel consumption. The system can be retrofitted to existing vessels and is expected to deliver fuel savings of around 20%.
Return on Investment (ROI)
The initial investment for wind-assisted propulsion systems varies based on the technology and vessel type. However, with fuel savings ranging from 5% to 20%, shipowners can anticipate a return on investment within three to five years. Factors influencing ROI include installation costs, fuel prices, and operational profiles. As fuel costs rise and environmental regulations tighten, the economic viability of these systems becomes increasingly attractive.
Key Takeaways
In 2025, wind-assisted propulsion stands out as a "hot" trend in maritime innovation. Advancements in technology and successful trials have demonstrated the practicality and benefits of harnessing wind energy for commercial shipping. As the industry moves toward decarbonization, integrating wind-assisted propulsion systems offers a viable pathway to achieving sustainability goals while enhancing economic performance.
1️⃣0️⃣ Trim Optimization Systems 🌡️
Enhancing Fuel Efficiency Through Optimal Vessel Trim
Trim optimization systems are advanced technologies designed to enhance a vessel's fuel efficiency by determining and maintaining the optimal trim—the longitudinal balance of the ship—during various operating conditions. By adjusting the distribution of cargo, ballast, and fuel, these systems minimize hydrodynamic resistance, leading to significant fuel savings and reduced greenhouse gas emissions.
Technological Advancements
Modern trim optimization leverages computational tools and real-time data analysis:
- Computational Fluid Dynamics (CFD): Utilizing CFD simulations, ship designers can predict the hydrodynamic performance of different trim settings without physical model testing. This approach allows for the creation of trim optimization matrices that inform optimal loading and ballast configurations.
- Artificial Neural Networks (ANN): Integrating ANN models with CFD data enables the development of user-friendly software tools that provide real-time trim optimization guidance, facilitating quick decision-making for fuel-efficient operations.
Leading Industry Players
Several companies specialize in providing trim optimization solutions:
- DNV: Offers the ECO Assistant, an onboard software tool that provides ship-specific trim optimization guidance, enabling fuel savings across various operating conditions.
- Herbert-ABS Software Solutions: Developed the CargoMax Trim Optimization Tool, which combines regulatory compliance with optimization algorithms to deliver efficient and achievable loading conditions that minimize fuel consumption.
- FORCE Technology: Utilizes CFD-based trim optimization services, providing ship-specific guidance to achieve fuel savings without requiring physical modifications to the hull or propulsion systems.
Return on Investment (ROI)
Implementing trim optimization systems involves initial costs, including software installation and crew training. However, the potential fuel savings are substantial. Studies indicate that optimizing trim can reduce fuel consumption by up to 5%, depending on the vessel type and operational profile. For a container feeder vessel of about 2,000 TEU sailing at 22 knots, this translates to savings of approximately 35 barrels of oil per day.
The potential payback period for such investments is typically between one to six months, making it a cost-effective strategy for enhancing operational efficiency.
Key Takeaways
In 2025, trim optimization systems are a "hot" trend in the maritime industry, driven by the dual imperatives of cost reduction and environmental sustainability. By leveraging advanced computational tools and real-time data analysis, these systems enable ship operators to achieve optimal vessel performance with minimal investment. As fuel prices rise and emission regulations become more stringent, adopting trim optimization solutions offers a practical pathway to improved efficiency and compliance.
1️⃣1️⃣ Wake Reduction Technologies 🌡️
Enhancing Maritime Efficiency and Environmental Stewardship
Wake reduction technologies are innovative solutions designed to minimize the waves generated by vessels as they move through water. Excessive wake can lead to increased fuel consumption, shoreline erosion, and disturbances to marine ecosystems. Implementing wake reduction strategies not only enhances a vessel's operational efficiency but also mitigates its environmental impact.
Technological Advancements
Several approaches have been developed to address wake generation:
- Hull Design Optimization: Streamlined hull shapes reduce water displacement and wave formation. Advanced computational fluid dynamics (CFD) simulations allow designers to create hulls that minimize wake while maintaining performance. For instance, the Lürssen effect involves the use of additional rudders to direct water flow, lifting the stern and reducing wake height.
