Top 20 Time-Saving Maintenance Tips for Maritime Vessels
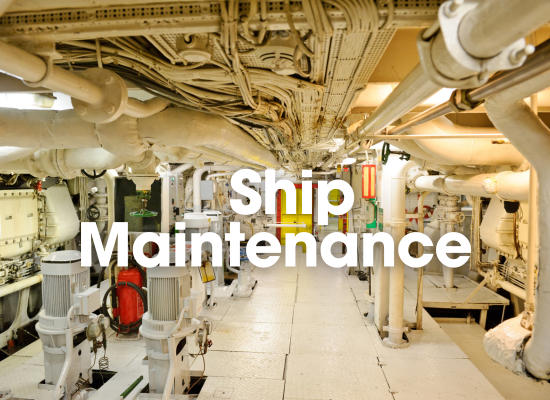
In the fast-paced world of maritime shipping, efficiency isn’t just a goal; it’s a necessity for staying competitive and profitable. Effective maintenance of vessels not only ensures operational reliability but also significantly impacts the speed and cost of maritime operations. Below we explore 20 time-saving maintenance tips designed to streamline processes on maritime vessels. These tips range from leveraging advanced technologies to adopting strategic operational practices, all aimed at minimizing downtime and maximizing productivity for ship owners and fleet managers.
* Please send feedback/suggestions to editor @ shipuniverse.com
1. Implement Predictive Maintenance Technologies
- Overview: Utilize sensors to predict equipment failures before they occur.
- Time to Implement: Setup can take a few weeks to integrate with existing systems.
- Cost: High initial investment, but significant long-term savings in reduced downtime.
- Impact: Minimizes unplanned maintenance and extends the life of machinery.
2. Schedule Regular Dry Docking Strategically
- Overview: Plan and execute dry docking when it aligns with slower business periods to minimize impact.
- Time to Implement: Planning should start at least 6 months in advance.
- Cost: Considerable, depending on the scope of work and dock location.
- Impact: Ensures thorough maintenance without disrupting peak operational times.
3. Standardize Parts Across the Fleet
- Overview: Use standardized parts for the same type of equipment across all vessels.
- Time to Implement: Can be implemented gradually as parts need replacement.
- Cost: Moderate upfront costs for inventory but reduced costs over time due to bulk purchasing and reduced variability.
- Impact: Streamlines repairs and maintenance, reducing time spent sourcing and replacing parts.
4. Train Crews in Basic Onboard Maintenance
- Overview: Equip crew members with the skills to perform routine maintenance and minor repairs.
- Time to Implement: Ongoing training sessions; initial basic training could be completed in a few weeks.
- Cost: Regular training costs, potentially offset by reduced need for specialist intervention.
- Impact: Keeps the vessel running smoothly with less downtime waiting for external maintenance help, enhancing operational readiness.
5. Utilize Mobile Maintenance Units
- Overview: Deploy mobile maintenance teams equipped with necessary tools and parts to address issues across the fleet quickly.
- Time to Implement: Setup for initial teams can take 1-2 months, depending on existing infrastructure.
- Cost: High initial setup cost, but cost-effective in reducing vessel downtime and travel costs for repairs.
- Impact: Reduces wait times for repairs, allowing for quicker resolutions and less downtime.
6. Digital Maintenance Logs
- Overview: Shift from paper-based logs to digital systems to track maintenance history and schedule future tasks efficiently.
- Time to Implement: Digital system setup can be completed within a month.
- Cost: Moderate investment in software and training, offset by gains in efficiency and accuracy.
- Impact: Provides real-time updates and reminders, reducing the chance of missed maintenance tasks and improving long-term vessel health.
7. Implement Lean Maintenance Procedures
- Overview: Apply lean principles to maintenance routines to eliminate unnecessary steps and focus on value-adding activities.
- Time to Implement: Several months to analyze current procedures, design new workflows, and train staff.
- Cost: Costs are primarily related to training and initial analysis but generally low compared to the savings in time and resources.
- Impact: Streamlines maintenance processes, reducing time and costs while maintaining or improving quality.
8. Outsource Specialized Maintenance Tasks
- Overview: Contract out highly specialized or infrequent maintenance tasks to expert service providers.
- Time to Implement: Can be arranged as needed; setup a roster of trusted contractors in advance.
- Cost: Variable; potentially higher cost per service but overall cost-effective by avoiding the need for in-house specialists.
- Impact: Ensures high-quality maintenance while freeing up internal resources for more routine tasks.
9. Fast-Response Repair Kits on Board
- Overview: Equip ships with comprehensive repair kits that include essential tools and components for common breakdowns.
- Time to Implement: Can be assembled and deployed within a few weeks.
- Cost: Moderate initial investment in tools and parts, which could save significantly on emergency repair costs.
- Impact: Enables immediate in-house responses to small and medium issues, reducing downtime waiting for external help.
10. Seasonal Maintenance Planning
- Overview: Schedule maintenance activities based on seasonal variations in shipping schedules and weather conditions.
- Time to Implement: Requires annual planning, aligning with seasonal business cycles.
- Cost: Costs vary by task but overall efficiency in planning reduces unexpected expenditures.
