Port Strikes Ahead: A Ship Owner’s Survival Guide
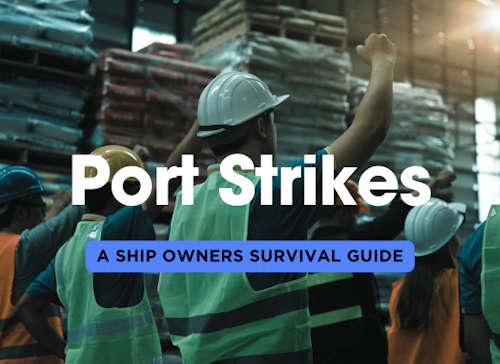
In the world of maritime shipping, strikes at key ports can be one of the most disruptive events for ship and fleet owners. Whether it’s dockworkers halting operations or logistical blockades forming, strikes can lead to delays, unexpected costs, and major disruptions to global supply chains. Today we will walk through practical strategies to mitigate these risks and keep your operations running smoothly during port labor disputes, wherever they might occur.
Understanding Supply Chain Impact
Developing Contingency Plans
Legal Considerations and Government Intervention
Communication with Stakeholders
Cost Management During Strikes
Monitoring the Situation
Understanding Broader Economic Effects
Understanding Supply Chain Impact
When strikes occur, the most immediate effect is on the supply chain. Ship and fleet owners should expect delays in the loading and unloading of cargo, increased costs due to supply chain rerouting, and potential shortages of goods, especially in time-sensitive industries like retail and agriculture. The domino effect often extends beyond the ports, affecting trucking, rail, and warehousing operations. Understanding the full scope of these impacts is crucial to mitigating the disruptions and keeping your cargo moving as efficiently as possible.
ShipUniverse: Understanding the Impact on Supply Chains | ||
---|---|---|
Aspect | Explanation | Recommended Action |
Delays | Strikes create massive backlogs in ports, with cargo stuck for days or even weeks. This is worsened by the ripple effect throughout the entire transportation network—trucking, rail, and even warehouses become impacted. | Work with logistics providers to pre-arrange alternative routes or ports. Keep in constant communication with partners to adjust schedules in real time. |
Cost Increases | Rerouting ships or using alternative transportation methods like air freight adds significant costs. Additionally, port fees, demurrage, and detention charges pile up if ships are held up at congested ports. | Negotiate flexible shipping contracts that include cost caps for delays and demurrage charges. Budget for potential strike-related cost spikes in your operational expenses. |
Perishable Goods Risk | For industries reliant on perishable goods (e.g., agriculture, pharmaceuticals), a strike can result in significant financial losses due to spoilage during transport delays. | Ensure you have refrigerated transport solutions available and explore using nearby ports to minimize the risk of spoilage. |
Global Supply Chain Disruption | Strikes at major U.S. ports can affect global supply chains by causing delays in goods arriving from international markets, which impacts factories and retailers relying on imports for production or sales. | Coordinate with international suppliers to expedite shipments before a strike and consider holding extra inventory where feasible to weather extended delays. |
Capacity Constraints | As ships reroute to other ports, those ports may not have the capacity to handle the influx, leading to additional delays and higher costs due to lack of available berths or equipment. | Pre-book space at alternative ports ahead of time and secure backup arrangements to prevent being left without options. |
Truck & Rail Delays | A strike doesn't just stop at the port—it quickly spreads to the trucking and rail networks. With fewer trucks available or increased demand for rail, prices soar and delivery timelines lengthen. | Develop partnerships with reliable trucking and rail companies that prioritize your cargo during disruptions, and try to lock in rates ahead of time. |
Increased Warehousing Costs | Warehouses near affected ports become overloaded, pushing businesses to use more expensive, distant facilities or rent temporary storage, increasing overall logistics costs. | Consider temporary warehousing contracts in advance or partner with third-party logistics companies (3PL) that offer scalable warehousing solutions. |
Customer Satisfaction | Prolonged delays can lead to unfulfilled customer orders, which in turn can damage long-term business relationships, especially during critical periods like the holiday season. | Communicate openly with your customers about possible delays. Offer discounts or incentives to mitigate dissatisfaction, and keep them informed with real-time updates. |
Contractual Penalties | Businesses bound by contracts that guarantee delivery timelines can face penalties or even breach of contract lawsuits if they fail to deliver on time during a strike. | Negotiate force majeure clauses into contracts, allowing for flexibility in cases of uncontrollable disruptions like port strikes. |
Long-Term Strategic Adjustments | A single strike might be temporary, but it often forces businesses to rethink their long-term supply chain strategies to build in greater resilience against future labor disruptions. | Consider diversifying suppliers, working with multiple ports, or increasing reliance on automation and technology to reduce human labor risks in critical supply chain areas. |
Developing Contingency Plans
When facing a potential or ongoing strike, it’s essential to have a robust contingency plan in place. This means diversifying your port options, rerouting cargo through unaffected regions, and ensuring flexibility in your shipping schedules. Ship and fleet owners can minimize risks by establishing relationships with logistics providers and alternative ports, allowing them to pivot quickly when disruptions occur. Working proactively with these partners to adjust schedules, secure space at other ports, and anticipate delays will help mitigate the impact of strikes on operations.