- Wake-Adapted Propulsion Systems: Customizing propellers, struts, and rudders to align with the vessel's wake field enhances propulsion efficiency and reduces wave generation. Michigan Wheel offers wake-adapted equipment that improves speed, fuel efficiency, and lowers noise and vibration by optimizing the interaction with the vessel's wake.
- Hydrofoil Technology: Elevating the hull above water using hydrofoils decreases contact with the water surface, significantly reducing wake. Artemis Technologies' eFoiler® system exemplifies this approach, enabling vessels to "fly" above the water, thus minimizing wave creation and allowing high-speed operations with minimal environmental disruption.
Leading Industry Players
- Artemis Technologies: Specializes in hydrofoil-based propulsion systems that lift vessels above the waterline, reducing drag and wake. Their eFoiler® technology is a testament to innovative design focused on efficiency and environmental responsibility.
- Michigan Wheel: Provides wake-adapted propulsion solutions, including custom-designed propellers and rudders that enhance vessel performance and reduce wake-induced impacts.
- Lürssen Werft: A German shipbuilding company recognized for developing the Lürssen effect, a technique that employs additional rudders to diminish wake height and improve vessel speed.
Return on Investment (ROI)
Investing in wake reduction technologies can yield substantial benefits. While the initial costs vary depending on the chosen solution—ranging from hull modifications to advanced propulsion systems—the long-term advantages include fuel savings, extended vessel lifespan due to reduced structural stress, and compliance with environmental regulations. For example, implementing wake-adapted equipment has demonstrated improvements in speed and fuel efficiency, leading to cost savings over time.
Key Takeaways
In 2025, wake reduction technologies are gaining traction as a "warm" trend in the maritime industry. As environmental concerns and regulatory pressures intensify, adopting solutions that mitigate wake generation aligns with sustainable practices and operational efficiency. By integrating advanced hull designs, propulsion adaptations, and hydrofoil systems, shipowners can enhance performance while minimizing ecological footprints.
🍵 LUKEWARM (Limited Adoption, Experimental or Niche Applications)
1️⃣2️⃣ Bow Shields
Enhancing Aerodynamic Efficiency in Container Ships
Bow shields, also known as wind deflectors, are aerodynamic structures installed on the bow of ships to reduce air resistance. By streamlining airflow around the vessel's superstructure and deck cargo, these devices decrease aerodynamic drag, leading to improved fuel efficiency and reduced greenhouse gas emissions.
Technological Advancements
The design of bow shields focuses on optimizing their shape and placement to maximize aerodynamic benefits:
- Aerodynamic Design: Utilizing computational fluid dynamics (CFD), engineers create smooth, rounded structures that effectively divert airflow, minimizing turbulence and drag. For instance, a study on a 12,000 TEU container ship demonstrated that an optimized bow windshield could significantly reduce wind resistance, contributing to fuel savings.
- Material Selection: Bow shields are constructed from lightweight, durable materials to withstand harsh marine environments without adding significant weight to the vessel.
Return on Investment (ROI)
The initial investment in bow shields includes design, fabrication, and installation costs. However, the fuel savings achieved can offset these expenses over time. With reported reductions in CO₂ emissions of around 2%, the potential payback period varies depending on factors such as fuel prices, voyage frequency, and vessel size. As environmental regulations become more stringent, the adoption of bow shields offers both economic and compliance benefits.
Key Takeaways
In 2025, the implementation of bow shields is considered a "warm" trend in the maritime industry. While primarily utilized on container ships, their proven benefits in reducing aerodynamic drag and enhancing fuel efficiency make them a viable consideration for other vessel types. As the industry continues to prioritize sustainability and operational efficiency, bow shields represent a practical solution to meet these objectives.
❄️ COLD (Low Demand, Niche, or Unproven for Large Ships)
1️⃣3️⃣ Fixed Air Pockets in Hull Design ❄️
Concept and Intended Benefits
Fixed air pockets in hull design involve incorporating cavities or air pockets within the hull structure to passively reduce drag by creating an air layer between the ship and the water. The idea is similar to air lubrication systems but without active air injection, relying instead on hull geometry and structural design to trap air naturally.
Why It’s Considered "Cold"
- Limited Practicality: Unlike active air lubrication systems, passive air pockets are difficult to maintain and can become ineffective in rough seas or varying load conditions.
