The 7 Key Types of Corrosion on Ships: How They Happen, Where They Strike, and What to Do About It
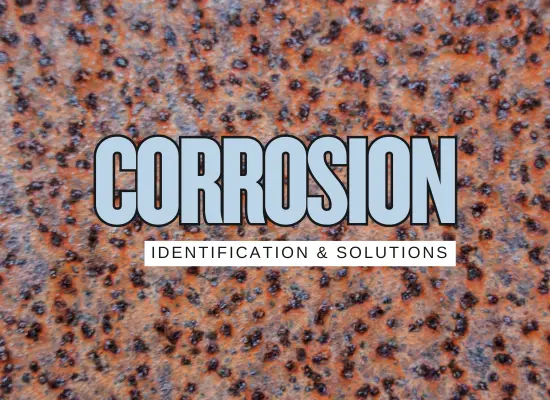
Corrosion might start small—but left unchecked, it can tear through steel, breach critical systems, and cost ships millions in repairs and downtime. It’s one of the most persistent and expensive threats in maritime shipping, and no vessel is immune. From ballast tanks to propeller shafts, corrosion finds its way into every corner of an ocean-going ship.
But not all corrosion is the same.
Here are the main 7 types of corrosion that every shipowner, engineer, and fleet manager should know—what causes them, where they strike, how to prevent them, and what to do if they show up.
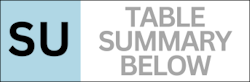
We welcome your feedback, suggestions, corrections, and ideas for enhancements. Please click here to get in touch.
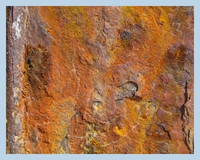
- Outer hull plating constantly in contact with seawater
- Ballast tanks with improper coatings or poor maintenance
- Decks and topsides exposed to rain, spray, and UV
- It weakens structural integrity across wide areas without showing dramatic signs early on
- Often goes unnoticed until thickness is reduced to a dangerous level
- Increases drydock intervals and accelerates need for steel replacement
- Rusty discoloration, scaling, or flaking metal
- Widespread paint breakdown or surface roughness
- Ultrasonic thickness measurements showing metal loss
- Use high-quality marine-grade coatings and ensure full surface coverage
- Apply and maintain cathodic protection (zinc or aluminum anodes)
- Schedule routine inspections and hull cleanings—don’t rely on drydock alone
- Remove corrosion via blasting or mechanical methods
- Replace or weld steel where thinning exceeds safe limits
- Recoat with corrosion-resistant primers and topcoats
- Routine prevention is inexpensive compared to structural steel repair
- Monitoring + early repainting can extend drydock intervals and lower lifecycle cost
- Fixing widespread uniform corrosion may require costly steel replacement and extended drydock time
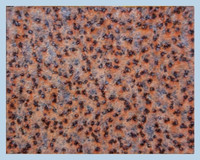
- Ballast tanks and cargo holds with stagnant water pockets
- Hull areas beneath marine growth or biofouling
- Under deteriorated coatings or paint blisters
- Pits can perforate hulls, tank walls, or pipes without visible surface damage
- Once initiated, pits grow rapidly and are difficult to stop
- Often leads to unplanned drydock or costly emergency repairs
- Localized rust spots, often surrounded by intact coating
- Blistering or bubbling paint that lifts off the surface
- Detected using close-up ROV surveys, UT testing, or after cleaning marine growth
- Use high-quality anti-fouling and epoxy coatings, especially in ballast tanks
- Ensure proper surface prep before coating application
- Regularly inspect high-risk areas and keep surfaces clean of deposits
- Grind out or gouge individual pits and weld over if structurally needed
- Replace heavily pitted sections of plating or pipework
- Thoroughly clean, prime, and recoat affected areas with corrosion inhibitors
- Preventive coatings and inspection routines are cost-effective
- Failure to detect pits early can lead to leaks, flooding, and drydock-level repairs
- Fixing pitting often requires welding or cutting out and replacing affected steel
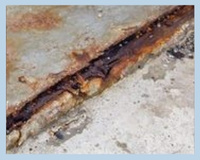
- Bolted joints and riveted connections
- Gasketed areas and lap joints
- Seams in ballast tanks and piping systems
- Often remains hidden until structural failure occurs
- Weakens fasteners, plates, and piping, leading to leaks
- Can rapidly spread if not detected early
- Localized rust streaks around bolted connections
- Sealant or paint discoloration near joint areas
- Deep material loss found in close-up inspections
- Use corrosion-resistant fasteners and welded seams instead of rivets
- Apply sealants and coatings to protect potential crevice areas
- Ensure regular cleaning and drainage of water-trapping gaps
- Remove affected fasteners or components and inspect for deeper damage
- Replace or re-weld corroded sections
- Apply protective coatings and seal crevices to prevent recurrence
- Preventive sealants and coatings are cost-effective
- Neglected crevice corrosion can lead to significant repair costs
- Fixing advanced cases often requires removing and replacing entire assemblies
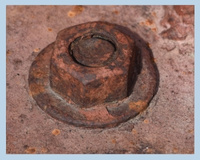
- Steel hulls with bronze propellers or fittings
- Aluminum components in contact with stainless steel fasteners
- Bolted joints using dissimilar metals in marine environments
- Causes rapid deterioration of the less noble (anodic) metal
- Often weakens fasteners and structural connections
- Can go unnoticed until severe metal loss occurs
- Severe corrosion around bolts, rivets, or joints of different metals
- One metal degrading while the other remains intact
- Accelerated corrosion near sacrificial anodes
- Use sacrificial anodes (zinc, aluminum) to absorb corrosion
- Electrically isolate different metals using coatings or gaskets
- Ensure proper material selection to avoid risky metal pairings
- Replace heavily corroded fasteners, bolts, or affected structures
- Apply insulating materials to break electrical contact between metals
- Reapply protective coatings and install proper cathodic protection
- Preventive measures (sacrificial anodes, coatings) are affordable