ShipUniverse: Developing Contingency Plans for Port Strikes | ||
---|---|---|
Strategy | Explanation | Recommended Action |
Diversify Port Options | Relying on a single port, especially one vulnerable to strikes, puts your operations at significant risk. Utilizing multiple ports—both domestically and internationally—can reduce this risk. | Identify alternative ports on the West Coast, Gulf Coast, or in nearby countries and establish contracts or agreements to quickly shift operations when needed. |
Reroute Cargo Early | Waiting for a strike to start before rerouting cargo can lead to delays and higher costs due to congestion at other ports. Proactive rerouting allows for smoother operations. | Work with your logistics team to reroute shipments early, especially when strike risks are high. Be prepared to pay slightly higher costs for preemptive actions, which may ultimately save time and money. |
Use Multiple Carriers | Relying on a single carrier can bottleneck operations if they are heavily impacted by a strike. Spread your shipments across several carriers to ensure flexibility. | Establish relationships with multiple carriers in advance, and ensure they have the capacity to pick up extra shipments during times of disruption. |
Collaborate with 3PL Providers | Third-Party Logistics (3PL) providers often have access to broader networks and alternative transport options, which can be vital during a strike. | Partner with a reliable 3PL that can provide flexible and scalable solutions for storage, transport, and rerouting during times of port strikes. |
Pre-book Alternative Storage | If shipments are delayed, you may need extra warehousing space. Pre-booking storage options at locations near alternative ports can help avoid last-minute congestion and costs. | Scout warehousing locations near alternative ports and pre-book storage in advance during periods of potential labor unrest. |
Adjust Shipping Schedules | Timing is crucial in avoiding the worst impacts of strikes. Flexible shipping schedules allow for adjusting routes or port destinations when disruptions occur. | Coordinate with your logistics team to build flexibility into your shipping schedules. This might involve staggered shipments or adjusting shipment windows to avoid peak strike periods. |
Monitor Strike Developments | Staying informed about labor negotiations and strike developments allows you to take action before a strike occurs, minimizing disruption. | Subscribe to industry news and labor updates. Establish contacts with port authorities to receive real-time information on potential strikes. |
Build Long-Term Relationships with Ports | Building strong relationships with port operators can offer advantages, such as priority treatment during disruptions and quicker solutions when strikes arise. | Foster good relationships with the ports you regularly use, so they will work with you in times of disruption. This can involve exclusive agreements or priority handling. |
Legal Considerations and Government Intervention
In times of labor unrest, it’s critical for ship and fleet owners to understand the legal frameworks governing strikes and the role government might play. The possibility of government intervention, such as invoking the Taft-Hartley Act, can temporarily suspend a strike but does not guarantee a quick resolution. Being aware of the legal mechanisms in place and planning accordingly will help you navigate potential disruptions while minimizing operational risks. Understanding your contractual rights and force majeure clauses is also essential for avoiding legal and financial penalties.