- Structural Challenges: Implementing fixed air pockets requires major design modifications, making it impractical for retrofits and costly for new builds.
- Marginal Efficiency Gains: Research has shown that while air layers can reduce drag, the gains are often inconsistent and difficult to optimize across different ship speeds and sea states.
Key Takeaways
While the concept of fixed air pockets for passive drag reduction is theoretically sound, its technical limitations and lack of real-world adoption make it a cold strategy for 2025. The maritime industry continues to focus on active air lubrication and hull coatings, which provide more reliable efficiency improvements.
1️⃣4️⃣ Adaptive Bow Structures ❄️
Concept and Intended Benefits
Adaptive bow structures, or flexible bow concepts, refer to hull designs where the bow shape can dynamically adjust based on sea conditions. This could involve mechanical adjustments, hydraulics, or flexible materials that change shape to optimize hydrodynamics for different speeds and wave conditions.
Why It’s Considered "Cold"
- High Complexity: A flexing or adjustable bow would require highly complex engineering, making it expensive and difficult to implement at scale.
- Durability Concerns: Ships endure extreme stress, and moving parts in the bow could be vulnerable to damage in rough seas.
- No Proven Fuel Savings: While the idea sounds promising, there’s no commercial implementation demonstrating significant fuel savings, unlike proven hull optimization techniques.
Key Takeaways
The idea of an adaptive bow structure remains more of an experimental concept rather than a viable solution for commercial shipping. Rigid hull optimizations and air lubrication systems provide simpler and more effective ways to reduce drag and improve efficiency.
1️⃣5️⃣ Retractable Hull Extensions ❄️
Concept and Intended Benefits
Retractable hull extensions refer to deployable sections of the hull that extend outward when needed to improve stability, hydrodynamics, or fuel efficiency. The concept is similar to foldable outriggers on racing yachts, aiming to optimize performance for different speeds and loading conditions.
Why It’s Considered "Cold"
- Engineering Complexity: A moving hull section adds mechanical failure risks and would require significant reinforcement to handle ocean forces.
- Limited Benefits for Large Ships: Unlike small racing vessels where aerodynamics and agility are key, large commercial ships rely more on hull shape and weight distribution than deployable structures for efficiency.
- High Maintenance and Regulatory Hurdles: Any movable hull components would require additional maintenance, classification society approval, and operational oversight, making them less attractive compared to passive efficiency solutions.
Key Takeaways
While retractable hull extensions may have niche applications in small vessels or specialized designs, they lack practicality for large commercial ships. Fixed hull optimization methods, such as hull coatings, air lubrication, and bow modifications, remain the preferred strategies in 2025.
Table Summary
ShipUniverse: Hull Optimization Strategies in 2025 | |||
Strategy | 🔥 | What You Need to Know | Potential Fuel Savings & Costs |
Low-Friction & Anti-Fouling Hull Coatings | 🔥 | Special coatings smooth the hull and prevent marine growth, reducing drag and improving efficiency. The latest biocide-free options last longer and require less maintenance than traditional coatings. |
Fuel savings: 5-10% Coating cost: $50-$80 per square meter Application cost: $100-$150 per square meter Potential payback period: 3-12 months |
Air Lubrication Systems | 🔥 | These systems pump a layer of air bubbles under the hull to reduce friction. Best suited for large vessels operating long distances, they require specialized installation. |
Fuel savings: 5-10% Installation cost: $500,000 - $1M Potential payback period: 2-4 years Best for: Large bulk carriers, tankers, and cruise ships |
High-Efficiency Propeller Upgrades | 🔥 | Upgrading to modern propellers with optimized blade designs can significantly improve propulsion efficiency. Options like wake-adapted blades and contra-rotating propellers are becoming more common. |
Fuel savings: Up to 15% Upgrade cost: $250,000 - $750,000 Potential payback period: 2-5 years Best for: Cargo ships, container ships, bulk carriers |