- Severe cases may require replacing large metal structures
- Improperly managed galvanic corrosion can cause catastrophic failures
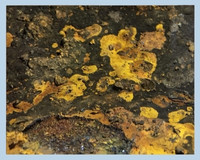
- Ballast tanks with stagnant water
- Fuel tanks and piping systems
- Hull areas affected by biofouling
- Can cause rapid, unpredictable corrosion
- Weakens structural integrity in hidden areas
- Often leads to leaks and system failures
- Slime-like biofilm on metal surfaces
- Pitting corrosion in oxygen-starved areas
- Unusual corrosion patterns in tanks and pipes
- Use biocides and antimicrobial coatings
- Regularly clean and flush ballast and fuel tanks
- Improve drainage and aeration in enclosed spaces
- Remove biofilm through chemical or mechanical cleaning
- Replace severely corroded sections
- Apply protective coatings and use corrosion inhibitors
- Routine cleaning and biocide treatments are cost-effective
- Failure to manage MIC can result in major tank or pipe failures
- Advanced cases may require extensive replacement of affected systems
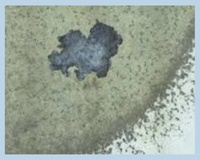
- Near electric thrusters and propeller shafts
- Areas with improper grounding on hull plating
- Metal components near ICCP anodes
- Corrodes metal at an accelerated rate
- Often unpredictable and severe
- Can compromise critical ship systems if undetected
- Highly localized, deep pitting
- Occurs near electrical sources or grounding points
- Damage is often concentrated and irregular
- Ensure proper grounding of electrical systems
- Regularly inspect ICCP systems for unintended leaks
- Use insulated mounts for electrical equipment near metal
- Identify and eliminate stray electrical currents
- Replace heavily corroded metal sections
- Apply protective coatings to vulnerable areas
- Routine electrical system checks help prevent costly damage
- Unresolved stray current corrosion can lead to major hull repairs
- Fixing electrical grounding issues is typically less expensive than structural damage repairs
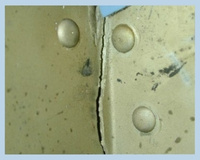
- Welded and riveted joints under constant stress
- High-strength alloys exposed to seawater
- Superstructures, piping, and pressure vessels
- Can cause sudden structural failure without warning
- Cracks often form internally before appearing on the surface
- Frequently occurs in high-stress areas, making repairs difficult
- Fine cracks forming along welds or stress points
- Metal failure with little to no prior corrosion signs
- Detected through dye penetrant or ultrasonic testing
- Use corrosion-resistant alloys for high-stress components
- Apply stress-relief treatments during fabrication
- Regularly inspect welds and structural joints for early cracks
- Remove and replace cracked sections to prevent propagation
- Apply post-weld heat treatments to reduce residual stress
- Use protective coatings to shield against corrosive environments
- Preventive material selection and stress-relief treatments add upfront costs
- Undetected SCC can lead to major safety risks and expensive repairs
- Fixing SCC typically requires full structural component replacement
Table Summary
ShipUniverse: Summary of 7 Key Corrosion Types on Ships | |||
Corrosion Type | How It Happens | Where It Strikes | Common Solutions |
Uniform Corrosion | Even metal loss across surfaces due to constant exposure to seawater and oxygen. | Hull plating, ballast tanks, deck surfaces | Use high-quality coatings, apply cathodic protection (zinc anodes), and schedule regular inspections. |
Pitting Corrosion | Localized, aggressive corrosion forming deep pits, often under coatings or in stagnant water. | Ballast tanks, hull areas under marine growth, cargo holds | Use high-performance coatings, ensure proper surface prep, and keep water circulation active to prevent stagnation. |
Crevice Corrosion | Forms in narrow, oxygen-starved gaps where seawater gets trapped, accelerating metal loss. | Bolted joints, gaskets, lap joints, ballast tank seams | Use corrosion-resistant fasteners, seal joints properly, and perform regular cleanings. |
Galvanic Corrosion | Occurs when two dissimilar metals are in contact in seawater, causing one to corrode faster. | Steel hulls with bronze propellers, aluminum structures with stainless steel bolts | Use sacrificial anodes, apply insulating coatings, and avoid risky metal pairings. |
Microbiologically Influenced Corrosion (MIC) | Caused by bacteria or fungi that produce corrosive byproducts, leading to metal loss. | Ballast tanks, fuel tanks, piping systems | Use biocides, clean and flush tanks regularly, and improve drainage. |
Stray Current Corrosion | Caused by unintended electrical currents flowing through ship metal, accelerating corrosion. | Near electric thrusters, hull plating, improper grounding areas | Ensure proper grounding, inspect electrical systems, and isolate electrical equipment from metal surfaces. |
Stress Corrosion Cracking (SCC) | Cracking caused by tensile stress combined with exposure to corrosive environments. | Welded joints, pressure vessels, high-stress structural components | Use corrosion-resistant alloys, apply stress-relief treatments, and inspect high-stress areas regularly. |
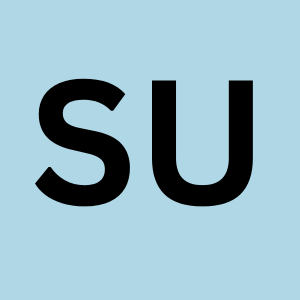
Do you have a Maritime Product or Service that may be of interest to Shipowners? Tell us about it here!
Do you have feedback or insights? Please reach out to editor @ shipuniverse.com