ShipUniverse: Legal Considerations and Government Intervention | ||
---|---|---|
Consideration | Explanation | Recommended Action |
Taft-Hartley Act | The Taft-Hartley Act allows the U.S. President to intervene in strikes that may threaten national health or safety. This act can temporarily suspend a strike with an 80-day cooling-off period, giving time for further negotiations. | Monitor government announcements closely if a strike occurs. While the Act can offer temporary relief, plan for extended negotiations and delays. |
Force Majeure Clauses | Force majeure clauses in contracts can protect you from penalties related to unforeseen events like strikes, by excusing performance when the situation is beyond your control. | Ensure your contracts include robust force majeure clauses that specifically mention strikes as a valid cause for delays or non-performance. |
Government Mediation | In some cases, the government may act as a mediator between unions and employers to resolve disputes without invoking formal interventions like the Taft-Hartley Act. | Stay informed about labor negotiations and government involvement. Establish connections with legal experts to guide you through any evolving situations. |
Labor Relations Laws | Labor relations laws differ from one region to another. Understanding the legal framework of each region where your fleet operates is crucial for determining what interventions may be allowed. | Consult legal counsel to understand the specific labor laws in the regions you operate in. This will help you anticipate potential legal actions during strikes. |
Contractual Penalties | If you fail to deliver goods or services on time due to strikes, you could face penalties or even breach of contract lawsuits from customers. | Review contracts to ensure that they provide for strike-related delays under force majeure or similar provisions, and be prepared to renegotiate terms if necessary. |
Insurance Coverage | Some business insurance policies offer strike coverage, reimbursing for losses due to labor disruptions. This can protect against financial losses from prolonged strikes. | Review your insurance policies to ensure strike coverage is included, and consider purchasing additional coverage if necessary. |
Industry Advocacy | Industry groups and trade associations may advocate on behalf of businesses affected by port strikes, pressuring governments to intervene or negotiate with unions. | Join industry associations that can advocate for your interests during labor disputes. These groups often have better access to negotiations and legal advice. |
Communication with Stakeholders
In the midst of a strike, communication becomes even more crucial. Keeping your clients, suppliers, and partners informed about delays, disruptions, and alternative plans will help manage expectations and reduce frustrations. Proactive and transparent communication helps maintain trust and strengthens relationships during challenging times. Whether it’s through automated updates, personalized emails, or direct phone calls, ship and fleet owners must ensure that everyone involved is aware of the situation and the steps being taken to minimize the impact.
ShipUniverse: Communication with Stakeholders During a Strike | ||
---|---|---|
Communication Method | Explanation | Recommended Action |
Automated Updates | Set up automated emails or text notifications to provide stakeholders with real-time updates about delays, changes to schedules, or rerouting of shipments. | Work with your IT team to implement an automated notification system that triggers updates when shipments are delayed or rerouted. |
Personalized Communication | For key clients or partners, personalized communication is critical. Direct phone calls or one-on-one emails can provide reassurance and build trust during a disruption. | Assign dedicated team members to handle personalized communication with high-priority clients. Ensure that these updates include specific details about contingency plans and solutions being implemented. |
Regular Status Meetings | Regular status meetings, either in person or via video conferencing, provide stakeholders with a forum to ask questions and stay informed on how the strike is being managed. | Schedule weekly or biweekly status calls with your key stakeholders to provide updates and allow for open communication about any concerns. |
Transparency with Delays | Being transparent about potential or existing delays shows that you’re taking responsibility for the disruption and keeping your partners informed. | Provide regular and honest updates, even if the news isn’t favorable. Let stakeholders know what steps are being taken to mitigate delays. |
Client Education | Explaining the broader impact of the strike helps stakeholders understand why delays are occurring and may help ease frustrations. | Send out educational materials that explain the situation, the expected impact, and the solutions your team is implementing. This could be in the form of newsletters, blog posts, or infographics. |
Internal Team Communication | Keeping your internal teams informed ensures everyone is aligned and able to provide consistent updates to stakeholders. | Hold daily internal briefings to ensure all team members have the latest information on the strike and know what to communicate to external partners. |
Flexibility in Customer Service | During strikes, being flexible with your customer service policies can help maintain relationships and show clients that you’re working hard to meet their needs. | Offer extended customer service hours, additional points of contact, or even temporary policy adjustments like fee waivers for delayed shipments. |
Cost Management During Strikes
Port strikes can lead to substantial cost increases, including higher shipping rates, storage fees, and additional labor expenses. Being proactive about managing these costs is essential to avoid severe financial strain. Ship and fleet owners should focus on strategies like negotiating flexible contracts, utilizing alternative transportation methods, and exploring cost-effective storage solutions. By carefully monitoring expenses and making smart decisions in advance, you can mitigate the financial impact of strikes and protect your bottom line.