- Impact: Prevents weather-related damages and optimizes downtime during slower seasons, ensuring peak readiness.
11. Remote Monitoring Systems
- Overview: Install sensors and systems to monitor the condition of critical ship systems remotely.
- Time to Implement: Implementation can take 1-3 months depending on the complexity of the system.
- Cost: High initial setup cost, but can reduce long-term maintenance and operational costs.
- Impact: Allows for real-time data analysis and preemptive maintenance actions, significantly reducing breakdown risks.
12. Consolidated Vendor Management
- Overview: Centralize maintenance service providers to simplify management and potentially leverage bulk discounts.
- Time to Implement: A few months to select providers and negotiate contracts.
- Cost: Costs associated with vendor analysis and negotiations, offset by potential long-term savings from streamlined operations.
- Impact: Reduces administrative overhead and strengthens bargaining power with vendors for better service terms and costs.
13. Enhanced Training Simulations
- Overview: Use virtual reality (VR) and other simulation tools to train crew on maintenance procedures without the need for physical presence.
- Time to Implement: Setting up a VR training program can take 1-2 months.
- Cost: Significant initial investment in VR equipment and software development, but reduces training costs over time.
- Impact: Provides hands-on training that enhances skill development and readiness, reducing errors and speeding up actual maintenance work.
14. Modular Equipment Design
- Overview: Implement modular designs for critical systems to simplify replacements and repairs.
- Time to Implement: Long-term integration, depending on refit schedules and new equipment purchases.
- Cost: High initial cost for modular system design and acquisition, offset by quicker, cheaper repairs and upgrades.
- Impact: Reduces downtime during repairs and allows for quicker updates to technology, keeping systems at peak efficiency.
15. Scheduled Downtime Optimization
- Overview: Analyze operational data to pinpoint the optimal times for scheduled downtime that minimizes impact on operations.
- Time to Implement: Requires ongoing data analysis with initial setup taking a few weeks to months.
- Cost: Moderate cost for data analysis tools and software, with significant potential savings in operational efficiency.
- Impact: Ensures maintenance is performed during the least disruptive periods, maintaining higher operational availability.
16. Eco-friendly Cleaning Agents
- Overview: Use biodegradable and eco-friendly cleaning agents for routine maintenance to reduce environmental impact and potential regulatory issues.
- Time to Implement: Immediate implementation once suitable products are sourced.
- Cost: Comparable to traditional cleaning agents, with potential for cost savings in waste disposal and environmental compliance.
- Impact: Enhances the ship’s environmental profile and reduces the risk of penalties associated with the release of harmful substances.
17. Advanced Corrosion Protection Techniques
- Overview: Implement advanced coatings and anode systems to protect against corrosion, extending the lifespan of vessel components.
- Time to Implement: Application and setup can take a few weeks during scheduled maintenance.
- Cost: High initial cost for advanced materials, but significantly reduces the frequency and cost of future repairs due to corrosion.
- Impact: Extends the durability of ship structures and systems, reducing long-term maintenance needs and costs.
18. Automated Inventory Management for Spare Parts
- Overview: Use automated systems to manage inventory levels of spare parts, ensuring availability without overstocking.
- Time to Implement: Several months to integrate systems and optimize inventory.
- Cost: Moderate investment in inventory management software, offset by reductions in tied-up capital and storage needs.
- Impact: Ensures parts are available when needed without unnecessary delays, optimizing repair times and reducing excess inventory costs.
19. Quick-release Fasteners for Easy Access
- Overview: Utilize quick-release fasteners in machinery and panels to allow faster access during maintenance checks.
- Time to Implement: Can be implemented during regular maintenance cycles within a few months.
- Cost: Low to moderate cost depending on the scale of implementation.
- Impact: Reduces time required for opening and securing equipment, speeding up both inspections and repairs.
20. Integrated Maintenance and Operation Software
- Overview: Implement comprehensive software that integrates maintenance schedules with operational data for optimal planning.
- Time to Implement: Requires several months for software customization and integration.
- Cost: Significant initial investment in software development and training.
- Impact: Provides a holistic view of operations and maintenance needs, enabling proactive maintenance planning and reducing downtime.
Adopting these 20 maintenance strategies can transform the way maritime operations are conducted, leading to significant time and cost savings. By integrating predictive maintenance technologies, optimizing scheduled downtime, and employing advanced materials and techniques, ship owners can enhance their fleet’s efficiency and extend the operational lifespan of their vessels. These improvements are not just about saving time; they contribute to a more sustainable and economically sound maritime future. Embracing these practices will ensure that maritime operations can stay ahead in a competitive industry, where efficiency and reliability are paramount.
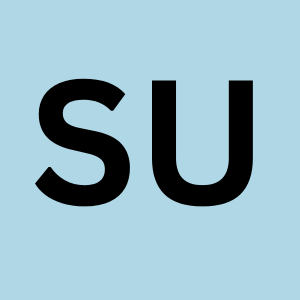
Do you have a Maritime Product or Service that may be of interest to Shipowners? Tell us about it here!
Do you have feedback or insights? Please reach out to editor @ shipuniverse.com