Energy-Saving Devices (ESDs) | 🔥 | These include pre-swirl stators, ducts, and propeller boss cap fins that optimize water flow, reduce turbulence, and increase fuel efficiency. |
Fuel savings: 4-10% Installation cost: $100,000 - $400,000 Potential payback period: 1-3 years Best for: Tankers, bulk carriers, container ships |
Rudder Optimization | 🔥 | Optimized rudder designs improve water flow around the propeller, reducing drag and enhancing propulsion efficiency. Technologies like twisted rudders and propulsion bulbs are gaining traction. |
Fuel savings: 2-8% Installation cost: $200,000 - $600,000 Potential payback period: 2-6 years Best for: Cargo ships, tankers, large vessels |
Bulbous Bow Retrofits | 🌡️ | A redesigned bulbous bow can significantly reduce wave resistance, improving fuel efficiency. Retrofits are most effective for ships that now operate at different speeds than originally designed. |
Fuel savings: 4-8% Retrofit cost: $250,000 - $700,000 Potential payback period: 1-3 years Best for: Container ships, bulk carriers, tankers |
Hull Form Optimization | 🌡️ | Refining the shape of the hull reduces drag and increases efficiency. Advanced computational fluid dynamics (CFD) simulations now allow precise hull modifications for better performance. |
Fuel savings: 4-8% Modification cost: $150,000 - $500,000 Potential payback period: 1-4 years Best for: New builds, ships undergoing major dry-docking |
Next-Gen Bow Shapes | 🌡️ | Innovative designs like the Ulstein X-BOW® reduce wave impact, improving fuel efficiency and vessel stability. These are becoming increasingly popular in offshore and expedition vessels. |
Fuel savings: 3-7% Cost: Part of vessel design, not easily retrofittable Best for: Offshore vessels, cruise ships, high-speed craft |
Wind-Assisted Propulsion | 🌡️ | Technologies like WindWings, rotor sails, and kite propulsion reduce fuel use by harnessing wind power. Adoption is rising due to stricter emissions regulations. |
Fuel savings: 5-20% Installation cost: $500,000 - $3M Potential payback period: 3-7 years Best for: Large bulk carriers, tankers, container ships |
Trim Optimization Systems | 🌡️ | Real-time software analyzes and adjusts a ship's trim to optimize hydrodynamic efficiency, reducing fuel consumption without requiring structural modifications. |
Fuel savings: 2-5% System cost: $50,000 - $250,000 Potential payback period: 6 months - 2 years Best for: Most large commercial vessels |
Wake Reduction Technologies | 🌡️ | These systems modify water flow behind a vessel to minimize wake, reducing drag and improving efficiency. Technologies include optimized stern designs and wake-adapted propulsion. |
Fuel savings: 2-6% Modification cost: $100,000 - $500,000 Potential payback period: 1-4 years Best for: Passenger ships, ferries, research vessels |
Bow Shields | 🍵 | Aerodynamic wind deflectors installed on the bow of container ships to reduce wind resistance, improving fuel efficiency and stability in high-wind conditions. |
Fuel savings: Up to 2% Installation cost: $50,000 - $250,000 Potential payback period: 1-3 years Best for: Container ships, car carriers |
Fixed Air Pockets in Hull Design | ❄️ | A passive drag reduction concept where air pockets in the hull create an air layer to reduce water friction. While promising in theory, real-world results have been inconsistent. |
Fuel savings: Uncertain Implementation cost: High due to hull modifications Best for: Experimental ship designs, concept testing |
Adaptive Bow Structures | ❄️ | Theoretical designs where the bow shape can dynamically adjust based on sea conditions to optimize hydrodynamics. No commercial applications currently exist. |
Fuel savings: Unknown Cost: Not commercially available Best for: Experimental research, future shipbuilding concepts |
Retractable Hull Extensions | ❄️ | Deployable hull sections that extend when needed to improve hydrodynamics. The mechanical complexity and maintenance challenges make this impractical for large commercial ships. |
Fuel savings: Theoretical Implementation cost: Likely high due to structural modifications Best for: Small vessels, military applications, concept ships |
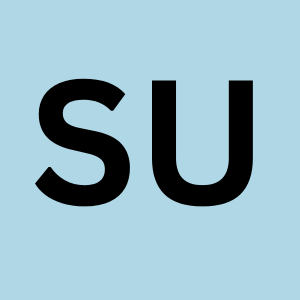
Do you have a Maritime Product or Service that may be of interest to Shipowners? Tell us about it here!
Do you have feedback or insights? Please reach out to editor @ shipuniverse.com