ShipUniverse: Cost Management Strategies During Port Strikes | ||
---|---|---|
Strategy | Explanation | Recommended Action |
Negotiate Flexible Shipping Contracts | Pre-negotiated contracts with flexibility for rerouting, delays, or fee adjustments can help manage cost spikes during a strike. | Work with your shipping partners to build flexibility into contracts, allowing for adjustments without severe financial penalties in the event of a strike. |
Utilize Multiple Transport Modes | Shifting from sea to air or land transport, though more expensive upfront, can be a cost-effective solution to avoid prolonged delays and storage costs. | Investigate options for rail or air freight for high-priority shipments, especially when long port delays seem imminent. |
Pre-Book Temporary Storage | During strikes, warehousing near congested ports becomes costly and scarce. Pre-booking temporary storage at alternate locations can help avoid last-minute price hikes. | Secure agreements with storage facilities at alternate ports or in key regions to use if port strikes occur, locking in lower prices ahead of time. |
Leverage Fuel Efficiency | Fuel costs can increase due to rerouting or extended delays at port. Implementing fuel-saving strategies can help offset these increases. | Adopt fuel-saving technologies and practices like optimized routing and slow steaming to reduce consumption and keep fuel costs down. |
Lock in Supplier Prices | Strikes often cause price surges for raw materials and goods. Locking in prices with suppliers through long-term contracts can help avoid unexpected cost spikes. | Negotiate fixed-price contracts with suppliers, especially for critical goods or inputs that may see price increases during shipping disruptions. |
Use Digital Freight Platforms | Digital platforms can offer real-time visibility into freight rates and allow for quick decision-making during price fluctuations caused by strikes. | Leverage digital freight platforms that provide price comparisons and real-time updates on shipping availability and rates to lock in the best deals during strikes. |
Prepare for Demurrage Costs | Ships stuck in congested ports may incur demurrage charges for exceeding allotted time at the terminal. These costs can quickly add up. | Budget for potential demurrage fees and work with port operators to expedite clearance for delayed ships where possible. |
Utilize Short-Term Insurance | Short-term business insurance policies can cover unexpected costs related to strike disruptions, offering financial protection against unexpected charges. | Review your insurance coverage to ensure it includes strike-related disruptions, and consider adding short-term policies during periods of high strike risk. |
Monitoring the Situation
In the midst of a strike, real-time updates and continuous monitoring of the situation are vital for minimizing disruption. Ship and fleet owners need to stay informed about the status of labor negotiations, changes in port operations, and any government interventions. Monitoring should extend beyond just port conditions; it should include tracking global supply chain impacts and keeping an eye on industry news for potential ripple effects. By having up-to-the-minute information, you can make quick decisions and adjust logistics to mitigate delays or reroute shipments.
ShipUniverse: Monitoring the Situation During a Strike | ||
---|---|---|
Monitoring Area | Explanation | Recommended Action |
Port and Labor Negotiation Updates | Staying informed about the status of labor negotiations at key ports helps you anticipate disruptions and make alternative plans early. | Subscribe to industry news outlets, trade union updates, and government announcements to receive real-time information on strikes. |
Government Actions and Policies | Government interventions, such as invoking the Taft-Hartley Act or other emergency measures, can influence how long a strike lasts and its severity. | Monitor government websites and announcements for potential interventions that could temporarily end a strike or ease port congestion. |
Global Supply Chain Ripple Effects | Strikes at major ports can have far-reaching effects, such as delays in cargo deliveries to other regions or shortages of materials worldwide. | Use global logistics platforms to track the ripple effects on international supply chains and identify potential chokepoints outside the immediate strike area. |
Shipping and Freight Rates | Freight rates may fluctuate significantly during strikes due to rerouting and increased demand for limited transport options. | Track real-time freight rates using digital freight platforms, and lock in contracts early if rates begin to rise. |
Port Conditions and Congestion | Strikes can lead to severe congestion at certain ports, causing ships to wait offshore for long periods and incurring demurrage charges. | Use port congestion tracking tools and reports to stay informed about conditions at the affected ports, so you can reroute shipments as necessary. |
Communication with Local Authorities | Local port authorities can provide real-time information on the state of their facilities and any temporary measures being put in place to ease congestion. | Establish direct communication lines with port authorities to get immediate updates on their operations and potential disruptions. |
Technology and Digital Tools | Digital platforms and tools, such as GPS tracking, can help you monitor your shipments in real-time and respond quickly to unexpected delays. | Invest in technology that provides real-time tracking of your fleet and cargo, and ensure you’re using digital solutions to stay ahead of potential disruptions. |
Understanding Broader Economic Effects
Port strikes don’t just impact individual businesses—they can cause widespread economic disruptions that extend beyond shipping. When a major port experiences delays, the ripple effect can affect entire industries, leading to shortages of goods, price hikes, and even slowdowns in manufacturing. Ship and fleet owners should be aware that a prolonged strike can influence not only their supply chain but also the overall market conditions. It’s essential to understand these broader effects to anticipate how a strike may change the economic landscape and to prepare for potential financial or operational impacts in the long term.
ShipUniverse: Understanding the Broader Economic Effects of Port Strikes | ||
---|---|---|
Effect | Explanation | Recommended Action |
Industry-Wide Shortages | Strikes can create bottlenecks that lead to shortages in critical industries like retail, manufacturing, and agriculture. This disrupts production cycles and affects inventory levels globally. | Monitor inventory closely and consider securing additional stock of critical goods in advance of strikes. For manufacturing, explore alternative suppliers outside affected regions. |
Price Increases | Delays and shortages caused by strikes can drive up the cost of goods and services, especially in sectors heavily reliant on timely deliveries, such as retail and construction. | Budget for potential price increases during strikes and communicate with your customers about potential cost adjustments ahead of time to manage expectations. |
Economic Slowdown | Strikes at major ports can ripple into the broader economy, slowing down sectors like manufacturing, retail, and even services that depend on the timely movement of goods. | Diversify your supply chain and secure backup suppliers to avoid dependency on regions affected by strikes. Monitor economic indicators to adjust business strategies accordingly. |
Disruption in Global Trade | With major ports shut down, global trade networks experience disruptions that slow the movement of goods between continents, affecting entire markets and economies. | Consider using multiple ports across different regions to diversify shipping routes. Pre-plan alternative routes for critical shipments and work with freight forwarders to mitigate trade disruptions. |
Impact on Jobs | Prolonged strikes can lead to job losses or reduced hours for workers in industries that rely on port operations, further contributing to an economic slowdown. | Stay informed about local economic conditions and labor market changes. Consider adjusting your workforce plans if prolonged strikes appear likely. |
Currency Fluctuations | A major disruption to global trade can lead to currency fluctuations, particularly in export-driven economies where goods can't be shipped on time, affecting exchange rates and trade balances. | Monitor currency markets and consider using hedging strategies to protect your business from adverse exchange rate fluctuations during prolonged strikes. |
Port strikes, while disruptive, don’t have to bring your operations to a halt. By taking a proactive approach—developing contingency plans, communicating effectively, managing costs, and staying informed—you can reduce the impact of strikes on your supply chain and business. Understanding the broader economic implications helps prepare you for potential long-term effects, while flexibility in your operations ensures you can pivot when needed. With the right strategies, ship and fleet owners can navigate these challenges and keep their businesses running smoothly, even in turbulent times.
Additional References
Federal Maritime Commission (FMC) - Port Disruptions and Remedies
- The FMC provides guidelines and regulatory insights on how port disruptions, such as strikes, affect maritime commerce and what steps can be taken to mitigate these disruptions.
https://www.fmc.gov/
International Maritime Organization (IMO) - Global Supply Chain and Shipping Guidelines
- The IMO is a specialized United Nations agency responsible for the safety and security of shipping. Their resources can help ship owners understand the international regulatory framework during times of port disruptions.
https://www.imo.org/
U.S. Department of Transportation - Maritime Administration (MARAD)
- MARAD provides information and resources related to the U.S. maritime industry, including how port strikes and labor disputes affect national transportation and shipping operations.
https://www.maritime.dot.gov/
National Labor Relations Board (NLRB) - Worker Strikes and Employer Rights
- The NLRB provides guidance on the legal framework surrounding strikes, including workers' rights and the legal obligations of employers during labor disputes in industries like shipping and logistics.
https://www.nlrb.gov/
International Longshore and Warehouse Union (ILWU)
- The ILWU represents dock workers and provides updates on labor negotiations and strike actions. Monitoring their website helps ship owners stay informed about labor disputes at key ports.
https://www.ilwu.org/
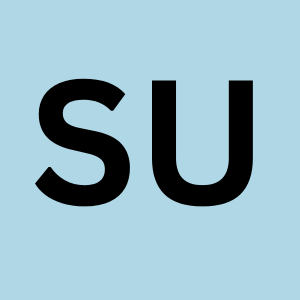
Do you have a Maritime Product or Service that may be of interest to Shipowners? Tell us about it here!
Do you have feedback or insights? Please reach out to editor @ shipuniverse.com